Data centers are often thought of as the backbone of the internet, and for good reason. Without data centers, we would not be able to store or access the massive amounts of data that are generated every day.
They are becoming increasingly important in the Middle East as the region’s economies transform digitally. In this article, we discuss key points you need to know about data centers in the Middle East and how Agility can help data center operators grow faster in the region.
What are data centers and what services do they offer?
Data centers are facilities that house computer systems and their associated components, such as telecommunications and storage systems, including servers, etc. Data centers typically require a large amount of power to operate and need to be located near robust telecommunications infrastructure to ensure the speed of data transmission.
Data centers offer a variety of services that can help businesses with their data storage and processing needs. They can provide storage space for data, as well as the infrastructure needed to process and manage it.
Data centers can also offer tools and services to help businesses analyze their data and make decisions about how to use it. In addition, data centers can provide access to high-speed networks and computing resources that can help businesses with their data-intensive tasks. Artificial intelligence (AI) and machine learning (ML) are two examples of use cases.
Data centers are critical infrastructures for many organizations. They store and manage data, applications, and other resources that are essential to the operation of the business. Data centers are used by companies of all sizes, from small businesses to large enterprises. They play a vital role in supporting mission-critical applications and services.
There are many different types of data centers, ranging from small facilities to large hyperscale data centers. The type of data center that an organization needs depends on its specific requirements.
Small and medium-sized businesses typically use colocation data centers. In a colocation data center, the customer rents space from a service provider and uses the service provider’s infrastructure to house its servers and other IT equipment.
Large enterprises often build their own data centers. These data centers are designed to meet the specific needs of the enterprise, such as accommodating a large number of users or supporting high-performance applications.
Hyperscale data centers are the largest and most powerful type of data center. They are designed to support the massive scale of operations of hyperscale companies, such as Google, Facebook, and Amazon.
What is driving the growth of data centers in the Middle East?
There are several factors driving the growth of data centers in the Middle East, including:
- Data sovereignty laws mandate that certain categories of data – e.g. government and certain personal data of citizens and residents – be resident in the country
- Migration to the cloud for hosting data by both governments and enterprises in the region
- Rising consumption of data by consumers driven by the growth of 4G or 5G services from telecom companies and the usage of applications that leverage artificial intelligence (AI)
- Growing connectivity of subsea cables to countries in the region enables larger flows of data from the country globally
- Lower latency requirements from streaming applications like Netflix and other so-called Over-the-Top media services (OTTs).
What is the current data center market size and what are the forecasts for growth?
The colocation market in the six Gulf Cooperation Council (GCC) data centers in the Middle East is forecasted to grow 2.2 times by 2025 from 383 MW of IT load to an estimated 839 MW of IT load, demonstrating the large investment that is going into this sector.
Some commentary from the Gulf Data Center Association (GDCA) on the 6 GCC markets in the Middle East:
Saudi Arabia – The largest economy in the region is seeing a lot of growth in data center activity.
- The government continues to offer strong support for data centre growth. The Ministry of Communications and Information Technology (MCIT) recently called for an $18 Billion investment in hyperscale data centers and renewable energy by 2030 to take total capacity to more than 1.3GW and transform Saudi Arabia into the main data center hub for the region.
- With a population approaching 35 million, there is a large domestic demand which has been reinforced by recent data protection laws that place tight restrictions on the transfer of data outside of the country. Saudis are avid users of social media and consumers of online content. Notably, Saudi Arabia is becoming a global hub for esports and gaming.
- Saudi Arabia has 16 in-service subsea cables, which places it as one of the highest amongst other GCC countries in terms of connectivity. The 2Africa cable, which will be the longest subsea cable ever developed and is expected to come into operation by the end of next year, has four cable landing points in Saudi Arabia. Google’s Blue Raman cable, which will connect Europe to the Middle East and India without going through the Gulf of Suez, includes a future cable landing point in Duba on the Red Sea.
- Whilst Riyadh, Jeddah, and Dammam remain the three main clusters for data center development, the government is pushing ahead with the development of Neom. As an early deployment in the development of the city, Neom is building a 12MW data center facility, with Oracle announced as the first tenant.
UAE – The UAE has led the GCC region in terms of data center capacity, variety of data center operators, and future growth ambition for many years.
- The market has remained attractive with its tech-hungry and growing population, as well as Dubai’s position as a major international business and trading hub.
- The UAE has worked hard to improve its international and regional connectivity, now being served by 17 international subsea cables, whereas a decade ago, this number was significantly lower.
- Multiple hyperscale cloud providers are now present, including AWS, Microsoft, Google, and Alibaba. AWS’s recent launch of their own data centers in the UAE reflects the country’s rapid uptake of cloud services, with most Government entities, large enterprises, and SMEs using cloud services already or are in advanced stages of actioning a migration plan.
Qatar – Demand for data center requirements in Qatar received a big boost ahead of the World Cup last year, which saw massive investment into new infrastructure to support the global sporting event.
- Until recently, the market in Qatar was limited to just two operators offering colocation services, namely Meeza and Ooredoo. However, with the entry of cloud providers Microsoft and Google, the market has shifted into another phase of development, with a number of international operators now actively looking at Qatar for opportunities to offer build-to-suit facilities, which is opening up the market to potential new entrants.
- Qatar was the first country in the world to launch 5G services back in 2018. It has the cheapest power costs for businesses in the GCC and has the highest per capita levels in the region.
- Qatar is making big efforts to diversify the economy away from its past reliance on oil and natural gas as well as develop more sustainable sources of energy. Large-scale solar projects are now in operation with the 800 MW Al Kharsaah project, with a further 800MW of solar output in the pipeline to be developed by 2024.
Kuwait – The Kuwaiti data center market was limited to a handful of players offering retail colocation, but Google will be the first hyper scaler to enter the market.
- The known providers are Zain, Ooredoo (formerly Fast Telco), Kalaam (formerly Zajil), and Solutions by STC (formerly Quality Net). These are all telecom companies that have built additional colocation data center space alongside their own needs. The majority of these facilities are built in their own headquarters occupying a couple of floors in each building. Smaller hosting businesses have taken space within the Tec Building tower, which is home to Kuwait’s cable landing station.
- The rest of the market currently lies within enterprise facilities – in particular, the financial services sector, which continues to invest in enterprise facilities. ITU built a 1,200 sqm data center with over 500 servers for Kuwait Finance House in 2021.
- The market has recently seen an increase in cloud requirements as businesses look to migrate to the cloud. However, the market has struggled to expand to support new requirements and, as a result, has seen some requirements go to neighboring GCC markets. For example, Batelco has an alliance with Ooredoo, and its Global Zone data center in Bahrain is made available to support Global Zone Kuwait.
- There have been multiple attempts by the existing providers (along with a few other GCC operators) to build new facilities. However, difficulties in finding logistics space and securing sufficient power have halted most progress.
- Google is opening a cloud region in Kuwait – the first hyper scaler in the country. Google is working closely with the government as part of a strategic partnership to help promote further digital transformation in the economy and meet the goals set out in the 2035 Kuwait Vision Plan. This includes further development and availability of e-services. Mastercard, for example, has collaborated with Google to recently launch Google Pay in Kuwait.
- The new cloud region has led to a requirement for data center development which has heightened interest levels from a number of international wholesale operators. However, finding suitable sites for data centers and navigating the approval process has so far proved challenging.
- Agility Logistics Park (ALP), one of the largest real estate owners of warehousing and industrial land, has announced plans to deploy data center campuses across several Middle East and African countries, including one on a site in Kuwait next to a major substation.
Bahrain – The Bahrain data center market has managed to attract some major wins over the past few years
- Names such as AWS, Tencent, and the recent announcement of a major data center campus with STC prove that there is significant confidence in this market.
- Confidence stems from an active and supportive Government with regard to data centers, along with a geopolitical climate that is widely considered to be stable and safe
- Bahrain’s attributes include an open telco market, a reputation as an easy place to do business, and lower operating costs compared to other GCC countries.
- Taking advantage of its geographical position, the Bahraini market is working hard to position itself as a central Gulf location that can manage a wide range of requirements, including disaster recovery, regional cloud deployments such as cloud gaming, and a keen interest in financial markets and fintech.
- The government of Bahrain continues to support data center opportunities via the Economic Development Board of Bahrain (EDB Bahrain). This is in keeping with the Kingdom’s Cloud First policy, introduced in part to reduce the cost of Government I.T. infrastructure.
- Tencent Cloud announced plans that it would build its first data center in Bahrain, which could make it the second cloud player to do so after AWS established its availability zone in the Kingdom of Bahrain in 2019.
Oman – Oman has the highest number of subsea cables in the GCC with 14 currently in operation and a further 4 planned.
- Omantel is the main telecom company in the country and has a joint venture with 4Trust that operates Oman Data Park which has several facilities in Wattayah, Knowledge Oasis Muscat and Duqm. Last year, Oman Data Park announced plans to build a data centre in Zanzibar.
- Oman has set a target of 30% of all power to come from renewable sources by 2030 with a number of large-scale solar and wind projects in the pipeline.
- The capacity of the sector in Oman is undergoing a growth phase with a number of data centres under construction. In the past, many companies used their own in-house facilities but demand for colocation is rising with migration to the cloud.
- Oman has three free trade zones (Al Mazunah, Sohar and Salalah) and two special economic zones (Duqm and Knowledge Oasis Muscat). Various incentives are on offer to help attract inward investment including allowing 100% foreign ownership of companies. Last year, the Sohar Free Zone agreed to lease 25,000 sqm of land to a Chinese firm to build a cloud data centre.
- At the end of 2022, the Ministry of Transport, Communications and Information Technology (MTCIT) signed an MoU with AWS to launch a local zone for cloud hosting in Muscat. Oman is the first country in the MENA region to host an AWS local zone after its launch in the US and other cities in the world.
What are the challenges to the development and operation of data centers in the Middle East?
There are several challenges to the development of data centers in the Middle East, including:
- Land acquisition – securing sites with the appropriate land use/zoning at the right location with proximity to power and fiber connectivity
- Permitting – securing the permits for building and operating a data center
- Power – securing large amounts of power, preferably from green sources
- Talent – Given this is a rapidly growing industry, there is a dearth of talent across the value chain in the industry in this region
How Agility can help enable data center operators to grow faster
Agility Logistics Parks (ALP), the leading private owner and developer of industrial real estate in the Middle East & Africa, has a portfolio of data center campuses, which are sites with substantial power and utilities (including renewable energy), building permits, and regulatory approval, to accelerate time-to-market for data center developers.
ALP has four decades of expertise in land acquisition and development in emerging markets and is a strong institutional partner for data center developers looking to deploy capacity rapidly across the Middle East.
ALP’s value proposition is speed to market in a de-risked manner in complex, challenging emerging markets leveraging several capabilities:
- Land acquisition – Large sites with title secured. Prime locations. Master planned and tailored for hyperscale clients and operators.
- Power & utilities – All sites already have secured multi-megawatt scale power availability with expansion opportunities.
- Fiber connectivity – Fiber connectivity from two POPs to all sites. Large fiber strand count
- Authority approvals – Ability to secure permitting and approvals for large complex projects in all markets
- Regulatory approvals – Ability to help secure proper regulatory approvals to operate in the local market.
- Construction expertise – Proven local construction and project management expertise. Pre-qualified vendors and ecosystem.
- Sustainability – Renewable energy sources available for all sites. Solar is available for all sites. Hydroelectric is the main power source for Ghana.
- Security & operations – Proven security and facilities operations support expertise in all markets.
The first two data center sites that ALP has brought to market are in Kuwait and Riyadh, Saudi Arabia:
- Kuwait – More than 100,000 sqm of land with 80+ MW of power available today with under a millisecond latency connectivity to the cable landing station. Solar power is available.
- Riyadh – 82,000 sqm of land available and 25+ MW available. Solar power is available.
ALP is looking to add more sites in Saudi Arabia and the UAE in response to strong demand from data center operators.
Connect with Agility’s data center campuses team for further information.
Last-Mile Logistics and Warehousing in the Middle East
Last-mile delivery and warehousing refer to the process of delivering goods from a central location to final destinations, typically customers’ homes or businesses. This can be done via various means, including ground transportation, airfreight, or even waterways. In most cases, last-mile delivery is handled by third-party logistics providers (3PLs) who specialize in this type of service.
The term last-mile delivery is often used in connection with e-commerce, as it refers to the final stage of delivering goods ordered online to the customer’s doorstep. This has become an increasingly important aspect of online retail as customers expect ever-faster delivery times.
The term warehousing refers to the process of storing goods in a central location before distribution. This can be done for a variety of reasons, including inventory management, order fulfillment, or even seasonal fluctuations in demand. Warehousing is typically handled by 3PLs who have access to large, centrally located facilities.
The Middle East is home to a growing number of e-commerce businesses and consumers. This has created a demand for last-mile delivery, parcel shipping, and warehousing services in the Middle East. Here, we discuss everything you need to know about these supply chain concepts in the region.
Last-Mile Delivery’s Service Development in the GCC
The GCC region is one of the most important logistics markets in the world. Its well-developed infrastructure and large population make it a prime target for last-mile delivery services. In recent years, we have seen a significant increase in the number of last-mile delivery companies operating in the GCC.
The most important factor driving the growth of last-mile delivery in the GCC is the increasing demand for e-commerce. The region has a large and growing population of internet users, and this is translating into greater demand for online shopping. In addition, many of the region’s leading retailers are now offering online shopping platforms, further boosting demand for last-mile UAE delivery services.
Another key factor driving the growth of last-mile delivery in the GCC is the region’s rapidly expanding logistics infrastructure. Because it is home to some of the world’s largest ports and airports, it is easier for delivery companies to move goods around the GCC. This makes it easier for companies to offer same-day or next-day delivery services, which is a significant selling point for customers.
The GCC region is an important market for last-mile delivery companies. The region’s well-developed infrastructure and large population make it an attractive target for these types of businesses. In addition, the region’s expanding logistics infrastructure makes it easier for delivery companies to move goods around. This results in faster delivery times and greater customer satisfaction.
Warehousing Development in the GCC
The GCC has seen a surge in warehousing development in recent years as the region’s economy has grown and diversified. This is driven by a combination of factors, including the expansion of e-commerce and the rise of new industries such as food and beverage manufacturing.
There is now a need for more sophisticated and efficient warehousing solutions to meet the demand from these industries. In response, developers are constructing larger and more modern warehouses that offer a variety of features and amenities.
How Does Warehousing Work/Combine with Last-Mile Delivery?
Warehousing plays an important role in the supply chain process, providing a safe and efficient location to store products until they are needed. But what exactly does warehousing involve? And how does it work alongside last-mile delivery to ensure that products reach their final destination?
In simple terms, warehousing is the storage of goods and materials. This can be done on a short- or long-term basis, depending on the needs of the business. Goods are usually stored in a warehouse until they are needed for distribution or sale or when returns need to be kept to sent back to the retailer.
There are many different types of warehouses, which can be classified according to their purpose, size, or location. For example, some warehouses are used for storage only, while others are used for both storage and distribution. Some warehouses are small, local operations, while others are large, international facilities.
The Evolution of E-Commerce Logistics Services
The internet has drastically changed the way businesses operate. In the past, companies would rely on brick-and-mortar locations to reach their customer base. Today, businesses of all sizes are tapping into e-commerce growth in the Middle East and leveraging the power of e-commerce to reach a global audience.
As the world of business has changed, so has the logistics field. E-commerce logistics is the process of planning, executing, and controlling the transportation and storage of goods in support of online sales. This type of logistics has evolved rapidly in recent years to keep up with the changing business landscape.
Advantages of Modern Technology For E-Commerce Businesses
Technology has brought about a revolution in the way businesses operate. E-commerce businesses have significantly benefited from the use of modern technology. Some advantages of using modern technology for e-commerce businesses are:
Increased Customer Reach
The reach of e-commerce businesses has increased manifold with the help of technology. Businesses can now reach out to customers worldwide and make deliveries overseas with the use of the internet.
Cost-effective
Technology has made it possible for firms to reduce their operating costs. E-commerce businesses can now reach out to customers at a fraction of the cost of traditional marketing methods.
Increased Efficiency
The use of technology has made businesses more efficient. Businesses can now track customer behavior and preferences with the help of technology. This tracking opportunity helps businesses customize their offerings and provide a better experience to their customers.
Improved Customer Service
E-commerce businesses can now offer 24/7 customer support and resolve queries quickly.
Increased Sales
Because companies can now provide a better shopping experience to their customers and persuade them to make a purchase, technology is paving the way for e-commerce retailers to increase their sales and boost their bottom line.
E-Commerce Fulfillment Warehousing and Last-Mile Delivery
E-commerce fulfillment warehousing and last-mile delivery are two of the most essential pieces of the e-commerce puzzle. Without a well-functioning warehouse and delivery system, your online business will struggle to meet customer expectations and compete with other businesses.
There are a few things to consider when setting up an e-commerce fulfillment system, including:
- The type of products you sell
- Your customer base
- Your budget
The type of products you sell will dictate the size and layout of your warehouse. If you sell large items, you’ll need a larger space with high ceilings and room for forklifts or other heavy machinery. If you sell smaller items, you can get away with a smaller space.
Your customer base will dictate your delivery options. If you sell to customers in a specific region, you’ll need to set up a local delivery system. If you sell to customers across the country, you’ll need to ship your products via UPS, FedEx, or another shipping company.
How an E-Commerce Warehouse is Different From a Traditional Warehouse
The most significant difference between an e-commerce warehouse and a traditional warehouse is how orders are processed. In a traditional warehouse, orders are typically processed manually, with workers picking items off shelves and packaging them up for shipment. In an e-commerce warehouse, orders are typically processed automatically, with items being retrieved from storage and placed onto conveyor belts or other automated shipping systems.
Another difference between an e-commerce warehouse and a traditional warehouse is the way in which inventory is managed. In a traditional warehouse, inventory is typically managed manually, with workers tracking what items are in stock and what needs to be ordered. In an e-commerce warehouse, inventory is typically managed automatically, with computerized systems keeping track of items in stock and what needs to be ordered.
E-commerce warehouses are typically much larger than traditional warehouses due to the need to store more inventory. They are also often located near major transportation hubs, such as airports or rail yards, to facilitate the speedy shipping of orders.
By Tarek Sultan
Vice-Chairman of the Board, Agility
- Investment is pouring into Gulf startups from domestic and foreign sources.
- Start-up friendly policies, access to funding and the multiplier effect are just a few of the reasons for this growth in investment.
- Powerful local and global economic currents are benefitting the Gulf states.
This is a golden age for startups and entrepreneurs in the six countries of the Gulf Cooperation Council (GCC). Geopolitics, technology, climate urgency and daring national agendas across the region have combined to create what might be the most favourable conditions that small businesses anywhere have ever enjoyed.
Private-sector expansion is the key to national ambitions in all six countries. Increasingly, Gulf leaders will be looking to small business and entrepreneurs as engines of job creation and innovation.
The time is right. The ecosystems that Gulf countries established to nurture, fund and scale digital startups are maturing. Gulf funders — from sovereign wealth funds to venture capitalists to family offices — are looking to write checks to entrepreneurs closer to home. Regulatory fine-tuning is creating new openings for smaller companies that have struggled to compete. Massive infrastructure, energy and technology projects are having a spinoff effect for local businesses and specialized service providers. Finally, powerful currents in Gulf trade, foreign investment, research and e-commerce are all working in favour of SMEs.
Five reasons the time is now for startups and small businesses in the Gulf
1. Funding
Simply put, there’s more money from local and international sources looking to invest in young, innovative Gulf companies.
The Gulf’s sovereign wealth funds have more than $4 trillion in assets under management, a record. They account for more than 40% of global SWF wealth, and their investments comprised 40% of the global sovereign investment total through the first nine months of 2024. Increasingly, Gulf fund managers are looking to invest more at home so that they can drive private-sector growth at the heart of the region’s national strategies.
Saudi Arabia’s Public Investment Fund (PIF) is shifting the balance of its portfolio to focus less on international holdings and more on investment in new industries and projects in the Kingdom. PIF Governor Yasir Al-Rumayyan said in October that the fund will trim its global holdings to 18% of its portfolio, down from 30% in 2020.
In other cases, Gulf sovereign funds are putting money into young companies with innovative ideas that can aid home-country economic diversification. Abu Dhabi’s Mubadala recently invested in Odoo, a Belgian company that offers single-platform software for small and medium-sized companies.
Venture capital investment in the GCC quadrupled from 2017 to 2022 and continues to outpace growth in most other geographies, increasing at a 24% compound annual growth rate. Investment is pouring into Gulf startups in AI, specialized online marketplaces, climate tech, delivery apps, fintech, edtech and investment platforms.
At the same time, overseas funds such as US-based ScienceWerx are putting down new roots in Saudi Arabia and neighboring countries so they can be first movers in AI, biotech, healthtech and other emerging fields. Similarly, Brookfield Asset Management says it is raising at least $2 billion for a new Middle East-focused private equity fund with PIF and other partners.
2. Multiplier effects
The vast majority of small businesses in the Gulf aren’t the kind to attract direct investment from sovereign funds and venture capitalists. But most can expect to be lifted by the “agglomeration” or multiplier effect that flows from the staggering amount of investment and spending across the region, particularly in mega-projects, logistics infrastructure, AI, clean energy and climate adaptation.
In the US, where most of the research on multiplier effects has been done, there is a clear correlation between investment and increased demand for local goods and services; increased productivity; and job creation. The addition of one highly skilled job in an urban area creates 2.5 jobs in other sectors dominated by smaller businesses: construction, food service and other localized roles.
3. Regulatory incentives
Gulf governments are using their policy levers to create new jobs, expand private-sector growth and boost investment. Among all the carrots and sticks being deployed by policymakers are loads of advantages and opportunities that benefit smaller businesses. Some examples:
— In the UAE, where there are nearly 50 economic free zones, operators are competing to create the most business-friendly conditions. The Ajman NuVentures Centre Free Zone, the newest in the Emirates, promises to grant business licenses online in 15 minutes and issue two-year visas for investors within 48 hours.
— In Saudi Arabia, one of the main drivers of growth in the small business sector has been the Kingdom’s sweeping push to make it easier and more attractive for women to join the workforce. Since 2017, the Kingdom has lifted the ban on women driving, introduced anti-harassment laws, expanded female legal autonomy, introduced childcare and transportation subsidies for working women, mandated equal pay and prohibited termination of pregnant women. Today, women own 45% of small and medium-sized businesses in Saudi Arabia. The rate of female participation in the labour force roughly doubled to 35% between 2017 and 2023.
— To create jobs for their citizens, Gulf countries are requiring private companies to meet hiring quotas and maintain a certain percentage of nationals in their workforce. In the UAE, small businesses can qualify for grants, subsidies and reduced fees by taking part in labour force Emiratization.
— Saudi Arabia’s Regional Headquarters Programme, intended to get multinationals to establish their regional head offices in the Kingdom, will add to the multiplier effect by sending global companies in search of Saudi partners for everything from local recruiting to branding, advertising and marketing.
4. Promotion and skills development
Gulf countries are getting better at figuring out what startups and small businesses need. Where non-energy exports used to be negligible, they are now aggressively promoted by the Saudis, Emiratis and other GCC governments.
In Kuwait, which licensed 6,700 new companies through the first three quarters of 2024, the National Fund for SME Development recently launched its Mubader Plus programme, offering workshops, counseling and other assistance to budding entrepreneurs.
Dubai’s Expand North Star, with 70,000 in attendance in 2024, is the world’s largest tech startup and investment event.
5. Powerful tailwinds
Gulf leaders are embracing the post-World War II US innovation model, which uses government money to fund university research that can produce ideas later scaled and commercialized by the private sector. GCC countries are establishing or expanding universities and pushing them to innovate through partnerships with leading international research institutions or alongside Gulf counterparts through platforms such as the Qatar-led My Gulf University.
Trade trends are also working in favour of SMEs. The UK and six GCC countries are nearing completion of a new free trade agreement valued at $73 billion annually. A new FTA with the UK is likely to accelerate economic integration among the six countries, as will Gulf e-commerce, which continues to outpace other regions in annual growth.
Not to be overlooked is the China factor. Chinese companies are looking to the Gulf as the place where they can diversify their manufacturing base, invest in renewable energy and hydrogen production and become EV market share leaders. Chinese investment in Gulf-based AI and tech development is making the GCC a hub for digital transformation and commerce.
For entrepreneurs, startups and small business in the GCC, it’s never been a better time.
This blog was originally published by the World Economic Forum.
By Agility Vice Chairman Tarek Sultan
As I head to Saudi’s FII conference, known as “Davos in the Desert” this week, I am reflecting on the pace of change I’ve personally witnessed in KSA.
Saudi Arabia’s progress in its journey to becoming a Tier 1 global logistics hub has been impressive. It’s clear the Kingdom is already ahead of many key targets and on course to meet many more, diversifying its economy and enhancing its global profile.
Agility has been investing in Saudi Arabia for 20 years. The scale, resources, resolve, and pace of reform we have seen in Saudi Arabia in recent years has been particularly exciting. In our view, Saudi Arabia is one of the most attractive markets for logistics investments in the world today.
Agility is investing in KSA around the following areas:
- Building essential infrastructure. We’re building a world-class logistics and distribution park near Jeddah. We’ve committed SAR 611 million ($163 million) to the 570,000 SQM project, an ultra-modern facility to go with the state-of-the-art Agility Logistics Parks already serving Saudi companies and multi-nationals in Riyadh and Dammam.
- Improving Air Travel. Our Menzies Aviation business is the world’s largest aviation services company. It has partnered with Saudi Logistics Services (SAL) to improve passenger services, cargo handling and warehousing, and airline hub management for Saudi-based airlines.
- Speeding the low-carbon transition. The Agility Logistics Park in Riyadh features the GCC’s first EDGE Advanced-certified warehouse (Excellence in Design for Greater Efficiencies), meaning it is zero-carbon ready and at least 40% more energy efficient than others in the market. Tristar also is building the Kingdom’s first LEED-certified green building for dangerous goods (DG), in Modon Dammam Second Industrial City.
- Investing in Saudi innovation. Through our venture capital arm, Agility Ventures, we have invested in Saudi Arabia’s entrepreneurs and digital innovators, such as e-commerce enablement innovator Zid and digital road freight platform Humoola. We are also helping bring transformational global health technologies to the Kingdom, through partnerships with companies like AiZTech Labs, which has developed breakthrough medical testing using selfies of the eyes taken with mobile phones and Bexa, a company pioneering innovative breast cancer screening technologies.
- Powering e-commerce. Our Shipa group of companies include Shipa Delivery, one of the Kingdom’s most advanced last-mile delivery providers, and Shipa E-Commerce, a leader in cross-border fulfillment. Shipa provides both domestic parcel delivery and cross-border shipping to and from the GCC and Saudi Arabia.
- Enhancing energy-sector efficiency and safety. Agility affiliate Tristar Group works with Aramco, SABIC, and others in the energy sector to modernize equipment, vehicles and storage facilities used in the handling of chemicals, cryogenic gases and hazardous goods — essential industrial feedstocks.
- Strengthening Saudi companies. United Stars, Tristar’s Saudi JV, earned the highest score among multi-nationals in Aramco’s In Kingdom Total Value Add (iktva) program. The program’s goal is to build a world-class supply chain while cultivating local business and retaining at least 70% of all procurement spend within the Kingdom. United Stars focuses on recruiting, coaching and developing strong Saudi teams.
When it comes to Saudi Arabia’s growth potential, Agility is an investor, partner, and supporter.
Security is a key warehousing factor. You have to protect your assets. Poor security can lead to theft, inaccurate inventory control, and lowered employee morale. Many businesses understand why security is key to good warehousing in Ghana, Mozambique, and Cote d’Ivoire. For that reason, many companies have turned to logistics parks that include security solutions to protect their assets and make a positive impact on the global supply chain.
Why security is important to good warehousing in Ghana, Mozambique, and Cote d’Ivoire
Security is key to good warehousing regardless of geographical location. And in countries and industries that play a large role in the supply chain, it’s even more important.
What role does security play in warehousing in Ghana, Mozambique, and Cote d’Ivoire?
Warehouse security plays a large role in sub-Saharan Africa countries like Ghana, Mozambique, and Cote d’Ivoire. There are several benefits to investing in warehouse security:
- Protecting your facility and employees against potential violence that can occur in rural or urban areas.
- Keeping your employees healthy and safe, even during outbreaks like malaria, HIV, and the COVID-19 pandemic. This includes health screenings and access to lifesaving medicine, including the COVID-19 vaccine.
- Encouraging stakeholders to invest more into your company. Investors want assurance that they’re investing their money wisely, and a secure warehouse helps achieve that.
What are the biggest security problems faced in warehouses in Ghana, Mozambique, and Cote d’Ivoire?
Unfortunately, many African countries face security problems. And this largely stems from lack of infrastructure and resources. Sub-Saharan Africa, home to some of the world’s fastest growing economies in recent years, has been hit hard by the pandemic. The IMF’s 2022 growth projection for the region is 3.8 percent – well below the 5 percent plus rates enjoyed in many years prior to the COVID-19 outbreak. Lack of widespread access to the COVID-19 vaccines will continue to hamper economic activity across the region.
These obstacles detract focus from security. The labor shortage and health risks caused by the COVID-19 pandemic have forced companies to choose between focusing on secure warehousing and running daily operations. The World Bank, among others, is trying to help stabilize the economy. As the economy stabilizes, more companies will have the resources to move into logistics parks with built-in security.
What can happen to warehousing in Ghana, Mozambique, and Cote d’Ivoire without good security?
Warehousing in any country can fail—including countries like Ghana, Mozambique, and Cote d’Ivoire. Subpar security can lead to theft by employees or outside parties, data breaches, and severe supply chain interruptions. Since all of this could lead to losses on your company’s bottom line, you need to make sure that your warehouse security is top notch.
Best security practices for warehouse space in Ghana, Mozambique, and Cote d’Ivoire
The best security practices for warehouse space in souther and West Africa rely on infrastructure and technology. There are also factors that affect security needs in these regions, and it’s important to understand them.
What factors affect security needs in warehouse space in Ghana, Mozambique, and Cote d’Ivoire?
All warehouse space faces security threats like burglary, vandalism and data breaches. However, many African countries are up against challenges that much of the Western world isn’t.
However, there is good news that can increase security and help alleviate safety concerns. And it comes in the form of logistics parks.
What do you need to have the best security in warehouse spaces in Ghana, Mozambique, and Cote d’Ivoire?
Logistics parks offer more than just warehousing. They are full-service work environments for your employees, clients, and operations. And because they offer 24-7 security solutions, they are the safest ways to do business in West and South Africa.
Here are a few ways that a logistics park can increase your safety and security:
- Walled compound to protect your facility, employees, and products
- Closed-circuit TV recording
- Fire-safety features like sprinkler systems
Additionally, logistics parks provide electricity, internet infrastructure, and custom amenities created to fit your company’s needs. In other words, to have the best security in warehouse spaces in Ghana, Mozambique, and Cote d’Ivoire, you need a logistics park.
What role does technology play in security for warehouse space in Ghana, Mozambique, and Cote d’Ivoire?
The best security for warehouse spaces involves technology. Here are a few examples of security measures that you can add to your logistics park to boost security:
- Security cameras and surveillance system
- Alarm system
- Trained guards
- Inventory tracking as an anti-theft measure
- Security software to prevent data breaches
To obtain the technology and resources for these security measures, you need the infrastructure to support the electrical, personnel, and internet needed to run them. And with the increase in profitable businesses like the automobile industry and solar power throughout Africa in recent years, the infrastructure needed to improve warehouse security is growing.
Improvements to warehousing security in Ghana, Mozambique, and Cote d’Ivoire
With the evolution of the African Growth and Opportunity Act in the United States, warehousing security is improving in Africa. This is especially true in countries like Ghana, Mozambique, and Cote d’Ivoire.
Who is developing improvements to warehousing security in Ghana, Mozambique, and Cote d’Ivoire?
Africa displays strong resilience in the face of its challenges. African economies are competing in the world market, attracting the interest of international investors, and beginning to trade with more countries around the world.
Thanks to these promising improvements, much of sub-Saharan Africa is trending toward economic growth. Companies like Agility Africa who see the region’s potential are providing technical assistance and building logistics parks to increase Africa’s presence in the global supply chain.
What factors drive improvements to warehousing security in Ghana, Mozambique, and Cote d’Ivoire?
The world economy is changing, and Africa wants to be part of it. The desire to increase their presence in the global supply chain is a significant factor that drives improvements to warehouse security.
Logistics parks are also increasing secure warehousing in West and southern Africa. The best parks offer on-site security management and routine perimeter sweeps to ensure the safety and security of the entire company. And as the African infrastructure improves, so will the capacity to make facilities even more secure.
How will improving warehousing security in Ghana, Mozambique, and Cote d’Ivoire impact the African economy?
Improving warehousing security in these nations should have a positive effect in the overall economy. As security improves, more companies will open facilities in the area. Each facility creates jobs, productivity, and innovation. And because more people will be working, the money they’ll put back into the economy will stimulate economic growth.
Best bonded warehousing in Ghana, Mozambique, and Cote d’Ivoire
Bonded warehousing can be difficult to come by. You need security to protect the goods, a strong warehouse receipt system to prove where the goods came from and are sold to, and the land and labor to support the warehouse’s operations. Fortunately, there are bonded warehousing opportunities throughout sub-Saharan Africa.
What is bonded warehousing?
A bonded warehouse stores imported or exported goods without having to pay customs duty or value added tax until the goods are sold to customers.
In other words, bonded warehousing provides a secure facility and logistics control for international goods. And since the logistics company doesn’t have to pay duties up front, it’s a lucrative way to warehouse.
What factors do the best bonded warehouses in Ghana, Mozambique, and Cote d’Ivoire share?
One of the factors is ethics compliance. To successfully compete in the global supply chain, warehouses and logistics parks must set high standards to attract new investors and avoid government scrutiny. When a company is on the up and up, it’s less of a risk for investors to finance their operations.
Additionally, high-end logistics parks have become a key factor in the best bonded warehouses. Logistics parks offer the storage, distribution, and operation capabilities that a bonded warehouse needs to efficiently transport their goods to their customers.
Technology is also a factor. In fact, 64 percent of supply chain executives believe that digitization and robotics are large elements to overcoming the economic recession caused by the COVID-19 pandemic.
Where can you find the best bonded warehousing in Ghana, Mozambique, and Cote d’Ivoire?
Bonded warehousing has become more available in West and southernm Africa in recent years. Land and labor are available in countries like Ghana, Mozambique, and Cote d’Ivoire, and companies are building logistics parks and increasing production in these developing regions.
Logistics parks are the best way to secure your warehousing in Ghana, Mozambique, and Cote d’Ivoire
You need an expert partner when you open warehouse space in southern and West Africa. Agility is that expert! Agility Logistics Parks provide infrastructure, round-the-clock services, and all the facility necessities and amenities to set you up for success.
Visit our website to find out how are flexible solutions fit your needs.
The physical and geographic features of a commercial real estate property determine its value. Rather than listing a long series of features, agents and brokers can summarize this value with a classification system ranging from A to C. At the high end are international-standard Class A warehouses.
More than simply storage buildings, international-standard Class A warehouses are the linchpin in modern, efficient supply chain logistics strategies. Read on to learn more about the characteristics and benefits of state-of-the-art Class A warehouses, the difference between a Class A warehouse and a Class A facility, and how to choose a Class A warehouse.
Characteristics of an international-standard, Class A warehouse
In short, international-standard Class A warehouses are state-of-the-art properties built specifically for warehousing and logistics. They have not been converted or renovated for this purpose. They are designed and built from the ground up to benefit the supply chain.
Before delving further into Class A characteristics, a brief look at other levels might prove helpful. A step down from Class A is Class B. Such a building may be a little older but renovated to have the latest and greatest technology. It will also have lower ceilings than a Class A building and may have multiple floors, which is not ideal for warehousing.
Class D and Class C buildings fall at the low end. They are typically older buildings converted from their original purposes, such as former hangars and manufacturing facilities. They often lack modern amenities, such as climate control and accessibility.
Building specifications and materials
Noncombustible or fireproof raw materials, flexibility, and mobility are essential aspects of Class A warehouse construction. Steel and sealed concrete are the most common structural elements with the possible addition of masonry, plaster, gypsum, or other noncombustible materials. Note that sealing concrete is essential to reduce dust that can cause wear and tear on equipment.
Glass, ceramic or stone tile, and stucco can enhance the aesthetic value of interior and exterior walls. Few people want to work in a bare steel and concrete box.
The warehouse might store a variety of inventory with different storage needs. To accommodate these needs, a Class A warehouse will have ceilings at least thirteen meters high, support columns at least twelve meters apart, and spans of at least twenty-four meters.
And that’s just inside the building—what’s outside is just as important. It must have at least one automatic docking gate for every five hundred square meters of interior space and sufficient outdoor space to maneuver large trucks and for employee parking.
Warehousing innovation
Technology and innovation are increasingly important in warehousing logistics. Four walls, support structure, and a roof are no longer sufficient. At a minimum, a Class A warehouse includes climate control, fire safety features, security monitoring and alarms, high-speed internet, and an electrical substation.
Beyond those requirements, automation is the future. An automated warehouse will include tech-based solutions such as drones that easily reach the highest shelves, robots (or “cobots” that work alongside humans), composite panels that improve the building’s energy efficiency, and more. Smart warehouses make smarter, more agile supply chains.
Location, location, location
The old adage that location is everything in real estate is particularly true with warehouses. Class A warehouses are located at the confluence of airports, railways, ports, and highways for quick access to major domestic and export markets.
Other building classes might not be as ideally located if their region has grown and changed since their construction. For example, industrial facilities built before 2000 are often converted and renovated, but they might be gridlocked within cities that have grown up around them.
Benefits of an international-standard, Class A warehouse
Because Class A warehouses are built specifically to suit a modern supply chain, the benefits are innumerable, ranging from optimized retail logistics to sustainability to safety. A few highlights include reduced carbon footprint and increased efficiency and accuracy.
Reduced carbon footprint
Inefficient heating and cooling systems—such as those you might find in a Class C building—mean high carbon emissions. Just by virtue of being new construction, Class A warehouses have the proper insulation and roofing materials to maximize indoor climate control.
Green warehouse design is also a common feature in Class A warehouses. Such sustainable design might include solar panels for alternative energy, skylights for daytime lighting, LED bulbs to reduce electricity consumption, xeriscaping to reduce water usage, and regionally sourced building materials to reduce transportation-related emissions. Individually and collectively, these features reduce the building’s carbon footprint.
Finally, a prime location reduces transit times and fuel use, giving you both increased efficiency and a reduced carbon footprint.
Increased efficiency and accuracy
Many of the features built into Class A warehouses increase efficiency right from the start. Smart warehouse management can then further reduce warehousing challenges and inefficiencies.
Optimal warehouse layout and layout flexibility, in particular, are huge time savers. High ceilings and wide spaces between columns and spans provide this flexibility. Stacking shelves higher puts related products in closer proximity. Wider aisles give people and equipment more room to maneuver quickly and safely.
Creating and adapting your rack design to your particular workflow ensures optimal movement throughout the space. A flexible layout also allows you to reorganize as inventory changes with supply and demand.
Zoning, both inside and outside the warehouse, is another important aspect of efficiency enabled by Class A space. With more automatic docking gates, some gates can be dedicated to receiving and others to dispatching to reduce traffic jams. Positioning popular products in proximity to dispatch areas gets them to market faster.
And as we all know, haste equals waste. Employees have more time to do their jobs thoroughly and effectively when efficiency is increased. Paired with warehouse automation, errors and waste are minimal.
Class A warehouse versus Class A facility
Unfortunately, building classification isn’t always consistent from market to market, and confusing language sometimes arises. Commercial real estate agents use the Class A designation on a variety of facilities, such as office space, light industrial space, distribution centers, and even warehouse space that doesn’t quite meet the criteria of a Class A warehouse.
In the case of warehouses in particular, distinguishing between these types of buildings is important. A large space dubbed a Class A “facility” instead of “warehouse” might have lower ceilings (at least ten meters instead of thirteen), which reduces options for shelving, and fewer automatic docking gates (one for every seven hundred meters of interior space instead of five hundred).
While these differences may seem small, each amenity can impact effective warehouse management and inventory management. In either case, however, “Class A” designates best-in-class property, and warehousing innovation can happen in a variety of settings.
How to choose a Class A warehouse
The first step in choosing a Class A warehouse is asking yourself and your team the right questions and sharing that information with your internal or external commercial real estate team. Here are just a few of the questions to consider:
- What functions will you perform on this property? Will it simply serve as well-staged storage for your company’s internal use? Will it be a distribution center with order picking, packing, and processing? Will you need co-located manufacturing facilities? Will you need a designated area for office space?
- How much space do you need now and in the next five to ten years? (Remember to plan for your success.)
- What type of inventory will you store and process, and will these goods have specialized storage needs, such as refrigeration or reinforced rack design?
- Do you already have a warehouse inventory management system, or do you need help creating one?
- How will you maximize warehouse efficiency? If you aren’t sure, consider consulting one of Agility’s experts.
- What warehouse technology and automation would be nice to have, and what do you absolutely require to meet your goals?
- What warehouse layout will you need to maximize traffic flow and safely maneuver people and equipment?
- Do you need rack design consultation?
- What location optimally positions your goods for your supply chain needs?
- What security features do you require to protect your assets (people and products)?
- Do you need a bonded warehouse or bonded space within a warehouse to manage dutiable goods?
- What’s your budget? Be sure to factor in how the features and benefits will offset your warehouse space’s costs.
Your answers will help determine the class of warehouse you truly need and prioritize the features and benefits of each promising property identified in your search.
Warehousing solutions simplified
Agility Logistics Parks designs, engineers, and operates the most advanced international-standard warehousing complexes and light industrial facilities in emerging markets. Our flexible solutions are ready. Contact our team to begin your search for an international-standard, Class A warehouse in the Middle East, Africa, or South Asia.
Warehousing in Saudi Arabia could play a crucial role in the global warehousing market. The country is at a crossroads between Asia, Europe, and Africa. And by improving its warehousing, it can establish its place as a powerhouse in global trade.
The Saudi warehousing market is growing, and emerging technology and services provide the country with more options to expand. To capitalize on this potential, Saudi Arabia must take stock of its current warehousing market and look for ways that logistics partners like Agility can help it grow.
Status of the warehousing market in Saudi Arabia
In 2016, Saudi Arabia announced its plan to reduce the country’s dependence on the oil market and diversify its economy with a strategy called Vision 2030. To develop the country into a global trading hub, Saudi Arabia is improving its logistics market, including warehousing, and has made strong steps forward in logistics management.
Current warehousing market
According to Ken Research, the Saudi dry warehousing market grew by 2.8 percent between 2015 and 2019 and will continue to grow until at least 2025. The industrial and retail industries are responsible for the largest percentage of this expansion.
The warehousing market is largest in the cities of Jeddah, Riyadh, and Dammam. While Jeddah has a majority of the warehouse revenue share, all three cities play a key role in the expansion of warehousing in Saudi Arabia.
- Jeddah: Jeddah is a port city on the Red Sea. Its warehousing district is close to the Jeddah Islamic Port. Here, the warehouse and logistics supply districts stretch 26.1 million square meters.
- Riyadh: Located in the center of the country, Riyadh is the capital of Saudi Arabia and its main financial hub. Its warehousing districts are primarily near Riyadh’s dry port. The city dedicates 24.5 million square meters to warehousing and logistics parks.
- Dammam: The Dammam metropolitan area is on the Persian Gulf. Its warehousing and logistics parks cluster among four zones to the north, east, south, and west of the city. Currently, the city uses 20.9 million square meters for its warehouses and logistics parks.
Dry freight forwarding
Dry logistics refers to the transport of freight that cannot get wet. The dry logistics market in Saudi Arabia centers primarily in Riyadh and Jeddah. These cities mainly use road transport for dry logistics, with air, sea, and rail following as alternate freight modes.
Dry freight forwarding is a newly stable industry in Saudi Arabia. Between 2015 and 2019, an oil price slump and subsequent economic downturn caused the dry logistics industry’s compound annual growth rate to decline.
However, market analysts from Ken Research forecast that the dry logistics and freight forwarding markets will grow by 1.3 and 0.8 percent, respectively, until the forecast period ends in 2025. This growth is due in part to Vision 2030’s efforts to improve the country’s logistics management.
Warehousing advancements in Saudi Arabia
As the warehousing market in Saudi Arabia expands, companies are developing innovative solutions to streamline their supply chains and increase functionality. Because of this, Saudi Arabia’s warehousing sector is set to keep pace with the rising demand for goods moving in and out of the country.
Key warehousing advancements
To meet the goals outlined in Vision 2030, the Saudi Arabia warehousing market expanded and introduced a number of inventive solutions to push the industry forward.
- Cold storage: In the wake of the COVID-19 pandemic, the need for a safe and effective way to transport and store vaccines was apparent. To meet global demand for a vaccine, Saudi Arabia built a series of warehouses dedicated to storing pharmaceuticals and other perishables. These refrigerated warehouses enable the country to maintain a cold supply chain.
- National Industrial Development and Logistics Program (NIDLP): Saudi Arabia launched NIDLP to improve infrastructure and design new policies related to economic growth. By dedicating financial support to logistics development, NIDLP aims to build Saudi Arabia’s role as a regional logistics hub and improve warehousing.
- Al Khomrah Logistics Zone: The Saudi Arabian ministry of transport opened a logistics zone in Jeddah to support shipping, freight distribution, and transport. This is the largest logistics zone in the country.
- On-demand warehousing: On-demand warehousing enables companies in Saudi Arabia to access warehouse solutions on a temporary basis. On-demand warehousing services negotiate with warehouses to build a network of facilities to increase supply chain efficiency. Companies can lease on-demand warehouse space as a way to cost effectively address shifting demand.
Important technology for warehousing advancements
One of the most crucial elements driving Saudi Arabia’s warehouse market is the country’s embrace of technological advances. These developments help streamline the supply chain and improve warehouse management.
- Saudi blockchain technology: Saudi Arabia aims to implement smart systems to facilitate efficient trade and storage—particularly at seaports, which account for the majority of its trade. To that end, Saudi Customs successfully launched a blockchain pilot to help strengthen the country’s shipping logistics infrastructure. The technology will offer a digital reference of all stages of trade in order to increase transparency across the shipping supply chain.
- Application programming interfaces (APIs): APIs help different order fulfillment, inventory management, and warehouse management software to communicate with each other. This streamlines the warehousing process and enables warehouses to connect with other elements of the supply chain.
- Internet of Things (IoT): The IoT is a boon for warehouse managers, enabling improved inventory management systems and real-time tracking. IoT devices embedded into shipments help companies see where their transported assets are in real time, anywhere in the supply chain. This leads to a faster, more efficient, and more visible flow of goods. By quickly exchanging data with the IoT, warehouses can make all processes more economical.
Challenges with Saudi Arabian warehousing logistics
To emerge as a major player in global logistics, Saudi Arabia must face several obstacles to warehousing expansion. By understanding these challenges, the country is better suited to overcome them.
Major challenges for logistics managers
- e-Commerce: The use of e-commerce has expanded globally and among Saudi Arabian citizens. The market is fast growing, which exposes weaknesses in Saudi Arabian supply chains. Urban centers in Saudi Arabia are not as compact and densely populated as urban environments elsewhere. That lack of density limits efficiency in distribution from the warehouse to the customer. Because of this, suppliers are sometimes unable to meet the demands of e-commerce shoppers for fast shipping.
- Supply chain interruption: COVID-19 revealed vulnerabilities in supply chains. Because their success is dependent upon a variety of uncontrollable variables, warehousing facilities have little power over supply chain interruptions. This means facilities are vulnerable to delays that can result in canceled orders and a lack of customer trust.
- Aging warehouses: Modern, automated warehouses come at a cost. Because of this, many warehousing districts, particularly in Riyadh, contain a large number of aging and outdated structures These are less suited to meet demand and can slow the throughput of goods. Saudi Arabia will need to upgrade these aging warehouses in order to keep up with the global warehousing market.
Solutions for common challenges with warehousing in Saudi Arabia
As challenges arise in warehouse management, companies must develop solutions to meet them. As Saudi Arabia seeks to overcome these challenges, there are many solutions that can help its warehousing networks thrive.
Close proximity to suppliers
Minimizing the distance that materials and goods need to travel can help reduce logistics inefficiencies. Large distances between a company’s suppliers, warehouse facilities, and consumer centers increase lead times, transportation costs, and the risk of supply chain disruption.
Strategic positioning of warehouses can prevent these complications. By positioning warehouses close to suppliers and consumer centers on road, air, and sea transport routes, companies can improve supply chain efficiency. Making these decisions upfront helps companies to cut inefficiencies out of their supply chain before they become a problem.
Warehouse automation
With a growing global demand for goods, it is essential that warehouses effectively manage their inventory, personnel, and equipment. Without reliable warehouse inventory monitoring, companies risk using unreliable data to manage inventory levels.
Additionally, inaccurate personnel or equipment tracking may lead to inefficient warehouse processes. As a consequence, these companies risk failing to deliver goods on time and costly setbacks. Automation in warehouse inventory management systems can alleviate these issues.
The most common way warehouses can implement automation is through warehouse management systems (WMSs) and warehouse control systems (WCSs). While there is some functional overlap between the two, WMSs primarily work to manage personnel and inventory while WCSs focus on equipment.
These systems provide more reliable data on stock levels and workflow to ensure swift order fulfillment. By embracing these systems, Saudi warehouses can more efficiently manage their inventory and product flow.
Logistics parks
One of the most challenging parts of any warehousing operation lies in infrastructure development. Existing logistics parks ease the burden by supplying a fully developed warehouse and logistics infrastructure to companies that need it—logistics parks provide complete logistics services in the storage and distribution of products.
Agility holds over one million square meters of space in Riyadh, Jeddah, and Dammam. Agility’s warehouses in Saudi Arabia are strategically located for easy access to seaports and airports, making them accessible to international customers. These modernized facilities can help companies optimize their logistics.
How Agility can help
Understanding warehousing in Saudi Arabia can help warehouse management companies make a plan for seizing the potential this region has to offer. To meet your warehousing requirements, contact Agility Saudi Arabia, a leading logistics provider in the region.
With Agility Saudi Arabia, regional and global clients can connect with suppliers and markets around the world.
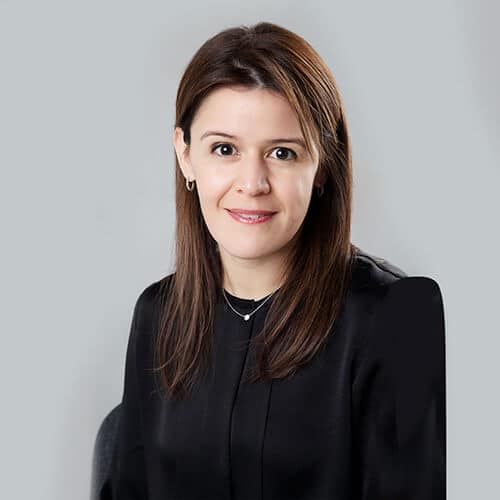
Head, Agility Ventures
I recently attended a Business Year conference on the role of the private sector in the future of the Kuwaiti economy. The event highlighted Kuwait’s potential to support a vibrant start-up community, but the need was clear for entrepreneurs to capitalize on the country’s digital transformation to drive innovation.
I spoke on a panel alongside entrepreneurs from other well-known Kuwaiti brands including Carriage and Just Clean. There were also insightful contributions from several others, including Kuwait’s Minister of Finance and the Director General of the Kuwait Direct Investment Promotion Authority (KDIPA).
We discussed the fact that while funding for SMEs is critical, a complete eco-system including incubators, talent, laws and other elements must be a part of the wider picture.
I’m encouraged because many of the essential components of a strong knowledge-economy eco-system are coming into place in Kuwait: public and private funding sources, incubators, accelerators and vital sources of mentorship, advice, connections and go-to-market expertise. Kuwait’s legal and regulatory framework is evolving in a positive way.
At Agility, we believe that established companies like ours have a key role to play in supporting SMEs, especially those in the Middle East. We do this both by building products that facilitate SME growth, and by directly providing funding, mentoring and other resources to startups in Kuwait and the broader region.
In March, we brought experts from the MIT Media Lab to Kuwait for the Agility Data Hackathon, a four-day event in which technology students, coders and entrepreneurs competed to solve real world societal and business problems with data and analytics. The idea: to bring together a new generation of Kuwait problem-solvers and encourage development of the collaborative, creative mentality critical to the future of Kuwait and its citizens.
Agility Ventures, our in-house venture capital arm, invests in and advises startups on supply chain ideas and technology. Startups we’ve supported so far include Homoola, a Saudi Arabia company using data analytics and technology to bring new efficiencies to road freight, and CargoX, a Brazilian road freight platform.
We’re also acting as role models, driving our own digital transformation through in-house innovation and investment and the introduction of new products and services. As part of our SME product strategy, we’re investing more than $100 million in Shipa, a new family of tech-enabled freight, e-commerce and delivery services that help small businesses reach international markets. New technologies can streamline the shipping process and make it easier for small businesses to reach overseas markets.
Can Kuwait transform itself into an innovation hub and a private sector-led knowledge economy? The Business Year conference showed that we have the right ingredients for a thriving startup community: funding initiatives, banking structures, connectivity, and well-placed consumers. Now we need to connect the ingredients so they form a healthy, integrated eco-system rather than existing in isolation or as part of fragmented networks. With key stakeholders leading the call for change and entrepreneurs driving innovation, a connected ecosystem will deliver lasting results.