In January 2021, Africa officially became a single free trade zone. Headquartered in the Ghanaian capital of Accra, the African Continental Free Trade Area (AfCFTA) created the largest free trade area in the world, measured by number of countries. Africa’s 1.3 billion people and combined gross domestic product of more than US$3 trillion now connect in a single market for goods and services.
In addition to AfCFTA, the explosion of e-commerce as well as infrastructure development are driving demand for high-quality warehousing throughout the continent. Agility, for example, is developing more than one million square meters of warehousing in burgeoning industrial areas. This includes new facilities in the sub-Saharan capitals of Accra, Maputo, and Abidjan. So how do you know if you are getting value for your money in Ghana, Mozambique, and Cote d’Ivoire warehousing?
Rapidly, African countries are making strides in logistics management. Warehousing used to rely on makeshift “godowns” for the storage of goods. Godowns typically lack certain basic features, such as reliable power, internet connectivity, security and sophisticated fire prevention and safety. Now, the need for modern warehouses is on the rise. With increased attention on attracting foreign investment in many African countries, here’s how to know if you are getting value for your money in Ghana, Mozambique, and Cote d’Ivoire warehousing.
What to look for in warehousing in Ghana, Mozambique, and Cote d’Ivoire
Common types of warehousing options in Ghana, Mozambique, and Cote d’Ivoire include:
- Public warehouses: Owned and regulated by government bodies that charge rent.
- Bonded warehouses: Owned by government or private companies with a government license.
- Private warehouses: Owned and managed by manufacturers or by specialized developers and logistics parks operators .
Logistics parks
A logistics park is an area specifically designed to consolidate and centralize storage, distribution, processing, assembly, light manufacturing and other activities, that require warehousing. Modern logistics parks integrate easily with transportation networks so that goods move easily to and from intended markets.
Ready-built warehousing
Logistics parks feature pre-existing warehouse space, known as “ready-built warehousing,” which offers more predictable expenses. The landlord has already absorbed the cost of land, permits, and other regulatory requirements.
For example, CDCI, the largest retailer in Cote d’Ivoire, relocated to a ready-built warehouse in the Agility Logistics Park near Abidjan. The move upgraded CDCI’s operations to international standards and helped streamline and modernize its storage facilities. Since the move, CDCI has reduced overall logistics costs and lowered the rate of theft.
Flexible leasing
Another advantage to ready-built warehousing is support for flexible leases and space allowing businesses to scale. A flexible lease allows you to use or let warehouse space according to need. Agility Africa, for example, offers flexible leases from six months to five years with sizes from 500 square meters to more than 10,000 square meters.
Infrastructure reliability
International standards include 24-7 security, plus consistent electrical power, all included in the lease. Security includes controlled access as well as constant monitoring of the facility. Plus, the warehouse features sprinkler systems and other fire-prevention measures.
Increasingly, world-class warehousing involves internet connectivity and dependable backup service. Reliable internet service provides access to inventory, data analytics and insights that your company can use to build a resilient supply chain.
Prime location
The UN Centre for Trade and Development estimates that there are currently more than 180 special economic zones (SEZs) in Africa, with 51 more under development. SEZs are areas that provide tax incentives in exchange for a company’s investment. Many African governments are facilitating development of logistics parks within SEZs to attract foreign investors.
Ghana, for example, established the Ghana Free Zones Authority (GFZA) in 1995. The GFZA lets companies operate in certain zones without paying customs duties. The Agility Logistics Park in the Tema Free Trade Zone offers not only bonded warehousing in Ghana but also laydown yard. A laydown yard is an outdoor space within a warehouse area to store material and equipment, often convenient for mining companies as well as oil and gas businesses.
For instance, many international energy companies have set up shop in the Agility Logistics Park near Accra. Its warehousing meets international standards, important for oil and gas, mining, automotive, fast-moving consumer goods, and electronics companies.
Why invest in warehousing in Ghana, Mozambique, and Cote d’Ivoire
The World Bank’s Logistics Performance Index is a survey of operators who provide feedback on a country’s logistics “friendliness.” Its most recent scores revealed that countries in sub-Saharan Africa averaged a score of 2.20 out of 5 for logistics infrastructure. However, African countries are emphasizing infrastructure upgrades. In fact, the British property consultancy Knight Frank estimates US$400 billion worth of rail and road development is taking place across Africa.
Africa’s industrial corridors
African governments with the support of the World Bank are creating seven industrial corridors that connect African regions by rail, by road, and by sea. For example, the West Africa Growth Ring links Ghana, Togo, Burkina Faso, and Cote d’Ivoire. The West Africa Growth Ring has seven main ports, including Takoradi and Tema in Ghana as well as San Pedro and Abidjan in Cote d’Ivoire.
Elsewhere, the Nacala Corridor connects Mozambique, Malawi, Zambia, and Zimbabwe. It features the Nacala Railway, valued at US$4.4 billion. Also, its main port of Nacala, in Mozambique, is the deepest port in southern Africa.
The objective of Africa’s industrial corridors is to promote investment and development, laying the groundwork for more than a million square meters of purpose-built warehousing, Knight Frank predicts. Companies such as Agility have built logistics parks along these prime industrial corridors, offering ready access to major ports and roadways.
Growth of e-commerce
Even before the COVID-19 pandemic, the Economist Intelligence Unit had predicted e-commerce in Africa to drive a 3.2 percent increase in retail sales. The pandemic drove even greater economic growth in online goods, which in turn created a promising outlook for warehousing, according to a study by the Mace Group.
Specifically, online sales revenues across Africa increased by more than 28 percent from 2019 to 2020, according to Knight Frank. Furthermore, e-commerce revenue could nearly double to $46 million by 2025 from the 2020 value of $27 billion, creating further private sector demand for warehousing.
Return on investment
Africa’s increasing attraction to foreign investors is driving demand for logistics facilities such as warehouses. As a result, industrial assets such as warehouses offer an average 12 percent yield. That’s double the yield of residential and more than the 9 percent yield of retail or office space, according to Knight Frank.
How to identify potential hidden costs in warehousing
Despite the emphasis on attracting foreign investment, each African country differs in its regulations. That’s why relying on local know-how helps your company figure out how to know if you are getting value for your money in Ghana, Mozambique, and Cote d’Ivoire warehousing.
Careful land management
For instance, leasing warehouse space in an Agility Logistics Park avoids the potential pitfalls of identifying and purchasing the land yourself. The navigation of each individual local market throughout sub-Saharan Africa requires informed decision-making and in-depth knowledge of local regulations. Otherwise, taxes or other fees particular to the chosen location can cause unpredicted cost overruns.
Stability in pricing
Furthermore, land prices are rising due to declining availability of suitable, properly zoned and approved land combined with increasing demand for industrial space. A further advantage of leasing space in a logistics park involves stability in operating expenses, such as electricity or waste management.
Emphasis on operational efficiency
Warehouses that meet international standards also decrease capital costs and boost quality control. Proximity to roads, railways, and ports also helps speed distribution.
How to incorporate best practices for investing in warehousing in Ghana, Mozambique, and Cote d’Ivoire
Best practices in warehousing go beyond physical infrastructure as well as considerations regarding power supply, internet access, and security.
Training local workers
Logistics in Africa have increased employment opportunities in Ghana, Mozambique, and Cote d’Ivoire. In Tema, for example, Agility hires 100 percent of its employees locally. The company offers vocational and technical training to local students to create its own skilled labor force.
Paying attention to the environment
In keeping with the global movement toward sustainability, Agility warehouses meet international environmental standards. For example, Agility uses energy-efficient roof materials. Skylights provide natural lighting and accompany LED and energy-saving bulbs. Solar-powered streetlights and wind-driven roof fans also contribute to energy savings.
Using data-driven solutions
Reliable internet means companies can use technology to improve best practices in warehousing. Artificial intelligence (AI) can save companies time and reduce operating costs. For example, AI can free employees from routine tasks, such as modifying fulfillment orders that come through the warehouse.
How to find the future in warehousing
The prime warehousing and logistics market has seen increased activity in certain pockets of sub-Saharan Africa, notably Abidjan and Maputo, Knight Frank reports. There’s rapidly improving infrastructure and favorable government regulations. It’s important to determine if you are getting value for your money in Ghana, Mozambique, and Cote d’Ivoire warehousing. Contact Agility today for expert guidance on how to capitalize on these emerging markets.
Logistics parks with strategic locations in Mozambique offer a unique benefit to gas and oil companies. Warehouses near road networks, airports, and rail lines provide the quick access needed for safe, secure storage of equipment, vehicles, and construction materials necessary for production of natural gas and oil.
The economy of Mozambique, one of Africa’s poorest countries, is forecast to grow by 4% in 2022. One reason is the country’s drive to exploit its sizeable deposits of oil and natural gas. Mozambique is currently the third-largest holder of natural gas reserves in Africa, with 100 trillion cubic feet of reserves. The country’s reserves position it to be an international exporter and one of the world’s leading producers of both oil and gas in the coming years.
The Rovuma Basin off the coast of the Cabo Delgado Province in Mozambique is considered the new home of oil and gas. Three large liquefied natural gas (LNG) projects underway in this area have greatly increased the demand for logistics parks:
- The Rovuma LNG project is a $30 billion LNG project and the largest of the three. The project has been on hold due to an insurgent attack in the area, but investors are confident the project will move forward soon.
- The Rovuma Basin also hosts the Mozambique LNG project ($20 billion) and the Coral Floating LNG project (worth $4.7 billion).
The following will demonstrate specific benefits of logistics parks for both oil and gas companies and what to look for when choosing a logistics park warehouse.
Benefits of logistics parks for oil companies in Mozambique
Oil companies face many challenges in today’s world, including the growing concern about fossil fuels and their role in climate change. Long-term energy transitions aim to improve energy efficiency and use of renewable energy to lower the environmental impact of fossil fuels.
Agility warehousing offers a unique opportunity for multinational energy companies operating in the booming market in Mozambique. For them, logistics parks are invaluable. Oil companies in particular face challenges when it comes to the storage of heavy equipment, pipes, and other materials needed to produce oil. Logistics parks help alleviate those complications and ensure oil companies keep costs down.
How oil companies can use logistics parks
Typical uses of logistics parks include storage, processing, distribution, and light manufacturing. They offer oil companies covered and outdoor storage for high-value equipment and parts, chemicals and lubricants, vehicles and other goods, in addition to providing space for fabrication and maintenance.
How does this relate specifically to oil companies? Large-scale energy projects like those in the Rovuma Basin require construction and engineering that must be synchronized and carefully sequenced. Logistics parks provide secure covered and uncovered space to stage materials, equipment and crew work required. Another important aspect of a logistics park is that they provide a central location, which enables those processes to be more efficient.
Unique benefits of logistics parks
Logistics parks offer many unique benefits, including reducing costs and saving companies’ time. The strategic location of logistics parks helps to streamline the transportation and warehouse needs of oil companies, thus increasing supply chain efficiency.
The Agility Logistics Park in Maputo, Mozambique, for example, is located on Maputo’s Ring Road with ready access to the Maputo Port and the main roadways to South Africa. The proximity of this logistics park to the port provides easy access to stored vehicles and pipes needed for major oil projects. Having these items stored close to drilling sites enables oil to be moved from offshore Mozambique to northern Mozambique and beyond in a more efficient and cost-effective way.
Reducing company costs and increasing productivity
Oil companies face unique and complex challenges with the supply chain. Special equipment needs and the vast number of pipes needed in oil production requires the assistance of logistics and logistics parks to guard against service interruptions and protect investment. Problems with drilling equipment in need of repair or replacement can be easily remedied if there is additional equipment stored nearby.
Logistics parks like the Agility Logistics Park warehouse in Maputo are ideally located and connected to road, air, rail, and sea networks. A strategic, central location reduces unnecessary transportation. A secure storage site for everything needed to produce oil also keeps costs down by keeping expensive machinery and equipment safe, and providing maintenance, repair and engineering space. In Mozambique, this is critical.
Benefits of logistics parks for gas companies in Mozambique
Mozambique generates more electricity than it consumes, and South Africa receives a large part of the excess energy because the surplus is exported from Mozambique. Apart from proven oil reserves, there is additional untapped potential in the energy sector, with an estimated hydropower potential of 12,000 MW and large natural gas reserves as well.
Proven and estimated Mozambican energy reserves present huge opportunities for gas companies. To efficiently reap the benefits, a central storage location is needed to assist with the intense resource and manpower needed to produce natural gas.
Logistics park features for gas companies
Offshore natural gas production requires a lot of specialized, heavy equipment. Cranes and hoisting systems, large engines, and pumps are commonly required. Logistics parks offer the amount of space necessary to store and maintain this kind of equipment, as well as the construction material for production platforms.
Pipes are essential in virtually any oil and gas project because they are used in underground wells, embedded in the sea floor and used to construct pipelines. Seventy-five percent of South Africa’s natural gas is transported via pipelines. Logistics parks are crucial to natural gas production because they provide laydown yard space for all the pipes needed for transport.
Why should gas companies use logistics parks for storage and distribution?
One of the challenges that gas companies face is ensuring that the requirements of demand and supply are met in an effective way. This is especially difficult in parts of Africa that lack the storage infrastructure needed to meet the demand.
Logistics parks and Agility warehouses provide the solution with safe, secure storage for gas production equipment and ideal locations for easy access. Gas companies can use logistics parks for storage of all the large equipment, tools, chemicals and other material necessary to extract and transport gas.
Improving gas company efficiency
South Africa has historically relied on coal as the main energy source for the country (comprising about 80 percent of the energy mix) but is moving towards natural gas, which emits less CO2. One of the biggest challenges that gas companies face in using natural gas and liquid fuels efficiently lies in the complicated supply chain.
Logistics parks increase the efficiency of the supply chain by cutting out unnecessary transportation time. With gas extraction equipment and pipes all in a central location, there are fewer steps in the chain.
How logistics parks in Mozambique help foster growth in international markets
Logistics parks help foster economic growth in international markets in several ways. First, logistics parks provide more efficient access to roads and ports. This helps encourage growth as it reduces transportation and shipping costs. Lower costs and easier transportation access both increase the opportunity to expand globally.
Logistics parks greatly help to streamline the supply chain process. Costs for gas and oil companies are reduced by using move-in ready warehouses as these businesses don’t have to plan and build their own storage facility. By helping to save costs and increase efficiency, logistics parks can help organizations grow and compete with multinationals.
Benefits of central distribution hubs
Mozambique offers tremendous opportunities in the oil and gas industries but lacks the infrastructure that is needed to process and distribute products. Logistics parks help boost the infrastructure by serving as central distribution hubs. These hubs have the following benefits:
- Lowered storage costs
- Increased efficiency of warehouse organization
- Lowered transportation costs
- Increased readiness to distribute products
Poor infrastructure results in disconnected supply chains, and logistics parks mitigate that risk. Companies wishing to enter a new market in an area with poor infrastructure can utilize the benefits of Agility ready-built warehousing. In short, centralized distribution hubs increase accessibility for oil and gas companies.
Reducing the carbon footprint
Lowering the carbon footprint of multiple industries is a global responsibility. Carbon footprint reporting is particularly important in African countries as they have a high vulnerability to climate change. Finding a balance between economic growth from energy operations and conservation of natural resources is no easy task.
The world has long been dependent on coal, and that has greatly contributed to high levels of greenhouse gasses. Moving from coal to natural gas serves to protect and increase energy investments while also meeting environmental goals and regulations. Logistics parks provide support for the transition to natural gas by providing centralized storage sites to make natural gas supply chains more efficient.
Fostering economic growth
An investment in Mozambique logistics parks will help foster economic growth in the region by supporting the manufacturing and extractives industries. Investing in logistics parks will help to support job growth and economic expansion in Mozambique.
Finding the right logistics parks in Mozambique
What oil companies should look for in logistics parks
There are several features that crude oil companies should look for in logistics parks when considering an investment in Mozambique. Of utmost importance is the location because having a strategic location is one of the best advantages of logistics parks. The lower transportation costs and streamlined distribution opportunities hinge on the location. Agility’s logistics parks, for example, are all located near capital cities and major roads and rail networks, seaports, and airports.
Cities like Maputo check all the boxes for location. The gas and oil exploration sectors in the Cabo Delgado Province have driven demand for an increase in air transport. This means that the area will most likely see an expansion in air transportation options. Mozambique already has four large commercial ports, including Maputo. Mozambique also has a rail network from the Port of Maputo to South Africa.
There is an inherent risk in investing in emerging markets with capital costs and efficiently meeting the market demand. Agility’s logistics parks help mitigate those risks with unique advantages. Agility offers services and expertise such as increased warehouse security, climate-controlled storage, and over forty years of facilities maintenance experience.
What gas companies should look for in logistics parks
Like oil companies, gas companies should look for certain traits in a logistics park. Location, experience, and type of warehousing offered are important. In addition, gas companies may want to consider sustainably-built warehousing.
As the world grapples with climate change and many countries attempt to make a move away from fossil fuels to renewable energy sources, natural gas extraction has presented itself as a transitional solution. Finding a logistics park that uses eco-friendly materials and waste management services will further support the environmental goals of responsible gas companies.
Agility offers a green warehouse design with recycling zones, low-emitting paint, and regionally sourced building materials. Agility warehouses also lower energy costs and environmental impact through solar panels, skylights, and LED lighting.
Regulatory requirements
Compliance with regulatory requirements is of paramount importance with gas and oil companies. As regulations for the extraction and production of gas and oil change, companies may need additional storage space for special equipment needed to meet requirements.
Depending on the area, there may also be many regulations surrounding the safe storage of hazardous materials used in energy production. Chemicals, drilling mud, and hazardous goods need a secure storage site, and Agility Logistics Parks can meet that requirement.
Contact Agility to learn more about the experienced, international-standard Agility Logistics Park in Mozambique. See how Agility warehousing provides high-quality, sustainably designed logistics parks with strategic access to transportation networks.
As a logistics hub for the World Food Program, the West African nation of Ghana has attracted attention in areas that support the movement of goods. Warehousing in Ghana has benefited from associated investments from private business as well as public-private partnerships.
With a population of more than 31 million, Ghana ranks as one of the fastest-growing economies in Africa, according to the World Bank’s Logistics Performance Index. Located just north of the equator in West Africa, Ghana’s coast runs 328 miles along the Atlantic Ocean, providing easy access to global shipping lanes.
Ghana channels its exports through two principal seaports on the Gulf of Guinea, which is an embayment of the Atlantic. Tema is located fifteen miles east of the capital city of Accra. Takoradi is in the other direction, about 113 miles west of Accra. In addition, Ghana has four international airports, including Accra’s Kotoka International Airport.
While the COVID-19 pandemic has disrupted economic activity in Ghana and worldwide, it also has forced African nations to find innovative solutions for trade. The continent is undergoing rapid change. After a six-month delay due to the pandemic, the African Continental Free Trade Area (AfCFTA), headquartered in Accra, launched in January 2021.
AfCFTA created the largest free-trade area since the formation of the World Trade Organization. Africa’s 1.2 billion people and combined gross domestic product of $3 trillion now create a single market for goods and services. Aspects of AfCFTA include reductions in tariffs, the free movement of people, and the emergence of new trade routes.
The signatory countries expect AfCFTA to boost trade within Africa and promote industrialization. Like other African governments, the Ghanaian government is determined to drive investment into its logistics infrastructure to support the emerging continental market. This includes improvements to ports, road systems, and warehousing in Ghana.
Benefits to renting warehouse space in Ghana
Several government initiatives have spurred the development of logistics in Ghana since the 1990s.
Investment incentives
To promote real estate investing in Ghana, the government passed the Ghana Investment Promotion Centre Act in 1994. The act established a government agency (the Ghana Investment Promotion Centre) specifically for encouraging and promoting investments in Ghana. In particular, the agency seeks to provide a transparent and attractive investment environment by facilitating the following:
- An investor registration process
- Work and residence permits for employees
- Import duty exemptions for machinery
- The acquisition of permits and approvals
Free zones
In 1995 the Ghanaian parliament passed the Free Zone Act, which established the Ghana Free Zones Authority (GFZA). The GFZA regulates certain special areas within which companies can produce, receive, and store goods without paying customs duties. In addition, real estate developers receive an exemption from property tax for their first eight years of operations.
The World Bank has recognized Ghana’s efforts. Its report Doing Business 2019: Training for Reform noted the following improvements:
- Easing trade across borders: Ghana has improved electronic document processing and submission for imports. Also, it has enhanced customs administration and inspections for imports and exports.
- Strengthening construction quality control: Ghana has imposed stricter qualification requirements for professionals in charge of inspections.
Location
By virtue of its location, cargo and travelers in Accra can reach Europe or the Americas by air in around eight hours. In addition, Ghana has an underdeveloped inland water transport system with great potential. Lake Volta winds 250 miles past important Ghanaian towns and connects to the Atlantic Ocean. Despite numerous constraints that affect industrial development, cargo ferries and barges carry an estimated 255,000 tons of products every year.
Furthermore, the Ghana Shippers’ Authority (GSA) has completed feasibility studies for warehousing projects at Buipe, a town in northern Ghana. Buipe sits on an inlet of Lake Volta. The GSA hopes to make use of its location to provide warehousing facilities to shippers, especially those from landlocked countries.
New terminals
Ghana has undertaken additional projects to attract logistics providers. For example, in 2016 the Ghana Airport Cargo Center (GACC) opened at Kotoka International Airport in Accra. A public-private partnership funded the 10,000 square meter (108,000 square foot) warehouse. The GACC features high-speed internet as well as solar water heaters and an in-house water filtration plant. The warehouse also has LED lighting and panoramic lifts for handling air freight and other cargo.
In addition, the Ghana Ports and Harbour Authority, a container terminal operating company, and a French logistics firm partnered on a new container terminal in Tema. The $1.5 billion investment increases the access of Ghana to the global trade market.
Infrastructure investment
An additional project focuses on expanding the road between Accra and Tema to a six-lane modern highway. The project is a collaboration between an international container terminal operating company, the government of Ghana, and a nonprofit road safety organization. The project also will improve connecting roads and access points between Tema and inland destinations.
e-Commerce
A report by the McKinsey Global Institute indicates e-commerce activity in Africa could reach $75 billion by 2025. The report designates Ghana as an “emerging” nation in terms of its internet economy and foundations for future performance.
The expansion of e-commerce depends on the availability of warehouses that meet international standards. According to the World Economic Forum, e-commerce logistics requires four times the warehouse capacity of a traditional fulfillment model.
Improvements to warehousing space in Ghana
For years, African countries relied on “godowns” for the storage of goods. A godown functions as a sort of makeshift warehouse that a retailer may use to store its own goods. Godowns lack certain basic features that meet international standards, such as reliable power, internet connectivity, security and protection from weather and the elements.
But as the Ghanaian government recognizes the importance of upgrading infrastructure, it has emphasized simplifying the development of commercial property.
Procedure simplification
The Ghana National Single Window program allows importers and exporters to file all necessary documentation in one place. Previously, a tangled web of paperwork contributed to inefficiencies in logistics management. Centralizing these requirements into one online repository simplifies the process for a logistics company seeking to operate in Ghana.
Warehouse certification
In 2019, the Ghana Commodity Exchange (GCX) launched a program to promote the use of warehouse receipts for trading and financing. After a farmer stores goods in a warehouse, the GCX produces an electronic receipt. The farmer may then use the receipt as collateral to secure a loan or as a commodity for trade.
Warehouse receipt finance has underpinned development of several countries in Africa, most notably Ethiopia, South Africa, and Tanzania. The GCX hopes to see similar growth in Ghana, where agriculture is a key sector of the Ghanaian economy. Agriculture accounts for up to 20 percent of the gross domestic product and 60 percent of employment, according to Ghana Talks Business.
The government of Ghana owns the GCX and provided the setup capital for the warehouse program. The GCX trades contracts for immediate delivery of white maize, yellow maize, sesame, sorghum, and soya bean through several warehouses.
The Ghana Grains Council, an industry association supporting the grains industry in West Africa, lists twelve GCX certified warehouses throughout the country. It also lists twenty-two community warehouses still operating under manual warehouse receipt.
Waste reduction through warehousing in Ghana
The government of Ghana has been working to establish itself as an important gateway to the West African market. Ghana Vision 2020 was the government’s economic plan to promote the flow of foreign capital into Ghana and provide international-quality infrastructure services.
Perishable goods
Globally, about one-third of food gets lost or wasted, according to the Food and Agriculture Organization of the United Nations. In Africa, poorly managed storage contributes to much of this loss.
To reduce waste, modern warehouse facilities in Ghana utilize temperature regulation as well as pest control and security measures. In addition, consolidating warehousing for commodities and agriculture allows local processing to take place in facilities used for storage.
For example, an aviation company developed the Air Ghana Perishable Centre (AGPC). The AGPC has features designed for the handling of perishable cargo designated for export out of Ghana. The facility has a refrigerator measuring 165 square meters (about 1,800 square feet) that can adjust to various temperatures.
In addition, the aviation company manages a 6,000 square meter (64,500 square foot) cargo facility in Accra. The warehouse has an automated storage retrieval system that can store up to 2,800 tons of goods. The facility also has three refrigerators offering various temperature ranges, all of which have sensors and alert systems to protect perishable goods.
Support for small and medium enterprises
A Ghanaian food producer consolidated its operations into a single production location. The company used a support program for small and medium enterprises (SMEs) to move into a ready-built warehouse that meets international standards. Thanks to the SME program from Agility, the company did not have to provide financial guarantees or raise capital. It moved into its new facility with just three months’ rent as a deposit.
Best practices for warehouse space in Ghana
In response to the COVID-19 pandemic, Agility offered free warehouse space to the World Health Organization (WHO). The WHO used Agility warehouses to stockpile medical supplies and the COVID-19 vaccine in Ghana and its other centers.
Setting the standard with Agility Ghana
Agility Ghana operates a forty-five-acre state-of-the-art industrial park in the Tema Free Trade Zone. The Ghana Agility Distribution Park is the first of a planned network of logistics parks Agility plans to build across Africa. The network has already expanded to include logistics parks in Mozambique, Ivory Coast and Nigeria.
Agility has a lease agreement with various types of tenants. Agility rents to multinational companies seeking to enter the market of West Africa. Also, small- and medium-sized Ghanaian companies looking to expand light manufacturing and their import-export businesses have a lease agreement. Agility is building seven more warehouses at the Ghana park, and it offers build-to-suit options for companies with specific requirements for rental property.
Sustaining environmental awareness
All Agility distribution parks meet international environmental standards. For example, the Ghana facility uses an energy-efficient roof and side-insulated panels as well as wind-driven roof fans. For lighting, it has skylights, LED and energy-saving bulbs, and solar-powered streetlights. Agility offers ecofriendly waste management services: the site recycles paper, plastic, metal, and carton waste.
Agility logistics parks also feature laydown yards. These are open spaces within the site to store a wide range of products, from vehicles and engineering components to oil and gas industry equipment. An online stock management system controls the movement of goods in and out of the laydown yards.
Agility’s laydown yards sit inside a separate fence within the Agility outer compound wall and feature constant security monitoring. In fact, all of Agility’s rental property, including the Ghana Agility Logistics Park, feature twenty-four-hour security and reliable power and connectivity. Thus Agility sets an example for quality logistics infrastructure with its warehousing in Ghana.
Investing in the labor force
Beyond the development of physical infrastructure, Agility has invested in human resources. It has developed leadership programs throughout Africa for local employees and university graduates. These programs provide training in management and skills related to logistics. Participants in the program have the opportunity to gain experience by working with Agility in Ghana and around the world.
Contact Agility to find out more about the Ghana Agility Logistics Park. Find out how the logistics hubs that Agility is building across the continent can help your company with a logistics infrastructure that meets or bests international standards.
Africa has struggled for years with industrial development. A lack of infrastructure and funding in African countries has limited the continent’s ability to compete with titans of production such as those in Asian countries. The lack of trade, in return, has limited funding for infrastructure.
However, companies from China, Europe, the United States and the Middle East are now looking to Africa as a burgeoning market and as a new frontier for logistics infrastructure to support growth there. With foreign investment, Africa is building warehousing and industrial parks.
While each country’s ability to sustain these parks is different, research shows that the whole continent benefits. With the economic growth and new employment that international investments have brought, Africa is on its way to becoming a competitor in the global market.
Highest concentrations of industrial parks and warehousing complexes in Africa
There are active industrial parks in forty-seven African countries, with the largest percentages in Morocco, Ethiopia, and Uganda. Agility currently has logistics parks in four African countries: Cote D’Ivoire, Mozambique, Ghana, and Nigeria.
With plans to build more, Agility has seen the potential for providing secure, efficient warehousing for supply chain and manufacturing companies. Now, Africa is reaping the rewards of this investment, as some industrial parks have grown to house over one thousand companies.
Industrial real estate booms in eastern Africa
Ethiopia’s Growth and Transformation Plan aims to make the African country a major manufacturing hub. It began to realize this goal through Chinese investments: China funded several parks and a railway connecting Addis Ababa to the Djibouti port. This plan is increasing the country’s revenue, and Ethiopia will build its newest agro-industrial park without foreign aid.
In Kenya, Nairobi Gate is a centrally located warehouse and logistics park built with efficiency in mind. It is expected to attract business with its “built to suit” approach offering tenants flexible and customizable spaces. Agility’s logistics parks feature both built-to-suit warehousing and facilities, along with ready-built structures that are move-in ready. Industrial parks are also gaining popularity in Uganda because they offer more space at cheaper prices than traditional warehouses located in the cities.
Opportunities along the coast
With Africa heavily dependent on maritime trade, landlocked Ethiopia and Uganda rely on other countries for access to shipping ports. These two countries will need infrastructure improvements to fully participate in the global marketplace, but those on the coastline have already benefited.
Morocco’s Tanger Med in particular boasts a location along multiple major maritime trade routes and connections to 186 ports. South Africa and Egypt are also hubs where many international shipping routes connect, and Djibouti is a notable subregional port. All four of Agility’s warehouse parks are on coastlines as well: three in western Africa and one in the south.
Benefits of warehousing and industrial parks in Africa
African leaders know that industrialization is key to improving economic conditions in all countries. It not only creates jobs but will also eventually enable African countries to compete in the global manufacturing market. The key is for international companies to bring their business to Africa. With foreign companies eager to invest, it is truly a winning situation for all parties involved.
Incentives for international companies to develop industrial parks
Africa provides many incentives for manufacturers looking to save production costs and establish new supply chains. Lower wages and a growing population of workers make African countries an attractive alternative to historically Asian production centers, and new legislation could lead to a major shift.
The impending African Continental Free Trade Area promises a continental market with unified standards between member countries and lower tariffs, eliminating several current barriers to foreign direct investment. The young population and high unemployment rate also create the opportunity for long-term employment and economic growth, especially if companies train their workers.
The Agility Logistics Park in Tema, Ghana, for example, runs a program to provide local students with vocational and technical training, directly contributing to the growth of a qualified, skilled local workforce. In fact, Agility hires 100 percent of its Ghana employees locally.
Incentives for African countries to develop industrial parks
The presence of industrial parks has already increased foreign direct investment in many African countries. A significant percentage of national exports comes from industrial parks, increasing overall trade and economic performance for those industries and related sectors.
Local communities enjoy more employment opportunities, and the presence of warehousing and industrial parks provides potential for skills improvement for local workers. These parks have been notably effective at increasing the population of women in the workforce and supporting job creation in highly skilled sectors. They also create jobs indirectly through the infrastructure required to build and sustain them, such as road development and power supply.
Warehousing and industrial park regulations in African countries
A major drive for the construction of these parks is that current African warehouses do not meet international standards. Even beyond official regulations, countries need updated facilities to attract business. Manufacturing practices need improvement, especially with the increasing focus on sustainable production.
Widespread standards for warehousing and industrial parks in Africa
With the push for more environmentally friendly production standards, the African Development Bank has created policies based on the concept of sustainable development. Some key points for industrial parks include diversifying energy sources and improving public health through proper waste management practices.
The United Nations has also set guidelines for the development of industrial parks to ensure the well-being of both humans and the environment. These include global standards for industrial, environmental, and social infrastructure.
Countries’ responses to warehousing and industrial park regulations
Many African countries currently benefit from creating sustainable manufacturing solutions. Morocco, for example, has attracted foreign investors with its ambitious goal to generate 52 percent of its energy renewably by 2030. Thanks to these investors, the country is already running its special economic zone carbon neutrally. South Africa is also pursuing industrial energy efficiency as a solution to its currently strained power grid.
However, strict sustainability standards are not realistic across the continent, as not every country has the same capability to meet them. Ethiopia has been a topic of discussion for the past several years, as it lacks comprehensive zoning and land-use regulations. Without these factors, the government cannot enforce sustainable building practices for industrial parks.
Technological advancements in warehousing and industrial parks in Africa
African countries’ varying ability to implement rising standards also blocks new technologies that simplify and cheapen supply chain logistics. Artificial intelligence (AI) is increasingly popular in the logistics industry, reducing time and costs, and the COVID-19 pandemic accelerated this transition.
AI technology in the supply chain industry
Though AI technology is not perfect, it is still an improvement over human error. Self-driving cars may still need a human supervisor, but AI can complete many routine tasks such as modifying orders without intervention, leaving employees free to focus on more important and complicated tasks. The whole operation runs more efficiently and, in many cases, safely.
Obstacles to implementing warehouse automation in Africa
Because African countries are just starting to build warehousing and industrial parks, many workers require basic training before employers can consider introducing AI and machine-learning technology. Even worldwide, educational programs are only now beginning to teach the fundamental skill set that AI technology requires, and these are especially scarce in Africa. While company training programs can help fill this gap, traditional education systems also need improvement.
Lack of necessary education is not the only obstacle that stands in Africa’s way. Others include the following:
- Reliance on electricity and internet for AI—two things that are not always consistently available or affordable
- Concerns about ethical use and data collection
- Possibility of bias in algorithms, especially those written in countries with a predominantly white population
- Limited access to large sets of data
However, with increased revenue and economic growth from warehousing and industrial parks, many countries may soon invest in programs, policies, and infrastructure. In turn, these will help remove obstacles and reduce the gap between Africa and more industrialized nations.
The future for warehousing and industrial parks in Africa
Many challenges remain for Africa to become truly industrialized, and each country will likely progress at its own rate. However, the continent as a whole is benefiting from foreign investment into warehousing and industrial parks in Africa. Many countries have seen significant economic growth in the past several years, and foreign direct investments created jobs and educational opportunities.
As more international companies take advantage of low wages and sustainability measures that ensure efficient production costs, Agility plans to expand its existing operations. It currently operates in twenty-two countries across Africa, providing freight forwarding, airport services, liquid fuel logistics, camp construction, catering, remote life support, and more. In the future, Agility plans to build more logistics parks to client specifications.
Establishing business in Africa may seem overwhelming. There are potential risks—from unmet infrastructure and sustainability standards to the cost of building large facilities and developing employee training programs. Contact Agility today to help mitigate these risks and design the right solution for your company and its products.
Substantial opportunity and potential exist in light manufacturing in Africa. For decades, African countries have struggled to industrialize at a level that can sustain jobs and produce a significant share of their goods. Political instability and major restrictions on trade and manufacturing have kept Africa from reaching its potential. Today, thanks in part to a new free trade agreement, Africa joins a renewed industrial revolution.
The light manufacturing industry
The modern industrial world generates a large number of well-paid jobs and connects many sectors of business, increasing the supply of consumer products distributed around the world. With light manufacturing requiring a low investment of overall capital and providing significant growth opportunities, the industry is a heavyweight in many developing economies.
Overview of light manufacturing
When many think of the manufacturing industry, they may envision enormous industrial plants packed with massive machinery and bustling with giant rigs and freighters. For the heavy manufacturing industry, this vision is accurate. But a dissimilar industry, one with lower environmental impact and lower reliance on heavy machinery, invokes a brighter image.
Heavy manufacturing transforms raw materials into large products used by other sellers later in the supply chain. By comparative advantage, light manufacturing produces small, high-value items destined for direct sale to consumers. This industry includes sectors in the production of food, clothing, electronics, paper, medications, and automobiles. Consumers use these products regularly, so the light industry requires quick and constant output.
Because it is less reliant on large plants and requires less capital investment for production and exportation, the light manufacturing industry is democratically dispersed throughout the world. Countries such as Brazil, Japan, China, and the United States are leaders in this industry. But according to an article from Industry Week, several African countries are now poised to move up the light industry ladder.
The status of light manufacturing in Africa
Though the manufacturing industry in Africa saw growth before the 1980s, shocking changes in the economy, especially after the COVID-19 pandemic, led to a decline. Regulations and instability forced many African populations to work in the informal sector and stifled manufacturing efforts. Until recently, Africa’s manufacturing industry suffered from heavy competition and low gross domestic product.
Despite these trends, some countries enjoy benefits from the light industry, including rising wages. And although manufacturers must still make efforts at expansion, connectivity, and infrastructure, the continent’s manufacturing production increased from $73 billion to $157 billion between 2005 and 2014. In addition, significant advancements in sub-Saharan Africa continue to develop, shifting economies from mineral-based sectors to consumer and service sectors.
For instance, light manufacturing efforts in developing countries such as Ethiopia, Uganda, and Nigeria are on the rise, particularly in production of food and beverages, packaged goods, fabrics, and furniture. Sub-Saharan Africa benefits from low labor costs, substantial resources, and favored international trade access with US and European markets. To further increase trade logistics, a key component of light manufacturing, African countries work to implement new procedures to increase automation and improve risk management systems.
Benefits of light manufacturing
Unlike heavy manufacturing, light manufacturing activities do not require heavy machinery or sizable amounts of raw material. Thus, they consume less energy and minimize the environmental impact. These characteristics make light manufacturing possible in and around cities and residential areas.
Light manufacturing does not require large areas of land for huge facilities. This results in a decreased need for power, equipment, and materials, making this industry less capital intensive. As an added benefit, the industry’s direct-to-consumer aspect makes it specifically designed for buyers.
In Africa, these benefits are of considerable value. Working to transform the economy, industry leaders in Africa work to support its expansive population. The light industry is labor-intensive because of high-demand production, so it contributes to job creation. Increased job creation makes long-term investments in skills training and education necessary for developing Africa’s manufacturing capabilities.
World Bank economist Hinh Dinh states, “No country in the world has developed without producing light manufacturing. And no country can skip it.” According to an article from New China, Ethiopia gained 23,000 job opportunities from the creation of a single light manufacturing industrial park. Continued supportive and collaborative efforts among African governments, stakeholders, and private sectors are essential if trends like these are to continue.
Regulations for light manufacturing in Africa
Demanding policies and regulations stifle these collaborative efforts and place serious limitations on Africa’s economic competitiveness in manufacturing. Having open trade and support from foreign investors and suppliers is crucial for the success of African economies.
Light manufacturing challenges in Africa
Some challenges African countries face in gaining this support include establishing reputations for reliability in trade and improving infrastructures for better network connectivity. Instances of corruption and crisis have led some trading partners to consider African trade to be high risk, and unreliable internet service impacts growth capabilities.
Barriers to trade in goods and services provide further challenges. Direct and indirect costs of international trade are some of the highest in the world, and the system of tariffs can be complex. For example, South Africa has nearly forty different tariff rates. In addition, some African countries maintain strict access to banking, insurance, engineering, and legal services.
Heavy competition from Chinese companies and other Asian markets causes an imbalance in supply and demand, forcing African governments to increase prices and tighten regulations and restrictions. To keep better control over trade and local economies, they must establish stringent qualification requirements for market entry, licensing, taxation, and foreign ownership.
Regulations to know when doing business with Africa
Though reforms are underway in many areas, African governments often impede efforts of doing business both within the continent and with other continents. Poorly considered tax policies, local content requirements, and restrictions on trade are key constraints. Governments in Africa emphasize making investments in domestically manufactured goods and services to raise revenue.
Recent frustrations from would-be foreign investors include frequent policy changes from African governments, making subsidies and trade unpredictable. The less stable business models that some companies hold can lessen confidence and credibility, as do continued arguments among trade regulators regarding taxation. Outmoded infrastructure and varying quality standards also contribute to business difficulties, particularly due to unreliable access to power and underdeveloped human capital.
High-level professionals from both the public and private sectors suggest that local content regulations require transformation. The best way to accomplish this is to find methods that are strict enough to develop local economies but loose enough to avoid deterring corporations. Until then, those doing business with Africa may find themselves restricted by red tape and conflict. Still, some ease in regulations and a new wave of technology are helping lower costs of doing business.
Opportunities for light manufacturing in Africa
As African countries continue making advancements in logistics infrastructure such as ports, airports, and roads, and if they streamline customs procedures, opportunities for light manufacturing will blossom.
One of the newest and most promising opportunities for light manufacturing in Africa is in Ghana. Working with a committee formed by Ghana’s president, members of the European Union recently announced the possibility of the country becoming a hub for COVID-19 vaccine manufacturing. If this move succeeds, the European Investment Bank is ready to offer support to the project.
Other encouraging opportunities in Africa stem from a recent introduction of 5G wireless communication in several countries. With faster and more efficient connectivity services, African countries can expect to see this advancement in technology boost their manufacturing capabilities. The article from Industry Week points to an example of this with General Electric planning to spend $1 billion in Nigeria by 2023 to help strengthen the country’s manufacturing and product services.
Additionally, governments in Mozambique plan to implement policies that will help spread wealth, bolster the economy, and create competitive market pricing. This boost will encourage more efficient processing of high-quality material production and enable businesses to capitalize on Africa’s availability of natural resources.
Africa’s budding industrialism
these regions, manufacturing is the fourth-largest industry. And South African Market Insights reports that the food and beverage sector of the light industry contributes to 25 percent of manufactured goods in the country.
Of note are the advances in Ethiopia and Rwanda. According to the article from New China, Ethiopia strives to become the manufacturing hub of Africa. The country has already invested $1.3 billion toward constructing industrial parks and aims to have thirty parks in place by 2025. In Rwanda, a boost in the manufacturing sector stems from high-quality infrastructure and the introduction of technical schools and on-the-job collaborative training programs.
Founders of the African Continental Free Trade Area (AfCFTA) intend to see this success continue. The agreement untangles customs procedures and lifts manufacturing and trade restrictions. The implementation of the AfCFTA will provide African countries with major opportunities for ending extreme poverty through long-term growth.
Light manufacturing in Africa: A budding industry with considerable opportunity
Regardless of restrictions and challenges, there is great potential and opportunity for light manufacturing in Africa. Economists expect spending and investment in the industry to reach over $666 billion by 2030.
Agility supports Africa’s economic growth and contributes to the continent’s budding light manufacturing industry. Recently, with a focus on structural transformation and sustainability, Agility opened new logistics parks in Mozambique, Ghana, Cote D’Ivoire, and Nigeria.
Find out more about Agility’s investments in logistics in Africa.
Although Africa has become a hotbed for investors looking to expand enterprise and penetrate new markets, many logistics problems in the West African subregion remain. West Africa comprises seventeen countries that historically have lagged behind other African regions in terms of infrastructure and political stability. Despite setbacks, many nations, such as Nigeria, Côte d’Ivoire, and Benin, are emerging as Africa’s leaders in trade. According to Agility’s Emerging Markets Index report, Nigeria is ranked tenth in the world for domestic logistics and growth in intraregional trade. A few of the reasons why West Africa has attracted so much foreign interest include its natural resources, its growing middle class, and the recent adoption of the African Continental Free Trade Area. Moreover, the United Nations Department of Economic and Social Affairs predicts that Africa’s sub-Saharan regional GDP will grow by 3.4 percent in 2021—even despite the impact of COVID-19. Manufacturers and businesses hoping to take advantage of West Africa’s projected economic development, however, must examine the unique challenges and conditions they face in supply chain management before making the move abroad.
Common logistics challenges with West African e-commerce
In 2020, e-commerce experienced unprecedented growth. Global e-commerce traffic hit 22 billion visits in June. For many retailers and manufacturers, e-commerce has become a primary method of conducting business. However, Africa trails the rest of the world in e-commerce. Lack of widespread broadband access, cybercrime, underdeveloped postal systems and other challenges confront businesses trying to sell online. Widespread cybercrime Cybersecurity remains a primary concern for e-commerce in Africa. In 2017, cybercrime cost Africa an estimated 0.20 percent of its annual GDP, according to a report published by the World Trade Organization. Nigeria and Ghana experience some of the highest rates of cybercrime in the world. According to a recent article by Deloitte, Nigeria saw a 20 percent increase in phishing scams in 2020 compared to 2019. An increase in use of digital platforms spurred by the COVID-19 pandemic is likely to blame. Since these countries see some of the highest rates of cybercrime in the world, West African consumers generally avoid sharing their personal information over the internet and distrust online shopping. Moreover, many African countries do not have legislation in place to protect consumers from online fraud, which further exacerbates consumer hesitancy toward e-commerce. Underdeveloped postal services Historically, street addresses in Africa were established in populous city centers, and few if any address networks were extended to outlying areas or rural areas. Since the creation of the West African Postal Conference in 2012, the region has moved toward a more integrated postal system across developing countries. However, postal services are slow to incorporate the use of information and communications technology (ICT) into their daily operations, which slows down the efficiency of this process and others. Africa’s land mass is larger than China, Europe, and the United States combined. Africa is home to more than one billion residents, yet the efficiency and reach of its postal systems fall drastically behind those of the rest of the world. Africa had nearly 3,300 outsourced postal offices and 8,300 owner-operated post offices in 2018. In comparison, the Asia-Pacific region had nearly 100,000 outsourced offices and 227,000 owner-operated ones in the same year. Because of underdeveloped postal services, e-commerce can be especially challenging in West Africa. Tracking the flow of goods and reverse logistics is difficult, and some remote areas remain without street addresses. Lacking ICT infrastructure In general, West Africa has severe gaps in ICT infrastructure. The majority of Africa’s developing countries experience barriers in internet usage, such as bandwidth constraints, unreliable connections and frequent power cuts. Building ICT infrastructure is costly and requires skilled workers, and several West African countries are among the poorest in the world. On top of that, the cost of internet access is much higher in West Africa than in other regions. The lack of ICT knowledge and ICT infrastructure results in a digital divide that affects e-commerce. Africa’s digital divide stifles the rise of online communities—a necessary factor for full participation in the second wave of e-commerce.
Factors affecting industrial logistics in West Africa
Recently, many foreign countries, such as the United States and China, have invested in infrastructure projects with the hopes of helping Africa realize its full potential within the global economy. Although West Africa is developing rapidly, its countries still score relatively low on the World Bank’s Logistics Performance Index. Sierra Leone, for example, ranks 164th out of 167 countries. Identifying ways to optimize costs and operational efficiency can be exceedingly difficult in West Africa’s fragmented markets. The logistics problems in West Africa that manufacturers must overcome include issues with the transport of goods and an overreliance on raw materials. Issues with the transport of goods According to the International Road Federation, sub-Saharan Africa—a region that includes most of West Africa—accounts for 6 percent of global road networks despite representing 17 percent of global land mass. Comparatively, the North American continent accounts for 21 percent of the world’s road networks. This creates major challenges in the transportation of goods and intraregional trade for the African continent. For example, intra-African trade accounted for just 19 percent of Nigeria’s exports and 8 percent of its imports between 2019 and 2020, according to Africa’s Trade Law Centre. Large sections between Côte d’Ivoire and Senegal lack modern, connecting highways. Rural areas in many African nations are cut off from the supply chain completely. Moreover, the lack of road infrastructure can cause difficulties in sourcing raw materials and fulfilling domestic orders. On the other hand, the high costs of ocean and air freight in West Africa impact inbound and outbound logistics. Recently, construction of African airports has been on the rise, but the vast majority of trade is done by boat. Key ports in West Africa include Abidjan, Côte d’Ivoire, and Lagos, Nigeria. Even with recent expansion, there still isn’t enough port capacity to meet demand and bolster the West African economy. Reliance on raw materials Although West Africa is steadily developing, most of its countries’ economies are still resource- based. This is also true for other African regions, such as Central Africa and North Africa. West Africa’s biggest industries include agriculture, mining, and oil. Outside of cities, many of West Africa’s rural inhabitants rely on employment in unskilled labor. Less than 30 percent of Burkina Faso’s population was living in urban areas as of 2019. Africa is rapidly urbanizing, and consumer demand and incomes are closely tied to the rate of urbanization. Although some West African countries have a growing middle class, other parts of the region still have high poverty rates. In several West African countries, more than 30 percent of the population live on less than $1.90 a day, according to Oxfam International. Reducing that percentage will be the key to unlocking stronger consumer demand. Inactivation of the labor market With some of the highest fertility rates in the world, West Africa has the potential for a substantial workforce. By 2040, Africa is expected to have a larger working population than India and China combined. However, there are many systemic challenges to sourcing skilled, experienced workers for the logistics industry. According to the World Bank, sub-Saharan literacy rates sit at 65 percent, which falls behind the global literacy rate of 86 percent. Mali has a literacy rate of 35 percent, making it one of the lowest in the world. High levels of illiteracy have to do with ineffective education systems. Furthermore, when looking at education attainment by gender, severe inequalities emerge between African men and women. Moreover, unemployment rates among Africa’s youth (ages fifteen to twenty-four) are significantly higher than those of other demographics. As of 2018, Burkina Faso’s and the Gambia’s youth unemployment rates sat at 49.1 percent and 53.5 percent, respectively. All of these factors combine to create problems with sourcing talent for production, leaving SMEs at risk.
Solutions to mitigate logistics problems in West Africa
Despite the many challenges in the logistics, retail, and manufacturing sectors, Africa’s future is promising. The establishment of the Economic Community of West African States has led government leaders to take a unified approach to policy changes. These changes are expected to facilitate the harmonization of West African countries and in turn lead to economic growth. In the meantime, SMEs are finding innovative ways to mitigate logistics problems. To reap the most benefits from its untapped markets, many logistics companies have begun to open the gates to mobile commerce (m-commerce) and adopt alternative forms of transport. Regardless of the approach, logistics companies must be flexible and dynamic to foster sustainable growth and optimize their supply chains. The boom in m-commerce Although e-commerce is in its early stages in West Africa, m-commerce is on the rise. Many local SMEs have penetrated new markets with this form of transacting. M-commerce has been widely adapted in West African countries for two reasons: first, the growing youth population has been quick to adapt this technology; and second, mobile data costs less than the costs associated with internet infrastructure and usage. In fact, m-commerce may be the key for retailing and identifying consumer demands. According to the 2019 Mobile Economy West Africa report, 70 percent of total telecommunications connections will be via smartphone by 2025, up from 38 percent in 2018. The report also finds that the mobile industry will contribute an estimated $68 billion to GDP in 2023, which is nearly 10 percent of the total estimated GDP. SMEs should invest in mobile formats for marketing their products and cultivating new customers. Furthermore, the use of GPS and tracing technologies may help curb the challenges associated with the postal systems in West African countries. Alternative forms of transport Despite West Africa’s fragmented road networks, African SMEs are outfitting their own supply chains with non-traditional forms of transportation. Many local businesses have invested in motorcycles, referred to locally as boda bodas, to deliver goods domestically. Motorcycles are better suited to handle different terrain and navigate traffic jams than delivery trucks. The COVID-19 pandemic has also prompted the use of drones to deliver vaccines to remote areas of West Africa. Applying this technology to the supply chain can benefit SMEs greatly. With drone technology, SMEs can avoid exorbitant fees for shipping freight by air while increasing flexibility in order fulfillment. Drones may even play a role in sourcing materials for production in the future.
Benefits of working with a company that specializes in supply chain and warehouse logistics in West Africa
One of the biggest challenges logistics companies must overcome is an overall lack of infrastructure. However, building infrastructure needed for end-to-end supply chain management can be uneconomical. Logistics costs, even in more urbanized areas, can add up. For example, total logistics costs in Nigeria amounted to $71.9 billion in 2019, which made up 5 percent of the continent’s total logistics costs. As a result, many start-ups and SMEs can benefit from using a third-party logistics company that is already well established within the region. When considering expansion into West Africa, businesses should identify their core competencies and focus on them. As for the remaining gaps in the supply chain, logistics infrastructure providers such as Agility offer facilities that act as platforms for growth in the region. Logistics parks de-risk market entry and expansion, allowing companies to conserve working capital by storing, distributing, assembling and processing their goods at secure, connected, international-standard facilities funded, built and run by professionals. To discover how Agility is solving logistics problems in West Africa for companies both large and small, check out these case studies.
Africans make up 12% of the world’s population but only 2.5% of the world’s passengers. Why the gap?
Africa has 731 airports and 419 airlines with an aviation industry that supports around 6.9 million jobs and USD 80 billion in economic activity. According to the International Air Transport Association (IATA), Africa is set to become one of the fastest growing aviation regions in the next 20 years with an annual expansion of nearly 5%. While it is evident that aviation in Africa has the potential to fuel economic growth, several barriers exist. Weak infrastructure, high ticket prices, poor connectivity and lack of liberalisation rank amongst the many challenges.
Consider the reality: Airport infrastructure in most African countries is outdated and not built to serve the growing volume of passengers or cargo. Airlines and airports are often managed by government entities or regulatory bodies. Foreign investment is discouraged. In Malawi, for example, it’s illegal for a foreign airline or private investor to own more than 49% of a national airline. So, this prevented Ethiopian Airlines from purchasing more than a 49% stake in Malawian Airlines.
Yet, modernising infrastructure and operations requires both investment and expertise, ideally from public-private partnerships. Africa needs to open its doors for private capital investment. Countries such as Côte d’Ivoire and Rwanda are heeding this call and making strategic bets in the sector while employing best practices to drive vibrant aviation growth. Take the outstanding example of the Abidjan International Airport. In 1996, management and operation of the terminal in Côte d’Ivoire were privatised and awarded to AERIA, a French company. Ownership of AERIA is shared by private investors (65%), a technical partner (25%) and Côte d’Ivoire (10%). The company has invested in infrastructure and delivered quality service, impressing the government so much that the concession has been extended.
With private capital involved in the mix as in Côte d’Ivoire, partnerships can build greater efficiency, higher revenue and better quality service that demand financial discipline and eliminate corruption. Still, governments have an important role to play in delivering economic and social benefits by championing intercontinental aviation as well as shaping a dynamic African aviation sector.
Liberalisation will bring strong outcomes – new routes, more frequent flights, better connections and lower fares. These improvements will increase the number of passengers, which will have both direct and indirect positive effects on trade, business travel and tourism. In turn, this has impacts for the broader economy, generating more tourism revenues, jobs and productivity. They will enhance the GDP of African countries and uplift the welfare of ordinary Africans. According to an IATA survey, if just 12 key African countries opened their markets and increased connectivity, an extra 155,000 jobs and USD 1.3 billion in annual GDP would be created in those countries. A study by InterVISTAS Consulting shows that in South Africa, liberalisation could yield an estimated 15,000 new jobs and generate USD 284 million in national revenues.
On the other hand, the lack of liberalisation affects connectivity and ticket costs. In Africa, no direct flight exists to travel from Abidjan, a hub in West Africa, to Dar Es Salam, a hub in East Africa. Instead, a traveler inefficiently flies to a second or third country before reaching the final destination. Across the globe, on average, low-cost carriers are about a quarter of all flights. In Africa, however, they don’t even reach 10%, which obviously makes ticket prices somewhat prohibitive.
So what’s ahead for Africa’s skies?
First, the Single African Air Transport Market introduced earlier this year aims to open up Africa’s skies and improve intra-African air connectivity. So far, 26 African countries have signed up. The movement is promising and will be more effective once all African countries come onboard.
Second, visas need rethinking. Only 14 out of 54 African countries currently offer visas upon arrival to African nationals. Difficulties in obtaining visas for intra-Africa travel affect travel and tourism. But visa openness underpins the continent’s tourism sector and can create many more skilled jobs. The AfDB’s Africa Tourism Monitoring Report outlines that a visa liberalisation scheme could increase tourism by 5% to 25%. Increased tourism will give rise to new businesses opportunities in transport, hotels, shopping malls and restaurants. For the 60% of African youth who are currently unemployed, this means a new job market, which also prevents local brain drain in the long run.
Indeed, the advantages of increased mobility are many. Not only the Schengen Agreement and the Gulf Cooperation Council, but also African countries that have eased visa restrictions, demonstrate this reality. Rwanda, for one, is a strong supporter of Visa Free Africa. On opening a visa on arrival to all African citizens, the country saw a 24% increase in tourism arrivals and a 50% increase in intra-African trade. Trade with the Democratic Republic of the Congo alone increased by 73% since the implementation of the policy. And when Rwanda abolished work permits for East African citizens, the country’s trade with Kenya and Uganda increased by at least 50%. Seychelles too saw benefits as one of the few completely visa-free countries in Africa. After adopting the policy, Seychelles saw an average 7% increase per year in international tourism into the country between 2009 and 2014.
Ultimately, by 2035, Africa will see an extra 192 million passengers a year for a total market of 303 million passengers traveling to and from African destinations. The top ten fastest-growing markets in percentage terms are in Africa: Sierra Leone, Guinea, Central African Republic, Benin, Mali, Rwanda, Togo, Uganda, Zambia and Madagascar. Each of these markets is expected to grow by more than 8% each year on average over the next 20 years, doubling in size each decade. Thus, while challenges exist, so do the opportunities according to these forecasts. With public-private partnerships for upgrading infrastructure and operations, open skies, and visa liberalisation, aviation in Africa is sure to soar. The question now is: How soon can we make this happen?
This article was originally published by OECD Development Matters. Read the full article here.
A sustainable vegetable garden in the arid demilitarized zone between Sudan and South Sudan brings relief to workers supporting the peacekeeping mission.
At the remote end of the supply chain, Agility’s GCC Services team of 105 expats and local staff supplies international peacekeepers with food and bottled water that is trucked hundreds of miles from the Port of Sudan to the mission in Abyei, Sudan.
Desperate for a quiet respite and something fresh to eat in a conflict zone, GCC personnel built a composting operation to turn kitchen waste into fertilizer and began bringing seeds back to Abyei when they returned from leave. The result is a lush, pesticide-free garden of herbs, vegetables and fruit.
The Abyei kitchen garden has yielded large quantities of nutritious beans, peas, jackfruit, guava, lemons, bananas, cassava, tomatoes, aubergines, cucumber, okra, watermelon, lettuce, coriander and other produce.
“This sounds like a small thing, but it’s not. Conditions in Abyei are austere, and the workdays are very long,” says Rashad Sinokrot, CEO of GCC Services. “The kitchen garden has created shade and greenery where there isn’t much of either. It’s been a stress reliever and teambuilder, and demonstrated that you can do something sustainable in a very harsh environment.”
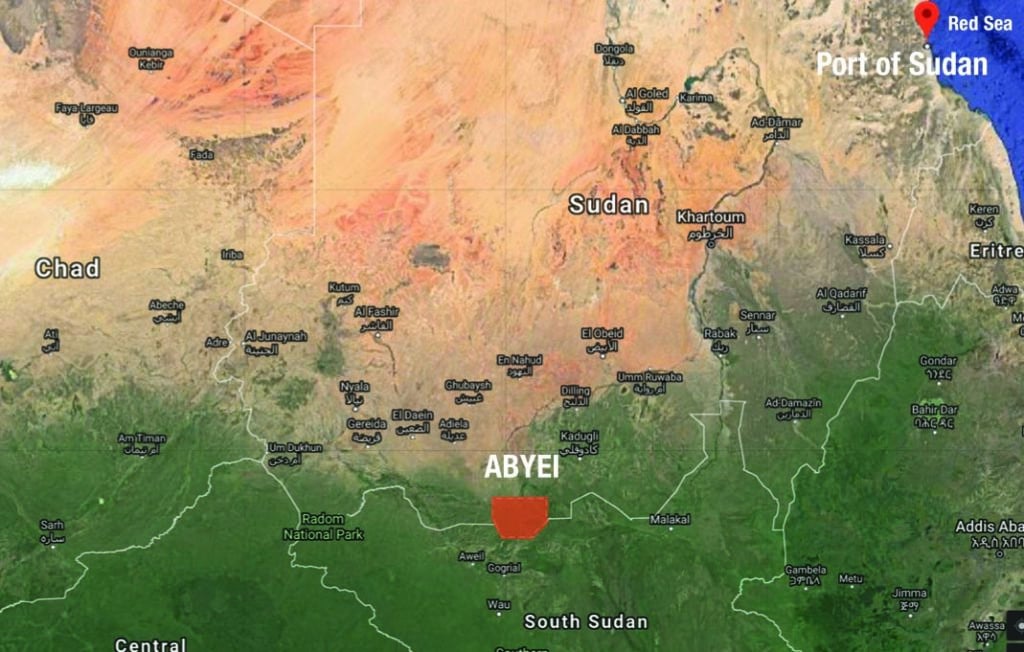