How Better Warehouses Increase Trade in Africa
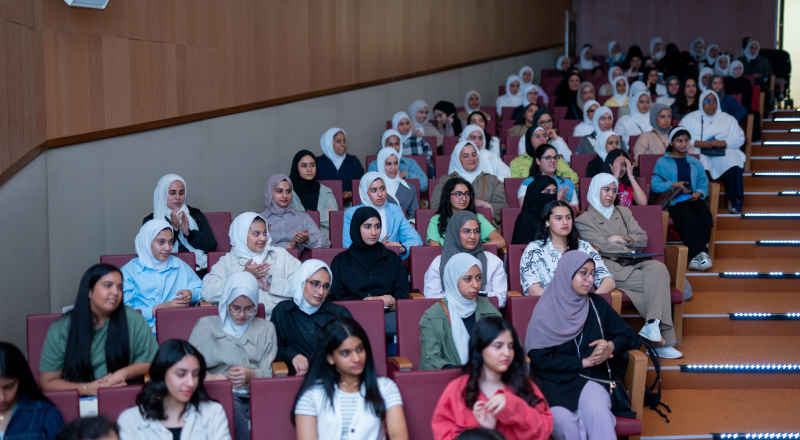
Kuwait-based Agility Logistics Parks customers can log-on to view contracts and make payments.
UK MOD personnel can log-in to the GRMS portal to schedule household relocation shipments.
Kuwait-based Agility Logistics Parks customers can log-on to view contracts and make payments.
UK MOD personnel can log-in to the GRMS portal to schedule household relocation shipments.
The physical and geographic features of a commercial real estate property determine its value. Rather than listing a long series of features, agents and brokers can summarize this value with a classification system ranging from A to C. At the high end are international-standard Class A warehouses.
More than simply storage buildings, international-standard Class A warehouses are the linchpin in modern, efficient supply chain logistics strategies. Read on to learn more about the characteristics and benefits of state-of-the-art Class A warehouses, the difference between a Class A warehouse and a Class A facility, and how to choose a Class A warehouse.
In short, international-standard Class A warehouses are state-of-the-art properties built specifically for warehousing and logistics. They have not been converted or renovated for this purpose. They are designed and built from the ground up to benefit the supply chain.
Before delving further into Class A characteristics, a brief look at other levels might prove helpful. A step down from Class A is Class B. Such a building may be a little older but renovated to have the latest and greatest technology. It will also have lower ceilings than a Class A building and may have multiple floors, which is not ideal for warehousing.
Class D and Class C buildings fall at the low end. They are typically older buildings converted from their original purposes, such as former hangars and manufacturing facilities. They often lack modern amenities, such as climate control and accessibility.
Noncombustible or fireproof raw materials, flexibility, and mobility are essential aspects of Class A warehouse construction. Steel and sealed concrete are the most common structural elements with the possible addition of masonry, plaster, gypsum, or other noncombustible materials. Note that sealing concrete is essential to reduce dust that can cause wear and tear on equipment.
Glass, ceramic or stone tile, and stucco can enhance the aesthetic value of interior and exterior walls. Few people want to work in a bare steel and concrete box.
The warehouse might store a variety of inventory with different storage needs. To accommodate these needs, a Class A warehouse will have ceilings at least thirteen meters high, support columns at least twelve meters apart, and spans of at least twenty-four meters.
And that’s just inside the building—what’s outside is just as important. It must have at least one automatic docking gate for every five hundred square meters of interior space and sufficient outdoor space to maneuver large trucks and for employee parking.
Technology and innovation are increasingly important in warehousing logistics. Four walls, support structure, and a roof are no longer sufficient. At a minimum, a Class A warehouse includes climate control, fire safety features, security monitoring and alarms, high-speed internet, and an electrical substation.
Beyond those requirements, automation is the future. An automated warehouse will include tech-based solutions such as drones that easily reach the highest shelves, robots (or “cobots” that work alongside humans), composite panels that improve the building’s energy efficiency, and more. Smart warehouses make smarter, more agile supply chains.
The old adage that location is everything in real estate is particularly true with warehouses. Class A warehouses are located at the confluence of airports, railways, ports, and highways for quick access to major domestic and export markets.
Other building classes might not be as ideally located if their region has grown and changed since their construction. For example, industrial facilities built before 2000 are often converted and renovated, but they might be gridlocked within cities that have grown up around them.
Because Class A warehouses are built specifically to suit a modern supply chain, the benefits are innumerable, ranging from optimized retail logistics to sustainability to safety. A few highlights include reduced carbon footprint and increased efficiency and accuracy.
Inefficient heating and cooling systems—such as those you might find in a Class C building—mean high carbon emissions. Just by virtue of being new construction, Class A warehouses have the proper insulation and roofing materials to maximize indoor climate control.
Green warehouse design is also a common feature in Class A warehouses. Such sustainable design might include solar panels for alternative energy, skylights for daytime lighting, LED bulbs to reduce electricity consumption, xeriscaping to reduce water usage, and regionally sourced building materials to reduce transportation-related emissions. Individually and collectively, these features reduce the building’s carbon footprint.
Finally, a prime location reduces transit times and fuel use, giving you both increased efficiency and a reduced carbon footprint.
Many of the features built into Class A warehouses increase efficiency right from the start. Smart warehouse management can then further reduce warehousing challenges and inefficiencies.
Optimal warehouse layout and layout flexibility, in particular, are huge time savers. High ceilings and wide spaces between columns and spans provide this flexibility. Stacking shelves higher puts related products in closer proximity. Wider aisles give people and equipment more room to maneuver quickly and safely.
Creating and adapting your rack design to your particular workflow ensures optimal movement throughout the space. A flexible layout also allows you to reorganize as inventory changes with supply and demand.
Zoning, both inside and outside the warehouse, is another important aspect of efficiency enabled by Class A space. With more automatic docking gates, some gates can be dedicated to receiving and others to dispatching to reduce traffic jams. Positioning popular products in proximity to dispatch areas gets them to market faster.
And as we all know, haste equals waste. Employees have more time to do their jobs thoroughly and effectively when efficiency is increased. Paired with warehouse automation, errors and waste are minimal.
Unfortunately, building classification isn’t always consistent from market to market, and confusing language sometimes arises. Commercial real estate agents use the Class A designation on a variety of facilities, such as office space, light industrial space, distribution centers, and even warehouse space that doesn’t quite meet the criteria of a Class A warehouse.
In the case of warehouses in particular, distinguishing between these types of buildings is important. A large space dubbed a Class A “facility” instead of “warehouse” might have lower ceilings (at least ten meters instead of thirteen), which reduces options for shelving, and fewer automatic docking gates (one for every seven hundred meters of interior space instead of five hundred).
While these differences may seem small, each amenity can impact effective warehouse management and inventory management. In either case, however, “Class A” designates best-in-class property, and warehousing innovation can happen in a variety of settings.
The first step in choosing a Class A warehouse is asking yourself and your team the right questions and sharing that information with your internal or external commercial real estate team. Here are just a few of the questions to consider:
Your answers will help determine the class of warehouse you truly need and prioritize the features and benefits of each promising property identified in your search.
Agility Logistics Parks designs, engineers, and operates the most advanced international-standard warehousing complexes and light industrial facilities in emerging markets. Our flexible solutions are ready. Contact our team to begin your search for an international-standard, Class A warehouse in the Middle East, Africa, or South Asia.