How Better Warehouses Increase Trade in Africa
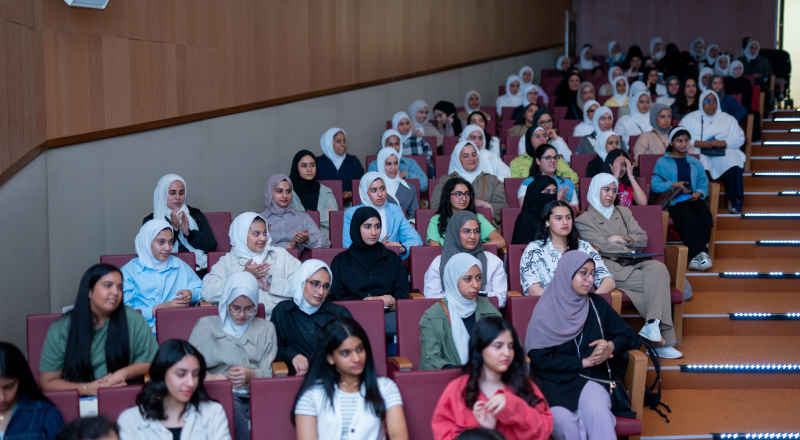
Kuwait-based Agility Logistics Parks customers can log-on to view contracts and make payments.
UK MOD personnel can log-in to the GRMS portal to schedule household relocation shipments.
Kuwait-based Agility Logistics Parks customers can log-on to view contracts and make payments.
UK MOD personnel can log-in to the GRMS portal to schedule household relocation shipments.
One glance at a globe is all you need to see Saudi Arabia’s strategic location in the global supply chain. Situated between Europe, Africa, and Asia, the Kingdom of Saudi Arabia has the potential to develop into a favored logistics hub.
Additionally, Saudi Arabia’s economy is on the rise. With an increasing population and a government set on reducing the country’s dependency on oil, this kingdom in the Middle East expects a steady recovery from the pandemic slowdown. The International Monetary Fund anticipates Saudi Arabia’s non-oil gross domestic product growth to be 3.9 percent in 2021 and 3.6 percent in 2022.
Since announcing Vision 2030 in April 2016, the government has started improving and expanding Saudi Arabia’s logistics infrastructure and capabilities. As a result, any customs broker and freight forwarder doing business in the kingdom can expect more streamlined procedures moving forward.
Additionally, logistics in the Middle East is becoming a freer, more open market with increasing participation from the private sector. For instance, real estate investment trusts (REITs) have recently made significant investments in the Saudi warehousing sector. In 2019, Derayah REIT and Al Mashaar REIT both acquired logistics facilities with multimillion-dollar valuations each (SAR 54.65 million and SAR 129.15 million, respectively).
Infrastructure supporting economic growth in the region continues to develop, and so too does warehousing. However, Saudi Arabia still faces some challenges as an emerging market. Businesses interested in expanding into the area should consider teaming up with a logistics partner with experience in the Kingdom, such as Agility. Offering a full suite of logistics solutions, Agility can help organizations from small companies to multinationals successfully execute and scale their warehousing operations in the Middle East.
As a result of growth in the retail sector, increased manufacturing activity, and expanding international trade, Saudi Arabia’s warehousing needs are growing. The 72 million square meters of warehousing and logistics space in the logistics hubs of Riyadh, King Abdullah Economic City (Jeddah), and Al Khobar (Dammam) are no longer sufficient.
Saudi Arabia’s warehousing challenges go beyond needing space for companies to store dry goods. According to a Research and Markets report, Saudi Arabia’s cold storage market is projected to reach $2.5 billion by 2024.
With this growing demand in mind, forecasters see the warehousing market in Saudi Arabia continuing its upward trend. According to a report by Ken Research, the warehousing market expects a compound annual growth rate increase of 4.1 percent through 2023.
Saudi Arabia, along with the rest of the world, is seeing a rise in e-commerce. The Saudi Gazette reported that e-commerce grew 74 percent during March and April of 2020 alone. This sizzling growth is putting pressure on Saudi Arabia’s warehousing sector to provide more space for online retailers like Namshi and Amazon.
Saudi Arabia needs more state-of-the-art facilities. Businesses in the e-commerce space need modern warehouses so that they can receive, process, and ship product efficiently, accurately, and quickly. The retail sector accounted for half of warehousing revenue in 2018. It’s clear that there is a need for additional warehousing space to accommodate projected growth.
The physical locations of Saudi Arabia’s current warehousing facilities pose another challenge. Most of the nation’s logistics centers are in and around Riyadh, Jeddah, and Dammam. The challenge is heightened by long distances over varied, rugged topography in extreme temperatures as goods are moved between stops along the supply chain.
One challenge that companies face related to warehouse management is finding enough workers to staff facilities. Some logistics providers believe Saudi Arabia lacks the labor force it requires to meet the growing needs of the warehousing sector. As a result, warehouse operators sometimes must find ways to operate their facilities with minimal staff.
As Saudi Arabia strives toward reducing its dependency on oil and opening up the economy, it is working diligently to meet increasing warehouse demands. In 2018, Saudi Arabia opened its economic doors by allowing 100 percent foreign ownership of new start-ups, real estate, and other assets in the kingdom. This is the type of policy change that will continue enticing industrial, retail, and logistics players to participate more heavily in the nation’s economic development.
As the Saudi government and private sector invest in the nation’s economic development, warehousing space is increasing. For example, in July 2018, the Emirati conglomerate Al Futtaim expanded its warehousing facility in Riyadh to 15,000 square meters.
Aside from increasing warehousing space in Saudi logistics hubs, the government is investing in “mega projects,” such as the smart city NEOM and the Red Sea Project. These projects, among others, are creating a demand for more warehouse space outside of the nation’s urban centers. As more warehousing facilities become available in these areas, the distance between stops along the supply chain will shorten, helping freight forwarders to get goods in the hands of consumers more quickly.
Through several key policy changes, the government is striving to create a larger and more capable workforce. According to Reuters, Saudi Arabia wants to create 1.2 million new jobs by 2022.
One of Saudi Arabia’s new policies is the creation of the Human Resource Development Fund (HRDF). The HRDF encourages employers to train Saudis for employment by acting as the middleman in vocational training. This fund reimburses up to 50 percent of the cost for employers to train hired Saudis.
Another policy shift that is helping to grow the workforce is the rise of female participation. According to the International Monetary Fund, the female labor force has risen 13 percent over the past two years. Women now account for 33 percent of Saudi Arabia’s workforce.
Another factor improving the kingdom’s logistics capabilities is increased digitization. As more facets of trade become digitized, customs brokers and freight forwarders are importing, storing, and delivering goods with less delay.
Consumers expect fast delivery times. To help achieve this, warehouse management must invest in a digital warehouse management system, which can help optimize and manage the day-to-day operational flow of a warehouse.
This software can help warehouse staff quickly receive and put away inventory, as well as pick, pack, and ship inventory per order specifications with high efficiency and accuracy. Further, it notifies warehouse management when inventory needs replenishing so that the warehouse is always stocked and ready to fulfill orders at any demand.
With the warehousing sector becoming more digitized, its capacity for automation blossoms. And the benefits of greater warehouse automation are multiple. For one, a warehouse can operate with fewer staff, which aids warehouse operators in a region where sufficient skilled, low-skilled and unskilled labor may be difficult to find.
Automation also decreases the workload of the human workforce. Repetitive jobs like unloading and sorting can be physically demanding. The tedious nature of such work can physically and mentally wear down staff and increase the possibility of human error.
Automating these tasks can improve staff longevity, minimize or eliminate human error, and free staff to concentrate on more high-value work for the warehouse. Since the best automation systems can even integrate with a facility’s materials handling equipment, burnout is more avoidable while the facility itself creates consistent productivity.
Despite moving toward greater automation, any warehouse will still require staff to ensure smooth facility operations—automation does not replace human ingenuity and critical thinking.
The Internet of Things (IoT). After increasing automation in the warehousing sector, the next step is incorporating IoT into the warehouse workflow. IoT technology enables advanced tracking and high traceability along the supply chain.
IoT devices powered by fifth-generation mobile technology and embedded into shipments capture and transmit a high volume of various data. Anyone from the manufacturer to the consumer can access this data from anywhere in the world in real time.
Inventory embedded with IoT chips is more visible at any point along the supply chain. Data captured from the chips can show where inventory is at any moment, as well as its condition. And the data can also alert stakeholders of shipment delays from accidents, detours, and unplanned stops.
As Saudi Arabia’s warehouse economy expands and evolves, warehouse operators must systematically manage the ways their facilities change. To do that, it is beneficial to first consider the key drivers compelling change management.
These drivers are forcing change throughout the warehousing sector.
As Saudi Arabia moves forward with technology, customers are putting more pressure on retailers to provide fast and efficient service. According to the General Authority for Statistics, in 2018, Saudis used their cell phones for six hours and forty-five minutes per day on average—fifteen minutes more than Americans. This suggests that Saudi Arabia’s citizens are plugged in and eager to conduct transactions or do business via mobile devices.
With so many Saudis online and with omnichannel networks becoming more necessary, this puts pressure on warehouses to function at optimal efficiency. In some cases, this means the consumer now has access to inventory data, which means that it is increasingly difficult for warehouse operators to be even one step ahead.
With warehousing advancements moving well beyond conveyor belts and forklifts, warehouse operators will need to implement change using a calculated and strategic approach. Clear communication has always been a factor in the success of any business. And the warehousing sector in Saudi Arabia is no different.
As processes change and as more advanced technology is in use in warehouse facilities, clear communication between managers and staff will continue to be necessary. And warehouse management should plan ahead to ensure staff are properly and adequately trained on all new devices and systems that find homes in warehouse facilities.
Through its shifts in policy and embrace of technological advances, Saudi Arabia is positioning itself to become a regional logistics hub outlined in Vision 2030. Any business looking to participate in this economic growth may want to take advantage of the intimate knowledge that comes from a logistics partner like Agility who is familiar with the region.