By understanding how green warehouse practices reduce cost, modern companies reap the benefits of improved bottom lines while boosting their corporate image.
Going green proves to stakeholders that a company values sustainability and cares about the larger world outside the corporate conference room. Indeed, research shows that such initiatives are vital to global health now and in the future. And with the right green warehouse practices, the benefit becomes twofold by leading to cost savings as well.
This article covers the cost-effective, competitive advantages of a green warehouse. Discover which green warehouse practices will save you the most money and how to implement them.
Gaining a cost-effective, competitive advantage through a sustainable green warehouse
Going green provides a competitive advantage, especially considering public interest in green initiatives. Suppose a prospective customer is choosing whether to buy from a company that implements sustainable practices or one that does not. A majority of studies show that all other factors being equal, consumers are more likely to choose the greener option.
Implementing green practices can also lead to cost savings because many green practices center on improving efficiency and reducing waste. Multiple supply chain leaders have achieved significant savings by adopting green practices. For example, Amazon’s data centers run entirely on renewable energy, which costs the company an estimated 10 percent less than using fossil fuel energy.
How supply chain leaders can incorporate green practices while maintaining profit margins
Now more than ever, supply chain leaders consider sustainability efforts to be critically important. In a 2017 survey by EcoVadis and the HEC Paris business school, 97 percent of procurement officers named sustainability as one of their top five priorities. In addition, 75 percent of companies in the survey reported that they took environmental sustainability and social responsibility into account when selecting new suppliers.
Agility, which builds a number of green features into its warehouses, has also invested in a number of sustainable innovation companies. One is Hyliion, which is developing an electrified powertrain system for Class 8 commercial trucks. The Hypertruck Electric Range Extender (ERX) is a long-haul, fully electric powertrain that will improve vehicle performance, reduce emissions and save on operational costs.
Supply chain leaders also implement supply chain assessments to identify inefficiencies and ways to reduce waste and expense. This leads to cost savings by improving visibility into the supply chain and identifying opportunities for more efficient logistics solutions. Assessments can also pinpoint opportunities for improving environmental impact, such as implementing green procurement systems.
The right technologies and modeling tools also enable higher efficiency and allow companies to optimize their warehouse practices to improve their profit margin. For example, Agility has a route-modeling tool that enables specialists to work with a nearly infinite number of variables and combinations. These include routes, schedules, inventory requirements, shipping modes, packing density, load configuration, and more. From this data, specialists can model various supply chain strategies and identify ways to optimize their shipping practices, as well as other steps in their supply chains.
How a green warehouse saves you money
Green practices often involve finding ways to improve efficiency through an optimized supply chain, which often benefits not only the environment but also a company’s bottom line. For example, when General Motors established a reusable container program with its suppliers, it reduced disposal costs by $12 million.
The following are some simple examples of how cost savings come about from green practices:
-
Decrease fossil fuel use:
Using less fossil fuel leads to cost savings, as long as you don’t accomplish this reduction by spending more on electric transportation or other methods. Practices such as consolidating orders into fewer shipments or optimizing shipping routes, for example, save fuel and fuel costs without requiring you to spend the savings elsewhere. -
Reduce hazardous materials use:
Many chemicals and other materials may be hazardous to humans or the environment. By minimizing reliance on these materials, such as solvents and paint, you save on costs associated with their handling and disposal. -
Use recyclable or reusable packing materials:
Although reusable packing materials may have a higher up-front cost, the ability to reuse them leads to savings in the long run. Recyclable packing materials or materials made from recycled products may be less expensive. -
Use technology to reduce waste:
Technologies such as robotic process automation or warehouse management tools lead to fewer mistakes, conserve time and energy, increase process efficiency, and reduce waste overall.
Saving money on operations through green warehouse practices
Warehouse storage can be expensive. Many of the reasons for high costs have their origins in practices that aren’t green. High energy usage, inefficient storage practices, and warehouse processes that result in waste cost money and hurt the environment.
Reducing these inefficiencies and sources of waste can make your warehouse practices greener and more cost effective.
Green warehouse practices
Companies can implement many practices within the warehouse environment that increase efficiency, save money, and promote sustainability. The following are some of the more common green warehouse practices:
-
Storage optimization:
Store products in a way that minimizes the total floor space you need for them. Also, consider stacking products on pallets that forklifts can easily handle and move to minimize any expenditures associated with moving these items. -
Inventory control:
Make sure to properly package, label, and store inventory. This minimizes damage, which saves you money while decreasing how much you send to the landfill. -
Cross-docking:
By transferring products directly from the supplier truck to the delivery vehicle bound for the customer, you use fewer resources in the warehouse. -
Recycling and reusing:
Reusing pallets and storage materials when possible saves money and helps the environment. Recycling old materials keeps them out of the landfill and saves on disposal fees. -
Energy-saving practices:
Increasing warehouse insulation, using energy-efficient or natural lighting, and automating lighting can reduce energy costs. -
Warehouse management:
Warehouse management systems (WMS) automate and streamline many processes within the warehouse, reducing expense and waste. For example, WMS can record inventory locations, direct employees where to store items, and calculate the most efficient sequence for picking items. Warehouse management software also facilitates shipping to customers from the closest warehouse, minimizing transportation use.
Benefits of improved resource efficiency
Practices that take place in the warehouse often impact and reflect practices throughout the larger supply chain. Therefore, improvements in warehouse operation often lead to improvements in shipping, handling, order management, and more.
Many of these green warehouse practices fall under the category of improving resource efficiency. In other words, the goal is to obtain the maximum useful work with the minimum amount of resources. Those resources may be human workers, energy usage, storage space, time, transportation, packaging, and so on.
For example, suppose a company plans to warehouse one hundred cubic feet of product. The warehouse needs to receive the product from the manufacturer, store the product, and then ship it to customers when they place an order.
However, this total volume is slightly over the maximum for a single forty-eight-inch by forty-inch pallet. If the company decides instead to ship ninety cubic feet at once, it can stack the product on a single pallet and improve resource efficiency. The company can then wait until demand calls for another ninety cubic feet of the product before it ships more to the warehouse. This minimizes storage space, as well as shipping and handling resources.
Cost efficiency of flexible warehousing
With the fast pace of today’s economy, many companies find that flexible warehousing solutions better meet their needs. Flexible warehousing is a warehousing strategy that enables companies to scale their warehouse space up and down by storing inventory in shared warehouse spaces on an as-needed basis. This also includes changing warehousing locations to meet customer demand.
What makes flexible warehousing green is that it only uses the necessary resources rather than securing space that goes unused. It’s also extremely cost effective because companies only pay for the space they’re using instead of reserving the maximum space they may need at all times.
Some warehousing providers specialize in providing flexible warehousing space, not by owning any actual real estate themselves, but by providing companies with open space in warehouses.
Often, 3PL providers bring the most efficient, cost-effective, and green solutions because they come with industry expertise, as well as optimal infrastructure. By handling the warehousing needs of multiple companies at once, they can strategically manage storage of all types, often with the help of industry-leading warehouse management software.
Determining the most cost-effective green warehouse practices
With so many different green techniques on the rise, how can companies determine the most cost-effective green warehouse practices? Fortunately, emerging technologies can provide data and models to predict the financial impact of adopting green practices. In addition, there are a wide variety of case studies that can help companies see what has worked well in similar industries.
Best practices for green warehousing
The first step in determining which practices will prove most cost effective requires using data and technology. The right technology and tools allow companies to estimate the environmental impact of new practices, as well as the associated increase or decrease to overall costs.
For example, Agility has a carbon measurement tool, which allows its customers to accurately offset estimated CO2 emissions. Since 2009, Agility has been providing customers with free carbon footprint reports that enable them to track and reduce the amount of emissions created in their supply chains.
Reducing carbon emissions often goes hand in hand with decreasing costs. Green practices typically involve cost-efficient measures such as using renewable energy, reusing resources, and cutting down on packaging materials.
Tools like warehouse management software make it easier for companies to manage and optimize their warehouse processes. Companies can also take advantage of other technology tools that automate packaging, handle procedures that reduce waste, and increase efficiency in a host of other ways.
Best green ways to reduce warehouse costs
Cost-effective green warehouse techniques aren’t one-size-fits-all; the best methods can vary based on factors like a company’s product and the target market. To decide on the best green methods for reducing your warehouse costs, it can be helpful to study how similar companies have found success in implementing green practices.
The following are some examples of practices that have helped companies realize significant cost savings: A sports apparel brand in Indonesia and the Philippines realized $2.2 million in savings by collapsing and stacking unused boxes for future use.
A Chilean retail company saw cost savings by using tracking technology. Purchase order visibility and real-time reports enabled proactive vendor contact and tracking, as well as improvements to processing efficiency.
Working with Agility helped a major electronics company meet a tight timeline by selecting a strategically located 14,500-square-meter facility in Algeria. By working with industry experts, the company procured all the necessary equipment, tools, and systems efficiently, minimizing waste and sales losses.
A global telecommunications provider created a goods-in-transit center that reduces air cargo weight, transport costs, and carbon emissions on shipments from mainland China and Hong Kong to India.
In general, following green packaging practices and using green packaging materials can help companies reduce costs while remaining environmentally friendly and reducing waste.
Inexpensively implementing green warehouse practices
Some companies avoid implementing green warehouse practices because they fear the cost of doing so. Even though companies may realize cost savings once those practices are in place, the problem lies in the up-front expenses companies must pay to change current practices.
For example, if a company decides to use reusable shipping containers, the new containers’ up-front cost might far exceed the cost of disposable ones. Even though it saves money in the long term, the opportunity cost may dissuade some supply chain managers.
However, by starting with simple steps that reduce waste and increase efficiency, it’s possible to realize long-term cost savings even with a small initial investment. Afterward, you can apply those saved funds toward other green measures with higher opportunity costs.
Tips for transitioning to green warehouse practices
Adopting green warehouse practices doesn’t have to happen all at once and doesn’t need to be an overwhelming proposition. Below are some simple tips that you can implement over time to transition to more sustainable practices:
-
Start small with recycling:
Make it a practice to send used packaging materials to a recycling center instead of the landfill. Work with a battery recycler to safely dispose of worn forklift batteries or other similar materials. -
Upgrade warehouse equipment with sustainable alternatives:
As older equipment wears out, replace it with new products that have lower energy requirements and maintenance needs. For example, choose electric forklifts and pallet jacks, as well as eco-friendly conveyor systems. -
Make lighting modifications:
Installing an energy management system for warehouse lighting allows you to only use lighting when needed. Replacing older bulbs and fixtures with newer energy-efficient LED fixtures can significantly reduce energy use and save money. -
Consider warehouse layout:
A poorly laid out warehouse can reduce efficiency. Look at the process for unloading, storing, and processing products. Identify ways to make the transitions as smooth as possible, without the need for continually rearranging pallets or moving materials across the warehouse floor. -
Consider warehouse locations:
A green warehouse is part of a larger green supply chain. Most of the total supply chain carbon footprint comes from moving items to and from warehouse locations and consumers. Strategically optimizing warehouse locations, storing products as close as possible to large customer centers, and optimizing shipping routes will cut emissions and costs. -
Consider other warehouse systems:
This includes everything from your heating, ventilation, and air-conditioning (HVAC) system to your choices for insulation and roofing. Improving insulation reduces heat transfer and saves on expenses related to heating and air-conditioning. A more energy-efficient HVAC system reduces usage and costs. And when it’s time to replace the roof, choose one that is bright and reflective. -
Transition to eco-friendly packaging:
Many options are available on the market, allowing companies to implement green packaging practices that meet their needs. This includes packaging made from recycled paper, mushrooms, cornstarch, organic fabric, and bamboo. These packaging materials are often inexpensive to produce and lightweight, which can reduce shipping emissions and expenses.
Inefficiencies to eliminate to make your warehouse green while on a budget
Making your warehouse green while on a budget requires careful planning. To begin, look over your entire supply chain management process to identify inefficiencies you can easily eliminate to the benefit of the environment, as well as your bottom line.
These inefficiencies may include things like the following:
-
Workflow disorganization:
Follow the path a product takes from manufacturer to warehouse/distribution center to consumer. Identify any hiccups along the way, such as delays in transfer, storage times that are longer than needed, or problems with order processing. Remedying the situation may only require simple process changes at no additional cost to you. -
Lack of carrier mode diversification:
Seek to continually build relationships with different carriers, and get quotes for other carrier mode options. By sticking with what you’ve always used before, you might be missing out on less expensive (and more environmentally friendly) options. -
Lack of proper demand forecasting:
By not having accurate estimates of consumer demands, it’s difficult to strategically and efficiently stock products in the right warehouse locations. This leads to using more space than needed, as well as extra transportation expenses. A small investment in quality forecasting software can lead to a significant payoff in the end. -
Excess packaging usage:
Examine your packaging usage and practices. You need to use enough packing materials to keep products safe during storage and transport, but overuse is simply waste. Identify ways to refine and optimize the use of packaging materials.
Eliminating inefficiencies often costs little except the time it takes to identify them and implement new practices. As a result, you might begin realizing cost savings immediately, and the environment will thank you as well.
Reducing costs and improving sustainability with Agility
The two key ways that a green warehouse provides a competitive advantage are by improving company image and decreasing expenses. Anytime you can accomplish the same objectives at a lower cost without reducing quality or other metrics, it’s in your best interest to do so.
One of the most efficient ways to implement green warehouse practices while reducing costs is to partner with a third-party logistics provider along with a world-class warehouse operator like Agility. Not only does Agility offer scalable warehousing and distribution capabilities worldwide, but it is actively working to build a greener and more equitable supply chain.
Agility has implemented multiple ongoing efforts to reduce hidden environmental and social costs associated with supply chain logistics. Independent sustainability analyst EcoVadis ranks in the top 5 percent industry-wide for environmentally friendly practices.
By partnering with Agility for your warehouse or supply chain solutions, you are working with an industry leader that actively engages in sustainability efforts to support the environment. Contact Agility’s warehousing team today to learn how it can help you save money while minimizing your impact on the environment.
As the field of logistics changes, many organizations need to address the factors affecting warehousing efficiency in order to prepare for the future.
Supply Chain reports that UK warehouses lose nearly three thousand hours every year, thanks to inefficient processes—especially when it comes to inventory control, packing, unloading, and picking. In the US, inventory management challenges like stockpiles of unsold goods hinder warehouse efficiency. And global organizations with underperforming supply chains struggle to achieve profitability, calling for a need to optimize everything from distribution to warehousing. The good news: according to Deloitte, 79 percent of companies with superior supply chains attain revenue growth that’s far above average.
Why is warehouse efficiency more important than ever? Because the increased demands of e-commerce are currently straining warehouse operations. According to eMarketer, retail e-commerce sales grew 27.6 percent in 2020, and they’re set to grow another 14.3 percent in 2021. That leaves warehouses scrambling to keep up, and searching for ways to boost efficiency as a critical way to gain some ground. As a leader in supply chain optimization, Agility offers warehousing solutions designed to reduce costs and improve efficiency. In this article, we’ll delve into the most common factors that lead to warehouse inefficiency and how to solve them.
How warehouse layout affects efficiency
Logistics Management notes that just 11 percent of the total warehouse space in the US appeared in the last decade, meaning many warehouses are out of date. In fact, warehouses typically become obsolete within thirty-four years—a problem, considering that nearly one billion square feet of warehouse space is more than half a century old. These challenges mean many warehouses aren’t properly equipped to handle the increased demands of e-commerce. Common problems include low ceilings, not enough loading docks, or uneven floors that slow down warehouse staff.
Fortunately, it’s possible to modernize and expand warehouses to accommodate changing needs. And just as importantly, you can and should regularly update your warehouse layout to increase efficiency. Even if it’s not possible to invest in raising your warehouse roof or adding more square footage, making the best use of the space you do have can address workflow problems.
How can layout impact performance?
Flaws in your warehouse layout can lead to efficiency and performance problems, such as the following:
- This is when delays in one small area of your warehouse lead to a much larger holdup down the line. For instance, warehouses that do not organize goods efficiently often experience shipping bottlenecks, since picking ends up taking too long to keep up with the flow of incoming orders. Warehouses with inefficiently located receiving bays may see bottlenecks when it comes to stocking goods. Sure, a variety of factors can cause bottlenecking, but making changes to your layout often helps get things moving.
-
Redundant movements and activities.
When warehouse layout isn’t optimal, workers can waste hours of time over the course of a week. For instance, they may need to move pallets from a receiving dock on one side of the warehouse to a storage location on the other side of the facility: not the most efficient arrangement. In some cases, workers may end up making repeat trips or moving goods to one area, only to have to move them to another area, later. Optimizing worker paths—and changing your warehouse layout to support that—can help reduce wasted effort. -
Low picking metrics.
Suboptimal warehouse layout tends to make it hard for workers to pick a high number of units per hour (UPH). This leads to wasted time and money, not to mention shipping bottlenecks and ultimately, customer dissatisfaction. Redesigning your warehouse to enable the most efficient picking paths can address this issue, improving both worker performance and customer satisfaction. -
Heating and cooling inefficiency.
Some products in your warehouse may need refrigeration or have other temperature control needs. Storing these goods can result in high energy costs, which could have an impact on your bottom line. Fortunately, it’s possible to optimize your warehouse in order to house refrigerated goods in a separate, preferably insulated storage area. This ensures you aren’t cooling the rest of the warehouse unnecessarily or making refrigerators work too hard. -
Safety and security concerns.
If the flow of workers and goods through your warehouse isn’t efficient, or there isn’t enough space to maneuver equipment safely, accidents, injuries, and product breakage can occur. These issues aren’t just detrimental to warehouse efficiency and profit. They could cause serious harm to your workers. In addition, not having secure areas of the warehouse to store high-value goods like jewelry and electronics can lead to theft.
What about your warehouse layout could be hurting process efficiency
Look for common warehouse design problems, such as the following:
-
Insufficient space for deliveries
Using the same docks for loading and unloading goods—or docks located too close together—can lead to inefficiencies and hold up your shipping schedule. For instance, if deliveries overlap with loading and dispatching a truck, workers will struggle to share the space. This can lead to lost time, at best, and accidents or injuries, at worst. -
No clear picking paths
A big goal of warehouse design is to optimize pickers’ work. That means storing products in such a way that pickers can take the shortest possible paths. In general, picking paths should minimize backtracking, and products should be clearly labeled so they’re easy to find. Additionally, picking paths should wrap up near the packing area. After all, it doesn’t make sense for pickers to make their way across the warehouse, only to have to walk back to where they started after picking the order. -
Too many dead-end aisles
Good warehouse design optimizes the flow of goods and workers. Dead-end aisles require pickers—and forklifts—to execute turns and go back the way they came, leading to wasted movements and even traffic jams. This is not only inefficient but can violate safety codes. -
Not enough maneuverability
Moving large objects requires ample space, whereas tighter areas may be fine for storing smaller, lighter objects. When planning your warehouse layout, it’s critical to consider the handling needs for each type of product you stock. Remember that if a forklift has difficulty accessing larger or heavier objects, or if it has problems turning, it could collide with racks or stacks. This could lead to breakage and injuries. -
A shortage of overflow space
When unexpected needs and opportunities arise, it’s important to have some extra space. For instance, maybe your organization got a bulk discount on a product and ordered more than usual. Or maybe you’re piloting a new product that requires assembly at the warehouse. Whatever it is, overflow space will ensure you have room to get it done. And sometimes, warehouses have more room than they think. Cleaning out clutter or getting rid of obsolete inventory may free up the overflow space you’re looking for—whether you need a staging area or temporary storage. -
Insufficient waymarks
Helping warehouse workers safely navigate your facility is a critical consideration. After all, even the best layout isn’t always intuitive. Color-coding the warehouse floor helps with orientation, and clearly marking each aisle with a number can improve efficiency at every step. Keep in mind that sometimes it’s not possible to remove an obstruction to traffic flow. Structural columns are one such example. In this case, using brightly colored column protectors is key to preventing collisions and protecting columns from damage.
How do you lay out a warehouse efficiently?
Designing an efficient warehouse layout requires you to understand your inventory: it’s size, weight, popularity, and storage needs. This way, you can store products in configurations that make the most sense for your business. And if you’re redesigning the layout of your existing warehouse, it’s also helpful to know how your staff works. Do they tend to experience traffic jams in certain parts of the warehouse? Are they taking longer than they should to pick an order? From there, use the following considerations to lay out your warehouse for optimal efficiency:
-
Establish proper zoning
Zoning enables warehouse workers to store and pick products via the most efficient routes. As an example, storing bulky goods together in extra-wide aisles makes more sense than storing large and small items in the same aisles. For one, larger or heavier goods may have different logistical considerations. For two, these goods may need reinforced shelving, which tends to be costlier than standard shelving. Why waste those units on lightweight goods? -
Store popular items in the same place
This helps workers pick orders in less time—especially if most orders tend to contain several different popular products. Of course, your best sellers may change over time. It’s important to keep tabs on what these items are and rotate products in and out of your designated prime real estate zone. To achieve this, keep track of stock keeping unit (SKU) velocity. SKU velocity refers to the quantity and frequency of each SKU picked over a certain period of time, and it can help you determine how to sort products for the fastest order fulfillment. -
Maximize traffic flow
When workers can move quickly and easily through the warehouse, they save thousands of hours every year. In addition, your warehouse should see fewer bottlenecks and injuries, and less broken equipment or damaged products. To achieve this, plan your warehouse to maximize one-way traffic, avoid sharp turns and narrow aisles, and keep the floor clear and uncluttered.
-
-
Design for flexibility
An open warehouse layout enables you to make changes easily. In contrast, a warehouse that features too many fixed spaces can make it hard to switch up the layout as your inventory changes. If you have the option, make use of temporary, moveable partitions to divide up space. A key principle of warehouse layout design is that needs change fast. Keeping your space as flexible as possible is a great way to future-proof your warehouse.
-
How work methodology affects warehouse efficiency
It all starts with the work methodology
When warehouse workers don’t use optimal methods for moving, storing, or picking goods, this tends to result in low key performance indicators (KPIs) throughout your operations:
-
Receiving efficiency
This is the volume of goods each warehouse worker receives per hour. When warehouse operators use inefficient work methodology, expect receiving efficiency to be lower than your target, leading to higher costs. -
Put-away productivity
This KPI looks at the volume of goods each worker puts away per hour. You can also look at put-away accuracy, which could reveal inefficiencies when it comes to handling new inventory. Tracking this metric by individual worker can help you get to the root of the issue. -
Picking productivity
This is the number of order lines picked per hour. In addition, you should look at picking accuracy. Problems with these KPIs could indicate quality control issues, suboptimal picking paths, and the need to retrain workers. -
Perfect order rate
This is the total number of orders delivered without issues. Needless to say, problems with picking accuracy or efficiency issues that cause shipping delays can prevent your perfect order rate from hitting target.
Work methodologies that improve warehouse efficiency
The following methods could help your staff work smarter and boost overall warehouse efficiency:
-
-
Pick to light
Pick-to-light systems and put-to-light systems use indicator lights to help workers find or correctly place items. This speeds up the process of picking or putting away, since workers don’t have to search for the right location. And when synced with your warehouse management system (WMS) and enterprise resource planning tool (ERP), this solution makes it easy to keep tabs on your inventory. -
Cross docking
How fast do incoming products move out the door? If some goods are especially fast moving, shelving them upon arrival may not be efficient. Instead, move them to a staging area for pickers to find easily. Known as cross docking, this method enables quick retrieval, so workers don’t have to waste time shelving popular items only to have to pick them minutes or hours later.
-
-
Achieving quicker travel times
Pickers may need coaching on the fastest way to move from point A to point B. For instance, you could challenge workers to avoid backtracking by mapping the most efficient route through the warehouse before starting each order. In addition, it helps to inform everybody of any new changes to the warehouse layout, to minimize time spent wandering. -
Improving pick list accuracy
If out-of-stock items make it to pick lists, pickers could waste time searching for unavailable inventory. That’s why it’s so important to use an inventory management system and ensure all available data is as accurate as possible. -
Batch and cluster order picking
Batch order picking is when workers pick the same SKUs for several orders at the same time. This reduces travel time, since pickers can grab multiples of the same item at once. Cluster order picking is when pickers work on several orders at the same time—even if they don’t share SKUs in common. Why? Because it cuts down on overall travel time and prevents pickers from having to retrace their steps to and from the packing area with every order. -
Pick and pass
Also known as zone order picking, this method assigns workers to designated zones. They then pick SKUs from their zones, place them in bins, and pass them on to the next zone. With this strategy, picking the order is a true team effort. Plus, picking and passing is ideal for warehouses that have problems with worker congestion. -
Keeping SKUs together
If you have many similar items—like different-colored T-shirts in the same style—it makes sense to shelve these products next to each other. But avoid mixing SKUs. This creates confusion, wastes time during picking, and can lead to accuracy issues. -
Know your fastest pickers
Not every worker can pick at the same speed, and that’s OK. But acknowledging, rewarding, and studying your fastest pickers to learn their techniques is a great strategy. You can even have new or slower workers shadow your top performers to pick up tips. -
Active management
If worker productivity is low, this could be due to insufficient structure in the workday or unclear expectations, overall. It’s critical to allocate tasks and measure performance to keep workers on track. During downtime, assign tasks that can promote overall warehouse efficiency, like removing dead inventory or tidying staging areas.
How to evaluate the efficacy of your work methodology
To know if changes to your work methodology are getting results, you need to set benchmarks for your team and measure their performance against your expectations. It’s as simple as that. Using a WMS with radio frequency (RF) that can capture data makes it easy to track worker metrics, such as UPH, or organizational KPIs, such as perfect order rate. When making major changes to your team’s work methodology, try introducing one change at a time and tracking the results to see if there’s an improvement before introducing another change. If you overhaul everything at once, it’s hard to tell what’s working and what’s not.
How inventory affects warehouse efficiency
Warehouse inventory management is the system and set of processes used to organize and track the goods in your warehouse. Proper inventory management uses principles of facility and process engineering along with technology to improve inventory accuracy and visibility. Without a clear picture of your inventory, it’s difficult for staff to find and access stock, pick orders efficiently, and achieve a high perfect order rate. With a sound inventory management strategy, you’ll not only enable your team to improve their productivity, but you’ll save on the costs of labor, reduce error, and ultimately, increase customer satisfaction.
How does inventory turnover affect your warehouse efficiencies?
Not having enough inventory on hand can lead to order fulfillment delays and dissatisfied customers. On the other hand, having too much inventory that doesn’t turn over can lead to an excess of dead inventory, such as seasonal or expired goods you can’t sell. That can take a bite out of your profits—and take up valuable space in your warehouse. The following techniques can help you stay on top of your inventory and boost efficiency:
-
Use ABC analysis
This technique breaks goods down into three categories: A, B, and C. Category A includes the top 20 percent of your inventory, consisting of the best sellers that account for 80 percent of your revenue. Category B features the middle 30 percent of your inventory, which represents 15 percent of your revenue. And Category C consists of the bottom 50 percent of your inventory, or 5 percent of your revenue. By accurately sorting your inventory, you can store products more strategically, forecast demand, and ensure you never run out of your top products. -
Maintain economic order quantity (EOQ)
This is the ideal number of units your warehouse should order to minimize overall inventory costs related to factors such as order costs, holding, and shortage. You can calculate this by multiplying total order cost by annual demand, multiplying by two, and dividing by holding costs. Then, find the square root of that number to arrive at your EOQ. Keep in mind that this approach isn’t ideal for every business. If you typically see dramatic seasonal fluctuations in demand, you’ll need a more flexible ordering strategy. -
Try the just-in-time (JIT) inventory method
The JIT technique involves manufacturing or acquiring items right before you need them. Inventory moves quickly and doesn’t require as much warehouse space. Plus, this method eliminates the risk of overordering, which can leave companies with dead stock on hand.
How can you evaluate your current method of tracking warehouse inventory?
Many methods exist for tracking warehouse inventory—from sophisticated WMS with RF identification to universal product code scanning to a pencil and paper. To find out if your method is working for you, consider the following KPIs:
-
Inventory turnover
The higher the turnover, the better. If inventory sits too long in your warehouse, you’re losing money. -
Stock outs
Poor demand forecasting and inventory planning can lead you to run out of stock at inconvenient times. -
Lost sales
This is the number of opportunities lost during a stock out. -
Order cycle time
This is the amount of time starting when a customer places an order and ending when they receive the order. Inventory management issues could lead to a longer order cycle time and dissatisfied customers.
Today, warehouse automation can take a lot of the guesswork out of inventory management and demand forecasting. This technology also reduces the need for manual labor, eliminates human error, and can help you optimize your inventory to avoid waste or lost opportunities.
How to evaluate your warehouse’s efficiency
These tips can help you measure the efficiency of your warehouse operation and identify areas that need improvement:
-
Use tracking technology
A good WMS offers insights into your operations and team, including the health of your inventory, worker performance, and overall warehouse productivity. A WMS can also help with labor forecasting and inventory demand forecasting. It’s a great way to identify and fix inefficiencies throughout your warehouse. -
Talk to your workers
They’ll be able to tell you what pain points hold them back, and the answers may surprise you. For example, warehouses that feature conveyor belts designed to make certain tasks easier often find that workers get impatient with their slow speed. And if your warehouse layout needs reconfiguring, your pickers can likely tell you what needs to change. -
Observe your warehouse in action
Shadowing an employee will give you a chance to see whether your warehouse runs like a well-oiled machine. It’s the easiest way to find out if problems such as congested areas of the warehouse, receiving bottlenecks, or improperly slotted inventory are holding up your operations. -
Conduct regular warehouse audits
During an audit, you’ll look at everything from your warehouse’s capacity, layout, and storage systems to safety protocols and customer service performance metrics. By proactively and regularly auditing your operations, you’ll be able to identify and fix problems before they have a chance to get serious.
What is the best way to start improving warehouse efficiency?
To boost warehouse efficiency, you first need to isolate which factors need improvement. And that calls for some detective work. For instance, say your pickers’ average UPH is too low. This could be due to warehouse layout issues causing workers to retrace their steps or walk too far to complete an order. It could be because some of your pickers need coaching on the right techniques. Or maybe your warehouse could benefit from rezoning to make the most popular inventory easier to find. Accurately identifying the problem is half the battle, and it’s that much easier to improve your KPIs when you know what processes need fixing.
What is green warehousing? And why is it important in the modern business climate? As the Information Age advances and as Earth continues to suffer the effects of climate change, well-informed consumers demand environmental and social responsibility from businesses, including green warehousing.
Sustainability in business—demonstrated by companies that operate with concern for natural and human resources—can mean increased customer loyalty. Incorporating green logistics into warehousing as part of the supply chain can also yield better business productivity and improve a business’s bottom line.
Applying green trends in warehousing offers nearly immediate return on investment (ROI) plus longer-term global improvements while satisfying stakeholders’ desires.
Today’s green warehousing practices
As warehouse managers consider green warehousing in today’s business climate, they need to know how to measure results and where to find available, effective products and practices.
Key performance indicators in green warehousing
In global supply chains, warehouses produce environmental pollution mostly from heating, cooling, and lighting. Generally, the bigger the warehouse, the larger the carbon footprint. Warehouse managers can measure the carbon footprint of their operations by considering key performance indicators: emissions, natural resource use, and amount of waste and recycling.
Studying total carbon dioxide emissions, as well as energy consumption, water consumption, and rate of product or material use, will reveal areas where companies can apply green initiatives.
For example, a warehouse with a high electricity bill might discover that alternative lighting sources—like natural light, automatic lights, or other renewable energy options—offer savings. Likewise, the discovery that a warehouse consumes large quantities of water from a natural source might inspire change. By installing water flow reduction mechanisms or a rainwater capture system, warehouses can reduce, offset, or optimize water use.
Green warehousing technologies and products available today
After assessing their warehouses to identify logistics solutions for environmental sustainability, businesses have various green warehousing products to consider that will promote sustainable logistics:
- A warehouse management system (WMS)
- Order-picking technology
- Bar coding
- Radio frequency identification (RFID)
A WMS allows for the digital coordination of stores, distribution centers, and warehouses while coordinating shipping and transportation. Better inventory control through a WMS means green warehouses can operate with the ideal amount of product, thereby reducing excess inventory and maximizing storage space.
Technology to enhance order picking through automation or digitizing can increase accuracy and speed up warehouse orders. Order-picking technology has the added benefit of reducing paper consumption.
Also reducing the need for paper are the sustainable distribution practices of bar coding and RFID. These technologies improve processes and increase the visibility of goods throughout the supply chain.
Additional sustainable products include skylights to let in natural light, ceiling fans to control warehouse temperature, energy-efficient lights and fixtures, green building materials, and building insulation. Eco-friendly warehouses reduce waste, another important principle of sustainable business.
Challenges facing green logistics today
Implementing green initiatives along the supply chain is difficult. But with the right tools and management practices, companies can confront any number of challenges:
- The vastness of the global supply chain: Supply chain logistics covers a wide range of shipping types, routes, sizes, configurations, and more. Lessening environmental impact across the entire network can be challenging.
- Fewer green solutions for warehousing: Compared to other parts of the supply chain, such as transportation, fewer green solutions exist for warehousing. Yet many of the available solutions prove effective, and the number of solutions is growing.
- The up-front costs of green warehousing solutions: These costs might prevent some operations from converting. However, the initial investment for green logistics often pays off with time.
Even if the path to green warehousing presents challenges, companies wanting to stand out from their competitors can prioritize sustainability to make a difference in the world and in their accounts.
Effectiveness of green warehousing
In a global market, businesses need to stand out from their competitors. Success hinges on providing consumers with what they want: companies that go green in all aspects of their operations. A green supply chain satisfies stakeholders’ desires while positively impacting operations and finances.
Green warehousing for the bottom line
Thanks to the digital proliferation of information, customers know the environmental impact of their buying habits. Those who want to reduce their carbon footprint seek out companies that prioritize green initiatives, from raw material source to warehouse to packaging to transportation. Conscientious consumers are willing to pay more for green products and services.
Businesses gain a competitive advantage by reducing environmental impact through supply chain management, including through green distribution. And publicizing details of these sustainable practices—such as using solar panels or green building materials—creates customer loyalty because the buyer perceives the company as environmentally responsible.
Benefits of moving to a green economy
Green logistics plays an important part in a larger undertaking: to move the world toward a green economy. A green economy focuses on low carbon emission, is efficient with resources, and is socially inclusive.
Benefits of a green economy include reduced pollution, enhanced efficiency of energy and resources, a slowdown in the loss of biodiversity, and preservation of the services that the ecosystem provides.
A successful green economy allows economic growth and improves people’s ability to coexist with nature. Economic growth might move slowly at first, but the benefits play out in the long run. Lasting benefits of sustainable development include reducing the risks associated with climate change, energy shocks, and water scarcity.
Green practices can also reduce poverty and help developing countries via new export opportunities. Businesses that embrace responsible supply chain practices stage themselves for success in emerging markets.
Results of a greener warehouse on a company’s ROI
Although the benefits of green warehousing might seem intangible or too far off, supply chain managers who invest in going green see a fast ROI.
Energy-efficiency measures, such as switching lighting sources to reduce electricity consumption, have a quick payoff. Installing a WMS could deliver an ROI in a matter of months.
Importance of green warehousing
Because supply chains are a major source of environmental impact in the consumer sector, sustainability in the industry can have a positive impact on the environment.
Importance of green practices for warehouses
As stakeholders demand that businesses reduce their carbon footprints, green practices become increasingly important for eco-friendly warehouses. They must keep up with government regulations, meet insurance requirements, and satisfy the demands of customers.
A green warehouse aims to lessen its environmental impact through practices such as an automated warehouse, lean warehousing, and green building.
Green warehousing to reduce a company’s environmental footprint
Companies can focus on decreasing the carbon footprint of their warehouses through various methods:
- Decreasing demand for electricity: Companies can accomplish this by reducing heating, cooling, and lighting demands, by generating power on site, or by taking advantage of energy management systems.
- Reducing waste: Companies can limit waste by ensuring efficient inventory management, going paperless, and using eco-friendly packaging.
- Building warehouses efficiently: By cutting back on the size of warehouses, building vertically, or using green building materials, companies can diminish their footprints on the land itself.
Goals of green warehousing
As a strategy, sustainable logistics aims to reduce environmental costs, resource waste, and business risks—moving the world toward a green economy. And with a strategic approach to supply chain sustainability in the warehouse, a company can accomplish many of its green goals.
The future of green warehousing
The warehousing industry continues to evolve, finding new ways to improve operations and reduce environmental impact. Green warehouses, whether new or retrofitted, have allowed leaders to emerge among warehouse operators, and the principles they use can help transform warehouses around the world.
Projected features of new green warehouses
New green warehouses prioritize efficiency and sustainability. Features of eco-friendly warehouses include the following:
- Recycling areas
- Solar panels or other power-generating features
- Xeriscaping and drought-tolerant plants
- Green building practices
- Skylights
- Roofs and walls that are appropriate for the climate
- Low-emitting paint
- Energy-efficient lighting
- Regionally sourced building materials
Leaders in the green warehouse movement
Warehouse operators that stand out in the warehouse industry for embracing green warehousing practices include many well-known brands. For example, retail and outdoor recreation services consumer cooperative Recreational Equipment Inc. designed a net-zero energy distribution center in Arizona.
Another outdoor apparel company, Patagonia, embraced sustainable concepts and materials for energy efficiency in its Nevada warehouse construction and expansion. And Amazon, an online retailer and cloud services provider with fulfillment centers worldwide, states that it is working to reduce greenhouse gas emissions and improve resource efficiency across the globe.
Conscientious companies, including Agility, operate under guidance from the United Nations’ Sustainable Development Goals to end poverty and protect the planet. Two of those goals promote affordable, clean energy and climate action, and both apply to green warehousing.
Tips for green warehousing
As you look for ways to create a more sustainable business, consider these green warehousing tips:
- Use natural or efficient lighting.
- Go paperless.
- Reduce warehouse waste.
- Reduce heating and cooling needs.
- Employ warehouse automation.
- Use eco-friendly packaging.
- Use green building materials.
After a difficult year of deaths and lockdowns, hope is finally on the horizon as the first COVID-19 vaccines appear on the market. The very first doses of the COVID-19 vaccine have already been administered, but full distribution of the vaccine to the global population—which will represent the largest vaccine procurement and supply operation in history—is yet to begin in earnest.
This operation will greatly impact every aspect of the global supply chain. There are a number of expected vaccine logistics shortages from COVID-19, from shipping container availability to cold chain supplies. And that’s not counting the many COVID-19-related challenges the supply chain is already facing, such as route disruptions and skyrocketing cargo rates.
This article will discuss the impact of the global COVID-19 vaccine distribution on supply chain logistics, including anticipated COVID-19 vaccine logistics, unique distribution challenges of COVID-19 vaccines, development of the COVID-19 supply chain, and how the vaccine could impact pharmaceutical supply chain logistics.
Anticipating COVID-19 vaccine logistics
The COVID-19 vaccine distribution effort is not yet in full swing, but it’s possible to anticipate how the logistics of the effort will work. Both national and global agencies have discussed putting into place coordinated distribution initiatives on an unprecedented scale, which will require the cooperation of supply chain agents and logistics providers.
The vaccine supply chain before COVID-19
Pre-COVID-19, the vaccine supply chain was an end-to-end system that was meant to ensure effective vaccine storage and handling, as well as strict temperature control in the cold chain. It has always been essential for the vaccine supply chain to run smoothly to ensure uninterrupted vaccine delivery to populations in need.
However, even before COVID-19, the World Health Organization (WHO) reported that national supply chains were struggling to manage the volume of new vaccines and to take advantage of improved vaccine supply chain technology like updated cold chain materials.
Necessary changes to the vaccine supply chain due to the COVID-19 vaccine
Moving forward, the vaccine supply chain cannot afford to get bogged down in supply chain issues like inadequate storage, transportation, and personnel capacity. This creates bottlenecks, and in the past has led to spoilage of many vaccines. A global coordination effort will be needed to optimize the supply chain for this crucial operation. Possible steps include the following:
- Standardization of all COVID-19 vaccine packaging to ensure proper fit within containers
- Coordination of vaccine deliveries based on the two necessary doses of the COVID-19 vaccine
- Maintenance of the COVID-19 accessory supply chain for supplies such as needles and alcohol swabs
- Open communication across all agents within the supply chain
How the COVAX initiative will affect the logistics of the COVID-19 vaccine
COVAX is the vaccines pillar of the Access to COVID-19 Tools (ACT) Accelerator, launched by the WHO, the European Commission, and France in April 2020. It is leading efforts to procure vaccines and distribute them to ninety-two lower-income countries, while also supporting procurement for more than ninety-seven upper-middle-income and high-income nations.
According to UNICEF, the United Nations agency responsible for providing humanitarian and developmental aid to children worldwide, these represent more than four-fifths of the world’s population. UNICEF, a COVAX member, is responsible for the transportation and supply chain piece of the COVID-19 vaccine distribution.
COVAX will allocate vaccine doses to participating countries, proportional to their total population size. To distribute the vaccines, UNICEF is working with manufacturers and partners in procurement, freight, logistics, and storage. UNICEF is well suited to handling the distribution, because it is the single largest buyer of vaccines in the world and already has longstanding expertise in procurement and logistics.
How large a project is the COVID-19 vaccination effort expected to become?
The COVID-19 vaccination effort will be the largest vaccine procurement and supply operation in history. The World Economic Forum (WEF) expects approximately six to seven billion doses of COVID-19 vaccines to be consumed in 2021. This accounts for nearly the entire global population of 7.8 billion people.
Europe, North America, and Asia are expected to consume the largest shares of the 2021 doses. The WEF projects that the largest inflows of vaccine doses will be to Asia, excluding China and India (820 million doses), and Africa (450 million doses).
How the COVID-19 vaccination effort will affect other health care logistics
The health care and pharmaceutical industries will experience logistical challenges as a result of the COVID-19 vaccination effort, because of the vaccine effort itself and also because of disruptions to the medical and pharmaceutical supply chain due to COVID-19 and vaccine distribution.
Air shipments to Africa and parts of Asia-Pacific will lead to an imbalance in normal air freight trade and diversion of aircraft to routes leading to hubs in those regions, which may impact other supply chains, including medical and pharmaceutical supply chains.
In addition, shipping and freight prices are high and volatile due to the impact of COVID-19 on the entire shipping industry: global air cargo capacity remains about 20 percent below prepandemic levels, mainly due to reduction in passenger flights and resulting shortage of widebody belly capacity, which is down nearly 70 percent. Also putting pressure on rates is the lack of natural backhaul cargo from Africa and other southern hemisphere destinations.
To improve the COVID-19 vaccine supply chain, the pharmaceutical industry could consider combining a distributed manufacturing approach with multiple manufacturing sites in different regions in order to minimize distribution needs. Shipment in less-than-container loads for transport by ocean could be a possibility. In addition, the pharmaceutical industry may also be able to save time by shipping the vaccines in bulk.
Unique distribution challenges of COVID-19 vaccines
Vaccines are among the most difficult cargo to transport due to their very particular temperature requirements, so we can expect significant challenges in shipping the COVID-19 vaccine. In addition, associated shipping materials may become in short supply, while the unprecedented scale of the vaccine distribution effort will strain the entire global supply chain. Logistics providers will need to strategize carefully to effectively transport vaccines to their destinations.
The role of cold chain logistics in the distribution of the COVID-19 vaccine
“Cold chain logistics” refers to the process of safely transporting temperature-sensitive products in the supply chain. Vaccines are among these cold chain products: according to Supply Chain Dive, they must be shipped at a temperature between -50 degrees and -15 degrees Celsius if frozen, or 2 to 8 degrees Celsius otherwise. Temperature stabilization is tricky in shipping, and unfortunately, a quarter of all vaccines are degraded by the time they reach their destination.
Eighty-three percent of COVID-19 doses will be normal cold chain products requiring storage at 2 to 8 degrees Celsius; roughly 17 percent will be ultra cold chain products requiring storage at lower temperatures.
Temperature-sensitive shipping often relies on dry ice. One significant challenge in the COVID-19 vaccine supply chain is that different types of passenger aircraft are limited in the amount of dry ice they can carry. The range is 180 to 950 kilograms, with most aircraft types limited to the lower end of the range.
Materials in demand for the successful distribution of the COVID-19 vaccine
As discussed above, temperature-controlled shipping materials are essential in the vaccine supply chain and thus will be highly in demand.
There are two options when it comes to cold chain shipping: active containers and passive containers. An active container has active temperature control, while a passive container is an insulated container with no active temperature control. Cooling packaging must be used in passive containers, and cooling materials such as dry ice may soon be in short supply due to high demand.
In addition, requirements for related cargo could be significant: one pallet of vaccine doses requires one truckload of syringes and related equipment. Shipping space will be even more in demand because of this additional cargo.
How will the sheer size of the COVID-19 vaccination effort impact logistics?
The COVID-19 vaccination effort will make the entire logistics landscape look very different than usual. COVID-19 vaccines will represent five times the air freight volumes for all vaccines in 2019, and the vaccines will represent 12 percent of the pharmaceutical industry’s total air freight volume in 2019. Industry groups estimate that global COVID-19 vaccine distribution will require the equivalent air freight capacity of 928 Boeing 747-400 aircraft.
To prepare for the coming changes in the logistics industry, Agility’s COVID-19 Response Team & Charter Desk has done detailed analysis of carriers for capacity, frequency, scheduling, routing, cost, flow type, dry ice constraints, lead time requirements, cancellation rules, and types of agreements (HB, SB, ad hoc/spot). We are also evaluating carriers based on their performance records, flexibility, and risk, as well as the likelihood they will increase rates.
Since major shipping hubs on the ground will certainly feel the strain in the supply chain as well, we have evaluated their ground handling capabilities, airport requirements and constraints, and nearby cold storage availability and options.
Agility has expanded its network of life sciences centers to thirty-two locations worldwide. In addition, we are leveraging our parent company’s global footprint and logistics assets, which include aviation and ground handling expertise and facilities, truck fleets, and workforce, as well as international-standard logistics parks in Asia-Pacific, the Middle East, and Africa.
Developing the COVID-19 vaccine supply chain
Agencies involved with vaccine distribution are aware that developing the vaccine was just half the battle; the other half is effective distribution, a massive challenge in itself. Task forces have been appointed for just this purpose, and these groups will need to address safety precautions in the vaccine supply chain, as well as ways to streamline the process.
The role of the WHO’s COVID-19 Supply Chain Task Force
The WHO’s COVID-19 Supply Chain Task Force is addressing shortages in essential supplies, including personal protective equipment, diagnostics, and medical equipment. It is taking a three-pronged approach to this challenge in the following ways:
- Establishing a global strategy to provide access to essential supplies
- Bringing together public and private partners to help meet those needs
- Ensuring the distribution of essential supplies and cargo
The WHO is pursuing these goals through the following methods:
- Consolidating demand to avoid overlap and demand amplification
- Coordination of procurement to aggregate volumes and get better access and pricing
- Forming allocation agreements based on need, country capacity, and vulnerability levels
- Forming a singular distribution network that allows movement of deliveries through established hubs around the world and to designated ports of entry worldwide
Safety precautions in the coronavirus vaccine supply chain
The biggest vulnerability in COVID-19 vaccine distribution is the possibility of temperature excursions. Vaccine manufacturers must use only temperature-regulated shippers and containers that are certified to meet the international regulations for temperature-controlled products.
At the same time, manufacturers will need to prepare for risks that arise during the shipping process. Companies will need to have a plan for rescuing vaccine shipments that are delayed in delivery, so that temperature excursions do not occur. Companies will also need to plan for a certain inevitable level of vaccine spoilage and damage incurred in the shipping process.
How the coronavirus vaccine supply chain can be streamlined
As a logistics expert, Agility recommends the following strategies for helping the COVID-19 vaccine shipping process go more smoothly:
- Identify and evaluate key lane pairs based on value and importance
- Engage in forward planning, forecasting, and building of stock levels
- Examine possible changes to shipping solutions to reduce volume and weight
- Increase cold chain packaging availability and develop backup plans with key suppliers
- Tighten alliances with strategic partners
How the COVID-19 vaccine could change pharma supply chain logistics
The COVID-19 vaccine distribution will have an unparalleled impact on pharmaceutical supply chain logistics. The vaccine will strain the supply chain more than perhaps any other pharmaceutical product in history. Due to the COVID-19 vaccine, the pharmaceutical supply chain will face certain geopolitical issues and a changed market outlook, at least in the near future.
How will the COVID-19 vaccine rollout change supply chain logistics for pharmaceutical companies and products?
Agility has been talking to various industry stakeholders, including clients, airlines, ground handlers, and packaging providers about the market outlook for pharma supply chain logistics. In short, no one yet has a clear picture.
These stakeholders are looking closely at the following factors:
- Timeline/duration and shipping cycles
- Vaccine availability/expected shipping volumes
- Vaccine transport requirements, including variation in temperature requirements for different vaccines
- Beyond temperature control requirements, the product has a relatively low monetary value, yet a high criminal value. The aspect of product safety cannot be neglected.
- The air market situation and the COVID-19 pandemic impact on equipment and capacity
Agility foresees challenges in equipment and supplies of containers, dry ice shippers, and dry ice itself. We also anticipate imbalances and return logistics challenges for containers. On the road freight side, capacity and drivers will become an issue.
What can the pharmaceutical industry learn from the global distribution of COVID-19 vaccines?
In addition to being a challenge, the COVID-19 vaccine distribution effort can also represent an opportunity for the pharmaceutical supply chain, especially in terms of future vaccine distribution. Never has there been such an impetus for the pharma supply chain to optimize and coordinate its operations on a global scale.
After the COVID-19 pandemic, the pharma supply chain will be able to take advantage of optimized operations that were developed out of necessity for COVID-19 vaccine distribution. It can continue to coordinate pharmaceutical packaging to ensure it fits optimally within containers. It can also utilize strategies developed for COVID-19 vaccine distribution to push more pharmaceuticals to hard-to-reach areas. Finally, it can keep the lines of communication open to ensure better transparency across the supply chain, which will help keep products at the necessary temperatures, leading to less vaccine wastage overall.
How could the pharma industry prepare for future disruptions to its supply chain?
In the future, pharmaceutical manufacturers can make their supply chains more resilient by diversifying their sources and suppliers. In many cases, this will mean lessening dependence on China, which accounts for 28 percent of manufacturing worldwide. Regional supply chains will emerge, reducing the dependency on a limited number of suppliers located in one geography.
The other major way to “future-proof” pharmaceutical supply chains is to rely more on digital capabilities such as predictive modelling, big data, and partner integration. The increased information and flexibility afforded by these technologies can make all the difference in a crisis situation.
The supply chain’s role in conquering COVID-19
The COVID-19 disease and vaccine will continue to impact the entire global supply chain for the foreseeable future. The supply chain is crucial to distributing the vaccine and finally seeing an end to the pandemic. For the sake of human health and safety worldwide, it’s essential for every party involved to understand the logistics issues inherent in COVID-19 vaccine distribution and to strategize properly for an organized, effective approach.
Agility is committed to helping agents at all points of the supply chain navigate the unique logistics challenges presented by COVID-19. Receive the latest COVID-19 global shipping updates here.
This article is part of the World Economic Forum Annual Meeting
- The number of potentially disruptive technologies in logistics is daunting.
- This makes it difficult for supply chain businesses to know where to look.
- Blockchain, IoT, automation and data science should be first on their list.
Astute business leaders discipline themselves to be on constant lookout for disruptive new technologies.
They foster an internal business culture that is able to evaluate promising technologies through a continuous cycle: Watch > pilot > partner > adopt or discard.
In logistics, as in many other sectors, the number of potentially disruptive innovations is daunting. It includes everything from augmented reality and big data to autonomous vehicles and 3D printing. Even the most agile businesses can’t test or pilot everything, so what’s the right approach?
For companies with goods to move, there are several technologies that bear watching and four that every party in the supply chain should be testing at some level. These four are the BIRD technologies – blockchain, the internet of things (IoT), robotic process automation (RPA) and data science.
The BIRD technologies are inter-related and mutually reinforcing. Blockchain, or distributed ledger technology, establishes trust in data. The IoT provides a vast quantity of relevant data points. RPA improves the accuracy of data. Data science extracts value.
1) Blockchain
Blockchain has its skeptics, including many who believe the technology has already fallen short and might be too inherently problematic. Some skepticism is justified, but it’s premature for blockchain to be written off.
The idea behind blockchain is that all of the information required for completion of a transaction is stored in transparent, shared databases to prevent it from being deleted, tampered with or revised. There is a digital record of every process, task and payment involved. The authorization for any activity required at any stage is identified, validated, stored and shared with the parties who need it.
In ongoing pilots of this technology, shippers, freight forwarders, carriers, ports, insurance companies, banks, lawyers and others are sharing “milestone” information and data about their pieces of an individual shipping transaction. What’s missing today is agreement by all the relevant parties in the supply chain – including regulators – on a set of common industry standards that will govern the use of blockchain.
Absent a consensus on standardization, blockchain offers little. But with a common framework and set of rules, it could make shipping faster, cheaper and more efficient by increasing trust and reducing risk. It would shrink insurance premiums, financing costs and transit times, and eliminate supply chain intermediaries who add cost today but who would become surplus to requirements.
2) The internet of things
As a platform for sharing trusted data, blockchain is ideally suited to the internet of things. IoT devices can be attached to almost anything. As 5G technology evolves and spreads, tiny IoT chips embedded in products will enable businesses to track and monitor shipments of pharmaceuticals, high-tech goods, consumer products, industrial machinery and garments.
That data can be encrypted and shared through the blockchain so that customers and suppliers have a real-time record of the transaction. An IoT-enabled supply chain would be both leaner and less risky. It would allow for true just-in-time production by guaranteeing inventory accuracy and, in turn, reducing working capital requirements.
3) Robotic process automation
Of course, data is no good if it is not accurate. In the supply chain, the leading cause of inaccuracy is human error. Robotic process automation, or RPA, is the artificial intelligence used to allow software to handle many of the steps involved in a shipping transaction by understanding and manipulating data, triggering responses and interacting with other digital systems.
Use of RPA can ensure accuracy in customs declarations, safety certificates, bills of lading and other paperwork. It can reduce reliance on the manually entered data, emails and digital forms that produce errors, create delays and add cost all along the supply chain. RPA frees up workers to be more productive by doing what humans do best: solve problems, react to the unexpected, think creatively and deal with customers.
4) Data science
Thanks to data science, we are in the midst of seismic change in the supply chain. We are getting more data from more sources; it is the right data; and it is accurate. Tools such as artificial intelligence, machine learning and cloud computing enable us to analyze and use that data in powerful new ways.
Rather than using information to sound alarms when there are “exceptions” – problems or anomalies with an individual shipment or in the supply chain – we can use it to prevent them. Data becomes about managing the future, not the present.
The risk, of course, is that only large, well-resourced supply chain players will be able to take advantage of BIRD technologies and other advances that involve harnessing data. That would create a dangerous new digital divide between large and small, haves and have-nots.
Thankfully, data is having a democratizing effect by making the global economy fairer and more inclusive in important ways. Small businesses and emerging markets companies aspiring to go global aren’t piloting blockchain or developing their own RPA applications. But they are already the beneficiaries of new, inexpensive, data-informed tools and platforms underpinned by artificial intelligence and machine learning: online freight booking, instant financing, automated marketing, cheap cloud computing and remote advisory services.
The BIRD technologies generate trust in data, ensuring accuracy and giving users the ability to predict and act. In a data-driven world, they can help businesses of all sizes take flight.
Since the outbreak of the COVID-19 pandemic, companies across virtually every goods-based industry have been re-examining their reliance on China, which accounts for roughly 28% of global manufacturing and is a leading source of critical commodities such as rare earth minerals and ingredients for pharmaceutical products.
The China re-think didn’t start with COVID-19
Well before the pandemic, many companies relying on Chinese producers for finished goods and parts were looking to de-risk by finding alternative suppliers in other countries. Why? Geopolitical tensions, trade disputes, and rising costs in China.
Trade tensions and national security concerns have led to a wave of legislation in the United States, where there are more than 60 bills pending in Congress aimed at changing economic relations with China. In addition, U.S. brands and manufacturers comparing China’s labor costs to those in Mexico have seen China’s labor costs rising faster. That has eroded China’s competitiveness and made Mexico more attractive.
Outward migration of production was underway before the pandemic because tariffs imposed by the U.S. and China had increased supply chain costs by up to 10% for as much as 40% of companies sourcing in China, according to Kamala Raman, a senior director analyst at Gartner.
The U.S., Germany, Japan and other countries have expressed strategic concerns about overreliance on China for critical products: 5G telecommunications gear, semiconductors, steel, cranes, electrical power equipment and more. McKinsey identified 180 different products for which one country — most often China — accounts for more than 70% of the global export market. Many of the products are chemicals and pharmaceuticals.
Intel recently divested itself of a business in politically sensitive memory chips because the business was heavily dependent on China sales. Samsung and others have cited cost considerations for production moves or asset sales.
The pandemic is turning concern to action
China’s assertive response to the pandemic included lengthy, mandatory lockdowns that froze manufacturing and stranded global cargo shipments for several weeks in the spring of 2020. That caused unprecedented disruption in supply chains and led to shortages of everything from household goods and consumer electronics to industrial components and healthcare products.
The pandemic exposed the fragility of sprawling global supply chains. In one recent survey, one-quarter of businesses sourcing from China indicated plans to transition all or some of their operations to other countries over the next three years. In a Gartner survey, an even higher percentage – 33% — said they intend to pull manufacturing or sourcing out of China in the next two to three years. Sixty-four percent of North American manufacturing and industrial professional said they were likely to bring manufacturing production and sourcing back to North America, in a Thomas Publishing survey.
Look for knock-on effects
Any exodus from China will ripple around the world so expect huge and uneven consequences in other markets. The modest movement to other production and sourcing locations has already led to overheated labor markets and infrastructure bottlenecks in other Asian manufacturing countries.
In some cases, the effort to build supply chain resilience is felt most in far off warehousing and distribution hubs, where companies are adding safety stock or shifting from just-in-time inventory to beefed up “just-in-case” models.
Sourcing diversification is altering the flow of goods into U.S. ports. West Coast ports continue to have a lock on ocean traffic from China and serve as the primary gateway for Chinese goods. But now East Coast ports are receiving higher volumes of containerized ocean goods because, in addition to vessels traversing traditional routes from Europe, the Mediterranean and the Caribbean, they receive cargo from Vietnam, Thailand, Malaysia and India, which have found it economical to ship via the Indian Ocean and Suez Canal.
In turn, the shift toward the East Coast has driven up industrial real estate prices along the eastern seaboard of the U.S. as companies scramble to set up distribution hubs and e-commerce facilities.
Japan is pushing an ‘Exit China’ strategy
At least 87 Japanese companies have shuttered production in China, moving it back home to Japan or relocating to Southeast Asian countries in response to incentives offered under the Japanese government’s $2 billion Exit China program. Nikkei Asia says Japanese companies “wary of rising labor costs in China and geopolitical factors had already begun reorganizing production prior to the pandemic.”
Japanese investment in Southeast Asian manufacturing – specifically in Vietnam, the Philippines, Malaysia, Indonesia and Thailand – was already increasing at twice the rate of investment in China.
It’s not just China
Supply chain risk has been rising for years as costly disruptions become regular occurrences.
McKinsey says weather disasters alone accounted for 40 separate incidents involving damage in excess of $1 billion in 2019. Add the risk from trade disputes, retaliatory tariffs — and a doubling of cyberattacks in a single year at a time when companies are increasing their reliance on digital systems.
Geopolitical risk is unavoidable. Today, 80% of trade involves countries with declining stability scores. “Companies can now expect supply chain disruptions lasting a month or longer to occur every 3.7 years, and the most severe events take a major financial toll,” McKinsey says.
Agility’s Take
Economic trauma caused by COVID-19 will initially shrink the universe of suppliers, not expand it. And new layers of protectionism will leave companies with even fewer choices of supply because they will rob efficient producers — in China and elsewhere — of their competitiveness and make them too expensive.
Uprooting from China is not as easy as it seems. Forty years after it began modernizing, China today holds advantages available nowhere else: unmatched scale; abundant skilled and unskilled labor; sophisticated automation, engineering and sciences; world-class infrastructure and logistics; closely synchronized and integrated supplier networks both in-country and across Asia.
Twenty-five years ago, leaving China meant leaving a low-cost manufacturing center. Today, for some multi-nationals, it would mean giving up on the world’s largest consumer market and an economy growing at twice the rate of the United States before the COVID-19 crisis.
Willy Shih, a Harvard Business School professor, says: “There’s a lot of impatience about this supply chain resilience and reshoring. I like to remind people that it took 20 to 25 years for China to capture the supply chain for many products. And if you want to move the supply chain, we’re not talking about something that will happen in a year, or in a couple of years.”
- When the pandemic dies down, trade protectionism will become the biggest threat to global supply chains.
- This will both drive up prices and make resiliency harder to achieve.
- Accelerated digitalization and uptake of new technologies can help firms find a balance between supply chain resiliency and efficiency.
Seven months into the COVID-19 pandemic, businesses of all kinds are devising ways to protect themselves from future shocks by making their supply chains more resilient. In doing so, they need to guard against the mistake of preparing for the last battle rather than the coming one.
At some point, hopefully soon, the unprecedented global response to COVID-19 will reduce it to a manageable threat that allows us to return to something approximating normalcy in our personal and professional lives.
When that occurs, the greatest immediate and long-term risk to supply chains won’t be a virus. It will be trade protectionism, which was resurgent even before the COVID crisis, and now threatens to choke off the lifeblood we need to speed us toward recovery.
As recently as 2016, trading nations were erecting fresh barriers – subsidies, tariffs, quotas, licensing requirements and other obstacles – at twice the rate they were adopting measures to liberalize trade, according to Global Trade Alert. By 2018, new obstacles outpaced liberalizing steps by three to one. Last year, the ratio was four to one, and the value of global merchandise trade fell by 3%, the first decline since 2015.
Since the start of the COVID-19 crisis, we have seen protectionism intensify. Some emergency moves are clearly temporary. They were put in place by governments to ensure access to the medicines, machines and protective equipment required to contain or treat the virus. In other cases, the aim was to guarantee adequate food supplies for local populations.
Yet these new measures and others have been taken against a backdrop of simmering trade tensions between the world’s two largest economies, the US and China, and a growing chorus of voices in the US, Germany and other countries calling to re-shore, nationalize or find alternative sources for key products and industries such as 5G wireless equipment, semiconductors, steel, electrical power gear, mobile cranes, rare earth minerals and other goods.
The 164-nation World Trade Organization (WTO), normally the body that would quell trade wars and bolster the global consensus for free trade, has been weakened, perhaps fatally, by a loss of faith in its dispute resolution system and the apparent withdrawal of US support.
“In the current alternate universe we’re living in, global trade is collapsing and the WTO and the liberal order itself are in a true existential crisis,” Bloomberg noted in June.
As economies around the world emerge, unevenly, from the pandemic, we can expect demand to begin to strengthen. As it does, trade flows, carrier schedules and inventory levels will start to normalize, and supply and demand will find a new equilibrium.
But normalization won’t mean a return to normal. The World Bank expects a 5.2% contraction in global GDP in 2020. Advanced economies could shrink by as much as 7%, although they are likely to recover faster than economies in emerging or developing countries, the bank says.
Trade, which has accounted for 54% to 60% of global economic activity in recent years, is set to retreat even further. The WTO forecasts a drop in global trade flows of 13% to 32% in 2020. UNCTAD expects trade to decline by 20%. For context, the largest quarterly decline in trade volume during the 2008 financial crisis was 5%.
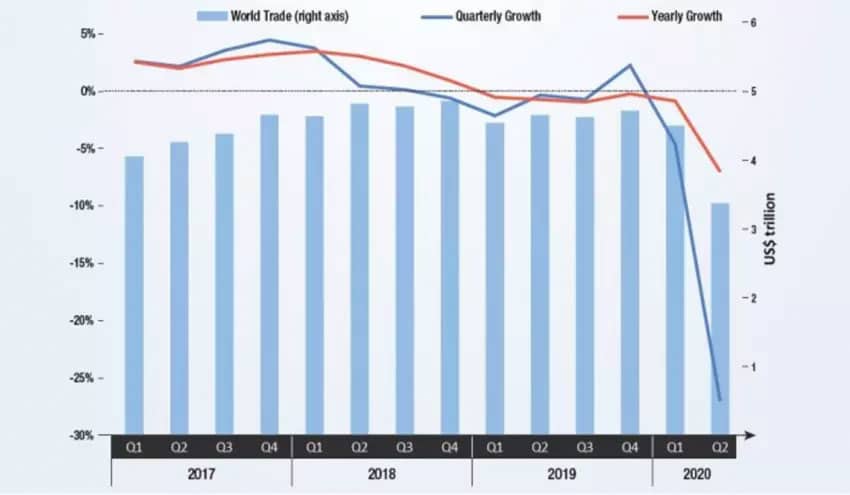
Image: UNCTAD
The new wave of protectionism, which includes a sharp rise in the use of international economic sanctions and penalties, will significantly increase the cost of goods at a time when we are experiencing historic levels of joblessness, poverty, and business failures on every continent.
Protectionism is likely to make supply chain resiliency harder to attain, not to mention more costly.
The first step toward resiliency is diversification of sources and suppliers. For many, that means reducing reliance on China, which accounts for 28% of global manufacturing.
Yet the economic trauma caused by COVID-19 will shrink the universe of suppliers, not expand it. And new layers of protectionism will leave companies with even fewer choices of supply because they will rob efficient producers – in China and elsewhere – of their competitiveness and make them too expensive.
Simply uprooting from China is not as easy as it seems. Forty years after it began modernizing, China today holds advantages available nowhere else: unmatched scale; abundant skilled and unskilled labour; sophisticated automation, engineering and sciences; world-class infrastructure and logistics; closely synchronized and integrated supplier networks both in-country and across Asia. Twenty-five years ago, leaving China meant leaving a low-cost manufacturing centre. Today, it would mean giving up on the world’s largest consumer market and an economy growing at twice the rate of the US before the COVID-19 crisis.
Other attempts to build resiliency also defy easy answers. For instance, businesses that see the pandemic as a reason to beef up future inventory through the addition of “safety stock” will probably think differently when the historically low cost of capital begins climbing.
Once the COVID-19 threat recedes, businesses across virtually all industries will have to find a new balance between efficiency and resiliency, because the latter carries a cost. Rather than trying to ‘deglobalize’ or shorten the physical length of far-flung supply chains, they should consider the resiliency offered by accelerated digitalization and deeper integration of technology.
From its earliest days, the pandemic separated digital leaders from laggards. Leaders had tools that gave them accurate visibility into supplier status, orders, shipments and inventory. They could make data-driven decisions quickly because they had trusted supply chain partners – especially freight forwarders and third-party logistics providers (3PLs) – sharing fresh information in near real-time and hunting down available production and shipping capacity. Laggards floundered and continue to flounder.
One obvious lesson from the pandemic is that digital capabilities such as predictive modelling, big data and partner integration are driving business flexibility. When things are relatively stable, those digital capabilities provide a competitive advantage. In times of disruption, they give companies the ability to optimize schedules, ports, modes, vendors and other variables, adjusting on the fly to events that could otherwise prove calamitous, even ruinous.
True resiliency means being ready for any kind of disruption: political, economic, cyber, conflict-based or, yes, pandemic-related. Knowing where to find it is what will separate tomorrow’s leaders from laggards.
Originally published on the World Economic Forum’s Agenda blog
By Biju Kewalram, Chief Digital Officer, Agility GIL
Accurate data and effective supply chain technology are more critical now than ever before. Data-driven decision making is enabling organizations to flex their supply chains to cope with rapid fluctuations in supply, demand and transportation. And as companies and countries attempt to “build back better” from the crisis, lowering carbon emissions has risen up the agenda, and smarter supply chains are an important lever.
Ten years ago, this simply wouldn’t have been possible. Over the last decade, a number of technologies have emerged, with the combined potential to revolutionize the way we move products around the globe.
We’re now moving into the stage of validation and implementation – accelerated by the current crisis – when the whole industry must push past R&D and into the industrial execution of smart systems. This stage will be critical in terms of bringing about actual, sustainable change.
What could the industrialization of these technologies mean for both businesses and consumers, and how can the businesses that haven’t yet implemented them catch up?
The four key technologies driving change in the supply chain are blockchain, the internet of things (IoT), robotic process automation (RPA) and data science (BIRD).
Blockchain generates data trust by enabling all players in a network to share a single (encrypted) database. Anyone with access can track the status and location of a shipment and, more importantly, identify opportunities for efficiencies on a larger scale than has been previously possible.
IoT technology is essential for gathering a vast number of data points. By implementing a system of smart sensors, stakeholders can accurately track sensory data (e.g., location, moisture, temperature, shock), reliably calculating arrival times and proactively responding to disrupted shipments.
RPA improves data accuracy in the chain by substituting human input (and resulting error potential) with software robots that update data within applications by reading them from other applications. This closes the “data confidence gap” when a chain of data updates is required (as in supply chains) to complete the visibility picture.
Data science is the key to unlocking this collective data value and making smarter decisions. Advanced machine learning is continuing to evolve, and AI will one day be used at each stage of the supply chain, although we are some way off this yet. In the meantime, setting up shared databases and making common inferences should be the focus.
What Are The Next Steps?
Now is the time to think about how these technologies can be transformed into deliverable solutions.We’ve spent a long time researching these revolutionary technologies, but only by starting to incorporate them into existing processes can we unlock their full potential.
Organizations at the front of the curve have been analyzing how these exciting digital solutions fit into their businesses, and at our company, we’ve supported a few pilots of certain technologies with clients who are eager to move their companies forward.
So what are the key considerations when piloting new technologies?
Start Small
With a number of technologies waiting to be tested, companies must take an agile, experimental approach. Rather than endeavoring to carry out large-scale trials across the whole organization, businesses should start by implementing the technology in a specific part of the process and gradually scale it up. Working in this way will allow trials to be integrated into day-to-day operations, quickly and effectively gathering firsthand data on multiple technologies.
Consider Your Team
Selecting the right team is vital to running a successful pilot. Ideally, you want a mix of experts who can provide insight on how the technology can be applied to a specific part of the process and the impact this will have on wider business operations. They must also have the analytical skills needed to evaluate the findings and report back to stakeholders. Most importantly, they must be passionate about innovation.
Partnering For Co-Creation
Carrying out individual pilots is one thing, but companies must push the boundaries of cocreation to test these technologies on a larger scale. Any change to the process will have knock-on effects along the supply chain, and the success of many technologies will depend on strong communication. Running pilots with trusted partners of different sizes will allow companies to analyze the adaptability of new technologies. Partners will need to start by agreeing on the problem they are trying to solve and the method they are going to use, as well as how they will measure success and share findings.
Our company’s partnership with electrified trucking company Hyliion is an example of how companies can collaborate to create a more efficient, greener supply chain. We’re helping the company with its long-haul, fully electric powertrain — the HyperTruck ERX. It can achieve a net-negative greenhouse gas emissions footprint using renewable natural gas, and the system’s machine learning algorithm further optimizes energy efficiency, emissions, performance and predictive maintenance schedules.
Gauging Success
Before embarking on a pilot, companies must set out some clear performance indicators and decide on a system for recording results. New technology may show promise for a specific task, but can it be scaled up? What impact would it have on costs, revenue and customer satisfaction? Approaching trials scientifically will help to determine the long-term value these technologies could have in terms of business performance.
Many pilots will inevitably encounter problems, but these experiences are still valuable. A comprehensive debriefing process is necessary to identify whether a failure was due to a weakness in the product or the process and whether these problems could be ironed out through further testing.
Of course, with the logistics industry evolving rapidly, there is no fixed end to the experimentation process. Companies that adopt this systematic approach with an analytical eye and a resilient attitude will thrive in the big data revolution. Organizations must be willing to disrupt their current processes and collaborate because partnerships will be crucial for implementing new technology and making digital supply chain dreams a reality.
This blog first appeared in Forbes