By Biju Kewalram, Chief Digital Officer, Agility GIL
Accurate data and effective supply chain technology are more critical now than ever before. Data-driven decision making is enabling organizations to flex their supply chains to cope with rapid fluctuations in supply, demand and transportation. And as companies and countries attempt to “build back better” from the crisis, lowering carbon emissions has risen up the agenda, and smarter supply chains are an important lever.
Ten years ago, this simply wouldn’t have been possible. Over the last decade, a number of technologies have emerged, with the combined potential to revolutionize the way we move products around the globe.
We’re now moving into the stage of validation and implementation – accelerated by the current crisis – when the whole industry must push past R&D and into the industrial execution of smart systems. This stage will be critical in terms of bringing about actual, sustainable change.
What could the industrialization of these technologies mean for both businesses and consumers, and how can the businesses that haven’t yet implemented them catch up?
The four key technologies driving change in the supply chain are blockchain, the internet of things (IoT), robotic process automation (RPA) and data science (BIRD).
Blockchain generates data trust by enabling all players in a network to share a single (encrypted) database. Anyone with access can track the status and location of a shipment and, more importantly, identify opportunities for efficiencies on a larger scale than has been previously possible.
IoT technology is essential for gathering a vast number of data points. By implementing a system of smart sensors, stakeholders can accurately track sensory data (e.g., location, moisture, temperature, shock), reliably calculating arrival times and proactively responding to disrupted shipments.
RPA improves data accuracy in the chain by substituting human input (and resulting error potential) with software robots that update data within applications by reading them from other applications. This closes the “data confidence gap” when a chain of data updates is required (as in supply chains) to complete the visibility picture.
Data science is the key to unlocking this collective data value and making smarter decisions. Advanced machine learning is continuing to evolve, and AI will one day be used at each stage of the supply chain, although we are some way off this yet. In the meantime, setting up shared databases and making common inferences should be the focus.
What Are The Next Steps?
Now is the time to think about how these technologies can be transformed into deliverable solutions.We’ve spent a long time researching these revolutionary technologies, but only by starting to incorporate them into existing processes can we unlock their full potential.
Organizations at the front of the curve have been analyzing how these exciting digital solutions fit into their businesses, and at our company, we’ve supported a few pilots of certain technologies with clients who are eager to move their companies forward.
So what are the key considerations when piloting new technologies?
Start Small
With a number of technologies waiting to be tested, companies must take an agile, experimental approach. Rather than endeavoring to carry out large-scale trials across the whole organization, businesses should start by implementing the technology in a specific part of the process and gradually scale it up. Working in this way will allow trials to be integrated into day-to-day operations, quickly and effectively gathering firsthand data on multiple technologies.
Consider Your Team
Selecting the right team is vital to running a successful pilot. Ideally, you want a mix of experts who can provide insight on how the technology can be applied to a specific part of the process and the impact this will have on wider business operations. They must also have the analytical skills needed to evaluate the findings and report back to stakeholders. Most importantly, they must be passionate about innovation.
Partnering For Co-Creation
Carrying out individual pilots is one thing, but companies must push the boundaries of cocreation to test these technologies on a larger scale. Any change to the process will have knock-on effects along the supply chain, and the success of many technologies will depend on strong communication. Running pilots with trusted partners of different sizes will allow companies to analyze the adaptability of new technologies. Partners will need to start by agreeing on the problem they are trying to solve and the method they are going to use, as well as how they will measure success and share findings.
Our company’s partnership with electrified trucking company Hyliion is an example of how companies can collaborate to create a more efficient, greener supply chain. We’re helping the company with its long-haul, fully electric powertrain — the HyperTruck ERX. It can achieve a net-negative greenhouse gas emissions footprint using renewable natural gas, and the system’s machine learning algorithm further optimizes energy efficiency, emissions, performance and predictive maintenance schedules.
Gauging Success
Before embarking on a pilot, companies must set out some clear performance indicators and decide on a system for recording results. New technology may show promise for a specific task, but can it be scaled up? What impact would it have on costs, revenue and customer satisfaction? Approaching trials scientifically will help to determine the long-term value these technologies could have in terms of business performance.
Many pilots will inevitably encounter problems, but these experiences are still valuable. A comprehensive debriefing process is necessary to identify whether a failure was due to a weakness in the product or the process and whether these problems could be ironed out through further testing.
Of course, with the logistics industry evolving rapidly, there is no fixed end to the experimentation process. Companies that adopt this systematic approach with an analytical eye and a resilient attitude will thrive in the big data revolution. Organizations must be willing to disrupt their current processes and collaborate because partnerships will be crucial for implementing new technology and making digital supply chain dreams a reality.
This blog first appeared in Forbes
Making every mile count
Revolutionizing logistics with digital freight matching
What if you could streamline your business, bolster productivity and slash your environmental impact?
Digital technologies are gaining traction in supply-chain logistics, unleashing a wave of efficiencies and unlocking multiple side benefits. In addition to boosting revenue and slashing operational costs, innovations like digital freight matching are reducing emissions, bolstering productivity and creating a more sustainable industry.
Using transport management software to match a vehicle’s capacity to nearby waiting shipments offers great potential, since lorries and trucks keep the global economy moving. In the US alone, they handle more than 70% of all freight tonnage.
Here are some of the key benefits offered by digital freight matching, which uses online and mobile technology to connect shippers who have cargo to drivers and trucking companies looking for loads:
1. Fewer empty trucks
Empty miles cost money. About 20% of the distance driven by US truckers is non-revenue generating, according to a report by the American Transportation Research Institute. Many industry experts say the actual number could be even higher.
By marrying the cargo to the truck as accurately as possible, applications that offer digital freight matching help eliminate these empty miles, boosting profitability while also lowering emissions and reducing the carbon footprint of the supply chain.
2. Better use of space
In the same way that they help to eradicate empty miles, digital freight tools can also make sure cargo space is being used in the most efficient way. Even experienced shippers can struggle to get the most out of the space on offer in each container and get the best return on investment.
Digital freight matching algorithms quickly calculate the optimal way for loads to be carried, helping drivers ensure they have cargo to carry in both directions before they set off – and all but eliminating the wasteful empty “back-haul.”
One company operating in Saudi Arabia offers a template of how this can work. There, 40% of trucks complete the return leg of their journey completely empty, costing the economy around $5 billion every year, according to the digital platform Homoola, which has financial backing from Agility.
“Knowing how big the inefficiencies were in the traditional way of doing things, we could see the enormous potential of a digital solution that made load-carrying more efficient,” Homoola’s co-founder Ziyad Alhomaid says.
3. Less time waiting
Using the technology in this way also cuts out the time drivers spend sitting idle while waiting for cargo. Connected systems facilitate planning that reduces loading, unloading and clearance logjams at ports and warehouses. In addition to a cost benefit, there’s a huge environmental upside, since an idling engine can produce up to twice as many exhaust emissions as an engine in motion. That releases a range of air pollutants including carbon monoxide, nitrogen dioxide, and other particulate matter.
4. More efficient fleets
Using digital freight matching technology allows firms to accurately estimate the numbers of vehicles and drivers required, not only for a given shipment, but also over a longer period. This enables them to right-size their fleets and driver pools, potentially saving significant amounts of money.
5. Less traffic on the roads
Cutting out unnecessary journeys reduces congestion and emissions. Any technology that helps reduce the number of heavy goods vehicles will have an instant environmental impact. In the UK alone, they are estimated to account for around 17% of greenhouse gas emissions from road transport and more than 20% of road transport nitrogen oxide emissions, while making up just 5% of all vehicle miles.
6. Paperless deliveries
Documentation associated with shipping often mounts up. Digital freight matching apps allow this to migrate to the cloud, saving time, money and energy, instantly cutting waste.
“Shipments often come with a lot of paper,” says Homoola’s Alhomaid. “We’re reducing this on the carrier side, as well as for shippers, and working towards a paper-free solution. It saves time, money, energy – and the environment.”
7. More transparent pricing
Technology can also aid price negotiations, letting both sides see a range of different prices, in real time, at the click of a button. Faster, more liquid transactions conducted via an app can be beneficial to both sides.
In 2016, US businesses spent more than $1 billion on logistics, much of which was procured in long-term contracts of more than six months, according to a report by the consultancy firm A. T. Kearney. Signing lengthy commitments is a financial risk for both the shipper and the carrier, whereas a more dynamic market – created by digital freight matching – helps to mitigate these risks because both parties have a better handle on fuel prices, surcharges, tolls, taxes, tariffs, driver’s rates and other costs that they will incur.
Such tools also improve transparency, visibility and comparability of pricing structures, and can be updated in real-time.
8. Stronger safety standards
In the same way that it bolsters pricing transparency, digital freight matching also gives better visibility to the documentation that’s involved in the industry and can help make the safety aspect less opaque. Driver certifications and safety records can be made easily accessible and readable on mobile devices. In time, distributive ledgers could also create instantly shareable records.
At any given time, for example, a shipper can see a truck’s location, have transparency over the associated costs, and gain insights into important points like on-time delivery. Certificates and records are accessible to all who need them, whenever they’re needed.
For Homoola co-founder Asim Alrajhi, this safety aspect goes together with enhancing quality control.
“It’s a fragmented market,” he says. “Things are done on the phone rather than digitally, and often there’s no quality assurance.” While digitalization is still at an early stage, the market in trucking is set to balloon to around $80 billion by 2025, up from around $11 billion currently, according to estimates from market research firm Frost & Sullivan, which also predicts digital freight brokerage will make up the lion’s share of that.
Once such technologies are adopted, they will improve predictability, speed, transparency and sustainability. This will ultimately result in the seamless delivery of any item, anytime, anywhere at a lower economic and environmental cost.
How to integrate new technology into your supply chain
Let’s assume you’re sold on the promise of the digital supply chain. A brave new world awaits if you commit to best use of rapid technological advances. The big question now is how to integrate these innovations into your business.
In our Guide to a Digital Supply Chain, we outlined why an agile approach, based on scalable pilot programs, is essential to evaluating new technologies in a way that is fast, efficient and cost-effective. Here, we will show what that looks like in practice.
Choose your evangelists
Choosing your team is just as important as deciding which technologies to test. The right people will have a mix of the technical knowhow needed to exploit the technology, a broad understanding of how the business operates, and the emotional intelligence to collaborate and communicate effectively with stakeholders.
This is a rare combination – people who possess those traits are to be treasured. More likely, you will create a small team whose members collectively bring these traits. Ideally, this team will represent a cross-section of your business, so that each member approaches the pilot with a different set of questions and priorities.
The job of this team is to evangelize change, so you need personalities excited by change, rather than team members who see change as a threat. If a pilot shows promise, you need people who can spread it wider, scale it up, and convince reluctant colleagues of its benefits.
You will want a mix of subject matter experts, operational personnel and systems integration specialists. Ask yourself what contributions and expertise you will need not just to run a pilot but also to evaluate its success, and then select accordingly. Consider also whether your choices will be able to cope with a fast pace of work in addition to their normal day jobs, and whether they have the interpersonal skills to work well with partners.
Small is beautiful
There are many reasons to keep initial pilots small – starting with the cost. Very few companies can afford unlimited R&D spend, and large-scale trials are expensive. The point of an agile, empirical approach is to try many things to see which work best, so a series of smaller, cheaper tests will tell you a lot more than a complex and expensive pilot.
Small pilots are also easier to integrate into the normal running of your operations, by limiting disruption, and the number of people involved. Change is hard for most people, so the fewer who need to have their daily routines changed for an experiment, the less resistance the pilot team will encounter.
Small pilots can also adapt quickly to different variables. For example, it might become clear very early that the particular IoT device you are testing to track consignments isn’t accepted on your preferred air cargo partner. A small pilot involving one customer’s deliveries could experiment both with changing IoT devices and with trying a different airline with limited ramifications.
Learning by failing
Most successful pilots can start small, then scale up. But you will also learn from the pilots that fail.
Embracing failure may not come naturally, but it is essential. The simple fact is that many, and perhaps most, of the pilots that you launch will run into serious obstacles. The teams will need to decide whether to persevere with the current solution, try again with a new approach, or move on to the next project. Remember the wisdom from the old ballad “The Gambler” by Kenny Rogers: “You got to know when to hold ‘em, know when to fold ‘em, know when to walk away, know when to run.”
Honest appraisals of why a pilot didn’t work will reveal a great deal about both the technology and the way your own organization is operating. All the knowledge gained should be shared and factored into the design of future pilots, in a constant iteration. Work out in advance how to capture what has been learned. A comprehensive debriefing process is essential.
Failure isn’t final. In any debrief, you should ask yourself whether an unsuccessful pilot is worth trying again and, if so, when – for example, when the technology reaches a certain price point or when a supplier’s or customer’s technical sophistication reaches a certain level.
Picking your partners
In the supply chain, no improvement can be made entirely in isolation. How your suppliers and customers adapt to the changes you make, and vice versa, will determine the success of the chain as a whole.
In Agility’s experience, collaborating on pilots is a win-win. But your partners need to share common goals and agree the following questions: What problem are we trying to solve? How much do we want to invest in finding a solution? Are we prepared to walk away without recrimination if the pilot is not a success? How far are we willing to share what we have learned with the other parties?
If the answers to those questions don’t match, then this might not be the right pilot.
It is also important to run pilots with different types of partners – something that worked well with a local family business might not scale up when applied to a large corporation. Agility collaborates with the full range: from an IoT cold storage pilot with a small firm specializing in one particular cargo in one market, to trials of blockchain with IBM and Maersk.
Don’t rest on your laurels
An experiment doesn’t end when a pilot shows promise. In fact, that is when the hard work begins – working out how to scale the pilot up and what other aspects of your business it can be applied to.
Constant experimentation can be draining, so communication is vital to bringing your workforce with you on your transformation. Strong leaders need to articulate why innovation is necessary, explain the journey, and inspire people to believe that the gain is worth the pain. But they also need to listen to concerns such as increased workload or a fear that their jobs may disappear as a result of the new technology. Anticipate these concerns and have a plan – the hardest part of getting new technology to work is people.
What success looks like
To judge success or failure, you need clear KPIs agreed in advance. A pilot may work in an operational sense, but will you actually extract value from the technology? What are the implications in terms of costs, revenue, customer satisfaction, staffing levels etc? Defining these parameters in advance will stop people getting carried away by a shiny new toy that may not be as cost-effective as it appears.
At Agility, we are constantly running pilots. We evaluate not only the four core technologies that we believe are at the heart of the digital supply chain – blockchain, Internet of Things, Robotic Process Automation, and Data Science [link to each article] – but a watchlist of 16 technologies, ranging from machine learning and the Cloud to 3D printing, virtual reality, autonomous vehicles and drones.
The template for every pilot is the same:
- First define what success will look like, by identifying the key business outcomes we are looking for
- Analyze exactly what we did, and what we found, at each stage of the pilot
- Decide on the next steps, who will be responsible for carrying them out, and the timeframe
- Identify the risks encountered on the way, and what can be done to mitigate them
Using this scientific approach, you can find the technologies that will give you the competitive edge to thrive as the digital supply chain becomes a reality.
Data science can predict the future
The car you drive is the product of one of the most complex logistical endeavours ever attempted. Tens of thousands of components and raw materials criss-cross the world to get to the right place at the right time for each vehicle to roll off the production line.
Holding spare stock costs money, so manufacturers prefer to rely on steady supplies of parts that are delivered exactly when they are needed. But the “just-in-time” model that underpins the automobile industry is vulnerable. Unexpected delays can have far-reaching and costly knock-on effects all the way along the supply chain.
The old saying that “for the want of a nail, a kingdom was lost” resonates in an industry where the want of a container of ball bearings can do serious damage to an automaker’s bottom line. But what if the company shipping that container knew that the usually reliable route would take too long this time, and automatically switched it to a quicker alternative?
Any tool that can predict when and where delays might happen, and work out ways to avoid them, will be extremely valuable. People cannot take into account every single one of the extraordinary number of variables affecting a sophisticated supply chain. Data science can.
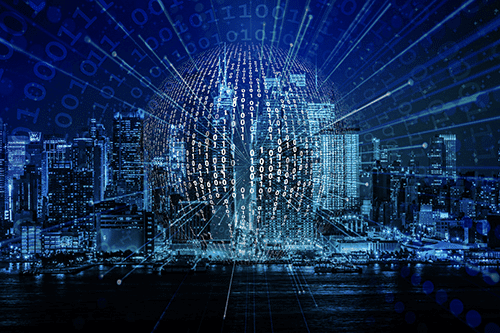
What is data science?
Data science involves analyzing information from the past and present, and using it to predict the future. And it isn’t new. Individuals and companies have long used ledgers, spreadsheets and computers to identify trends and spot potential problems and opportunities.
But the digital revolution is allowing data science to grow beyond anything seen before. Technologies such as the Internet of Things (IoT) are providing unprecedented quantities of data and track goods in real time as they move along the supply chain. Blockchain allows companies to trust that the data they are using (for example that a product has left a warehouse) is genuine and secure. Robotic Process Automation, or RPA, is eliminating errors from the data, guaranteeing its accuracy.
The result is data that gives a very detailed picture of the world. Using machine learning, computers can sift the information, looking for patterns. When a pattern is repeated often enough, it can be used as a guide to what is likely to happen in the future.
Why does it matter for supply chain?
Uncertainty is damaging to every part of a supply chain. But for shipping companies themselves it can be fatal. Competitive pricing depends on correct estimates of the costs incurred. If you estimate too high, you risk being outbid. If you estimate too low, you will lose money on the delivery.
Reputation is extremely important to shipping companies. Customers rely on the promises we make in order to run their businesses. If those promises are broken, the crucial bond of trust is weakened. As supply chains become ever more sophisticated, data science will be essential for accurate pricing and ensuring that the promises made will be kept.
Although cost and speed are the decisive factors in many deliveries, other considerations are becoming more important too. Political and economic volatility make the security of a supply chain ever more important. An increased awareness of the environmental cost of transporting goods means that emissions and carbon footprint are becoming key factors in deciding routes.
Data science allows shipping companies to account for new pieces of information, such as a change in a security situation or new environmental regulation, much more quickly. The same reaction speed also means new markets and routes can be evaluated sooner.
Opportunities…
Knowing what the optimal route will be is one thing. Acting on that information is another. This is where artificial intelligence (AI) can play a role.
AI is the use of computers to react to data in the same way a human would. If a warehouse manager knows that a spilled load has caused a logjam at the site entrance, he might want to alert incoming trucks to postpone their collection, and warn the next link in the chain to expect a delay. But will he have the time to call each driver while he’s sorting out the spill?
AI systems can be programmed to immediately alert all the relevant links in the chain. A truck that was due to collect from the warehouse can be diverted to another delivery until the site has been cleared. The aircraft that would be waiting for its consignment can be loaded with an alternative cargo.
AI could also work out a new route for the delayed consignment that falls within tailored parameters. When does the delivery actually need to be at its final destination? Is it a perishable good that means speed is paramount? Or is a low carbon cost the most important factor?
The efficiency dividend of this kind of AI could be enormous. Avoiding bottlenecks in real time will ultimately drive down the cost, improve the speed, and mitigate the environmental implications of the entire logistics and supply industry.
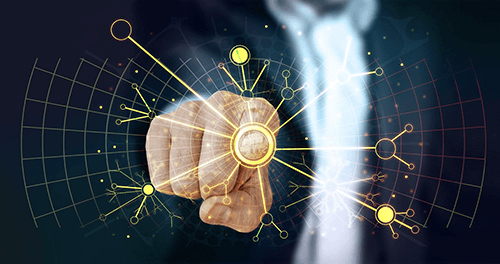
…and challenges
To make the kind of AI described above possible demands a high level of integration and interoperability. Data from multiple sources needs to be stored in a way that is accessible to all the relevant parties. This requires common standards and procedures so that different systems can effectively talk to each other.
The question of data ownership is controversial, and has not yet been resolved. Who, if anyone, can own the data? Who decides who can use it, and how? For example, take the case of tracking a shirt with an embedded IoT device from factory to retailer. Is the tracking data owned by the owner of the shirt? When does ownership of the shirt switch? Or does the data belong to the shipping company that is actually doing the tracking? Can the shipper use it to create proprietary business models? What happens to the data if the factory switches shipping companies? And whose rules apply in trade routes that span multiple countries?
These questions can only be answered as part of a broader global discussion. In the meantime, companies should ensure that they are compliant with data regulations that apply to any country jurisdiction they do business with. The EU’s GDPR laws are increasingly being seen as a gold standard that other countries will follow.
The final challenge is how to ensure AI responds in the right way. It is possible for computers to find patterns in data that are circumstantial, and have no predictive value at all. That means AI systems need to be monitored and evaluated.
Where now?
Data science is already playing a leading role in designing, managing and monitoring supply chains for bigger companies. Cloud computing is quickly making the technology cheaper and accessible to all. Shipping companies like Agility are already integrating advanced machine learning and AI into end-to-end services that are affordable for any customer, for example with our Shipa brand.
The data science revolution isn’t coming – it’s here already, and everyone can take part.
What we are learning
The greatest impact we’re seeing so far is in risk management. Until now, shippers have been using data to manage their “exceptions” – those instances when something in the supply chain goes wrong.
The next frontier is predictive analytics that allows shippers to address problems before they occur. That includes demand forecasting based on social media trends, consumption figures and other data to remove spikes and troughs in the supply chain and eliminate inventory bottlenecks.
Reaping the rewards of Robotic Process Automation
Two ships carrying identical cargoes have just docked at a busy port.
One shipment experiences the usual delays and frustrations. A customs declaration for one container mistakenly refers to 1000 units rather than 100. One item of cargo has the wrong safety certificate. Some of the delivery addresses are incorrect, leading to confusion with the truck dispatchers. One consignment has the wrong parts because somebody misread a decimal place.
The mistakes are eventually sorted out, but it takes time and money.
The second shipment clears the port with no errors. All the information is 100% accurate. Why? The supply chain has been managed with robotic process automation.
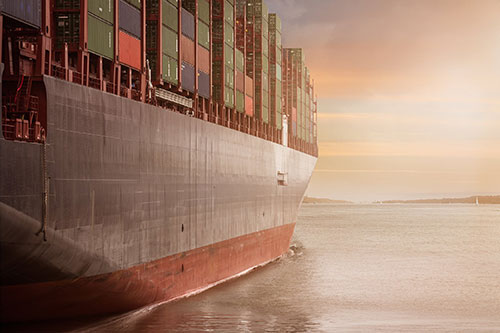
What is robotic process automation?
Robotic process automation, or RPA, does not involve robots as they exist in the popular imagination.
RPA is the use of software to carry out repetitive tasks that we do on computers. Increasingly, it is having a dramatic effect on costs, productivity, and accuracy.
The supply chain involves a vast amount of paperwork and manually entered data – emails and digital forms. Purchase orders, invoices, cargo manifests, customs declarations, delivery dockets, warehouse inventories – all necessary documents to ensure that the right package gets to the right place at the right time, in line with all relevant regulations.
Inputting data and generating the right documents is time-consuming, monotonous work. When people do the same task again and again, they inevitably make mistakes – because they are tired, bored, overworked, or unmotivated.
But machines don’t make those mistakes. Rules-based, repetitive work is ideal for a computer. It can carry out the same task 24 hours a day, doing exactly what it has been programmed to do without errors.
Why does it matter?
Businesses are under constant pressure to reduce overhead. Hiring people and training them on complex IT systems is expensive. When the work those people are doing is largely drudgery, it doesn’t just lead to errors: It is a waste of a valuable resource – the skills, talent and experience of that worker.
RPA can free employees to do more of the things that humans excel at and computers don’t: problem solving, reacting to unexpected events, creative thinking, and dealing with other people. Individual employees are not only more productive, but they experience greater job satisfaction, and are less likely to leave for other jobs.
Studies have shown that robotic process automation can make back-office operations up to ten times faster, and cut average costs by 37%.
Opportunities…
Many back-office jobs have been outsourced to external providers in an effort to minimize costs. But the efficiency savings of this trend are tailing off, partly as a result of growing wages in many of the countries where jobs have been transferred. Outsourcing the work also involves reputational risk: mistakes and poor-quality service by external providers and third-party contractors can have a damaging effect on a company’s brand.
RPA gives companies the opportunity to bring much of this work back in house. Improved customer service can pay huge dividends in supply chains where trust is a significant factor in deciding who to work with.
As the accuracy of data improves, more can be done with it. Combining RPA with data provided by technologies such as the Internet of Things (IoT) will allow companies to build highly accurate models of supply chains. Gaps in the market, and potential problems, can be identified, Companies which make the right use of this data will have significant competitive advantages.
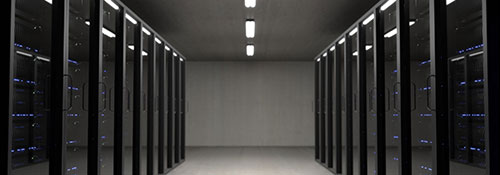
…and challenges
Designing an automated process for a particular task using a particular interface is relatively simple. But when different IT systems and interfaces are used, making sure that one program can understand the data provided by another is more complicated.
Even within individual companies, IT systems can vary widely. The warehouse may be run on an entirely different operating system from the accounts department. In a complex supply chain with multiple stakeholders, this problem is amplified dramatically.
For RPA to achieve its full potential, systems need to be integrated enough to allow data to be transferred seamlessly from one end of the chain to another. This means companies must consider what systems their partners use. Compatibility will be a key factor in any decisions about upgrading systems to avoid expensive mistakes.
Robotic processes will do exactly what they are told to do with the data they are given. Although more sophisticated systems can spot anomalous information, there will always be a need for people to monitor and improve processes to ensure the desired outcome.
Where now?
RPA is already being used across the industry. But in many organizations, it is deployed in silos. Many companies have already automated their invoicing, and also their delivery operations. But most have done so separately – the two systems don’t work with each other.
Agility is looking to integrate these processes all the way along the supply chain. End-to-end services like our Shipa brand are designed to make logistics easier and cheaper. This kind of business is ideal for RPA – ensuring the right goods get to the right place with the minimum of fuss.
What we are learning
At multiple points in the supply chain, the movement of freight is still reliant on manual data entry. But even limited deployment of RPA is exposing how those points so often become points of failure.
The most rapid adoption of RPA to date involves forwarders and carriers using it to automate event tracking and to bridge gaps between systems that require data transfer. Watch for faster, broader take up as the heavy cost of continued reliance on manual entry becomes clearer.
Warehousing is in the midst of a tech-driven revolution as companies race to identify and adopt emerging technologies that cut costs, optimize operations and improve overall supply chain efficiency. In some of the largest economies and companies, warehouse drones and robots already have been employed.
It’s not just logistics giants who are adopting innovative tech-based solutions. With the cost of automation falling, increasing numbers of SMEs and startups are investing in these efficient technologies. The top nine technologies shaking up the traditional warehousing scene:
1. Drones
Small maneuverable drones are appearing in warehouses as companies around the world seek to automate inventory and asset management. With stock stored up to ceilings as high as 12 meters in many warehouses, hard-to-reach barcodes have traditionally meant hours of labor using equipment such as forklifts and ladders. Scanner-carrying drones increase speed and accuracy by navigating warehouse shelves and taking automatic registry of stock. RFID tags can be read and located through cameras from a distance of 10m. Still needed are advancements that allow numerous drones to navigate tight spaces without colliding.
2. Robots
Robots are a game changer. They are programmed to guide themselves and to pick and pack orders into waiting carts or trucks. Some warehouses have already made the shift to full automation through use of robots. The distribution warehouse at online British supermarket Ocado uses thousands of robots to pack groceries into individual boxes. The robots run on complex algorithms that teach them where to pick up inventory and guide them to the exact grocery bag to drop it into, all while making sure that they don’t collide as they roam around filling orders.
3. Better Batteries
Batteries might not seem directly linked to warehousing, but they can power the machines that facilitate warehouse operations. So how can the latest innovations in battery technology advance warehousing?
Advancements in lithium-ion power cells have created impressive battery lives that can last up to ten years before needing to be replaced. Tesla’s latest batteries focus on alternative and affordable energy sources, drawing on solar power and energy from nearby power grids. Just think how powerful, efficient and cost effective robots, electric forklifts and other warehouse machines could be if they utilized these battery technologies. Heating and cooling warehouse space can consume large amounts of energy, so using improved batteries to power these systems could also mean significant savings on this front.
4. 3D Printing
3D printing could shake-up the entire global supply chain by bringing manufacturing closer to consumers and other end users. Take the example of auto parts now made in Asia for vehicles assembled in Mexico and sold in the United States. Production of some parts is likely to move closer to the market to cut down on shipment times and costs. 3D printing could reduce costs associated with complex trade and customs red tape for vast amounts of goods, because they could just be printed on demand near their final destination.
5. Automated Guided Vehicles
Automated Guided Vehicles (AGVs) differ to robots because instead of operating more autonomously they follow guided routes around warehouses. A huge advantage of AGVs is that they replace forklift trucks, so it’s not necessary to change the basic configuration of a warehouse. AGVs are also designed to come to a safe stop if they run into anything. This increases efficiency as AGVs can run continuously without breaks. AGVs are expected to become practical in even the smallest distribution centers, such as those of SMEs, as their cost continues to decrease.
6. Cloud Technologies
As with other industries, cloud storage is revolutionizing the productivity of warehousing as the instantaneous and self-updating systems cut down maintenance, infrastructure and the labor costs associated with the upkeep of management systems. Cloud technologies are also user-friendly and can be used by all employees, leaving companies less vulnerable if highly-skilled tech workers move on.
7. On-demand Warehousing
The “uberization” of warehousing – on-demand warehousing – is an emerging way of buying warehousing services and space on a pay-per-use basis. This method of warehousing gives customers more choice and flexibility over location, cost and supplier, either as a complete substitute to owning warehouses, or as partial replacements when new warehousing locations become necessary. The biggest disadvantage logistics companies face when adopting on-demand warehousing is that they’re exposed to fluctuating market rates for space, which is often overpriced in locations near ports, airports, rail spurs, major roads and urban centers.
8. Internet of Things
Internet of Things (IoT) technologies are not new on the logistics scene, and devices such as wearables, sensors and radio-frequency identification tags (RFID) are already used in many warehouses. By communicating relevant information to other IoT devices, the technologies reduce human error and the need for manual labor. Warehouse managers also get real-time visibility of order fulfillment, allowing them to process goods more efficiently.
Security concerns have blocked some of these advancements from reaching their potential, but a number of emerging technologies are being developed to enhance the safety of applying IoT sensor technology to large logistics operations. Microchips that allow more efficient encryption are one of the innovations that will ease security concerns about adopting the IoT in warehousing, and drastically increase efficiency in the future.
9. Composite Panel Technology
Clever developments in the construction and maintenance of warehouses are set to optimize insulation, air-tightness and durability through the use of new materials in composite panels. The latest panel technology can improve warehouse energy efficiency by around 20%. The cost and emission savings will be especially important in cold-storage facilities such as chilled and frozen food warehouses, where maintaining the correct temperature requires significant resource.
Composite panel technology is set to have global impact on the logistics supply chain: not only does it increase sustainability, it can also decrease warehouse build time and costs by one fifth.
How the Internet of Things will revolutionize your supply chain
A batch of vaccines leaves a pharmaceutical company bound for another continent. Each of the thousands of tiny vials has the potential to save a child’s life. But only if the contents of the container are kept chilled throughout the long journey.
From the moment it is driven away from the loading dock, the batch is being tracked. A chip is recording its location, and whether it is being kept upright. Crucially, the chip is also monitoring the temperature of the vaccines. From refrigerated lorries, cargo holds and warehouses, the chip feeds this information back to both the manufacturer and the medical center that has placed the order. Doctors and medical staff can see where the vaccines are and when they will arrive, certain they are in perfect condition. They can plan an immunization campaign that will keep a village free from a deadly disease for a generation.
All this is possible thanks to the Internet of Things.
What is the Internet of Things?
When we hear about the Internet of Things (IoT), we usually think of smart household appliances that can communicate with a network – for example fridges that keep track of their contents.
But IoT devices can be attached to almost anything. As 5G technology becomes more widespread, tiny chips are able to relay a huge amount of data. These chips could be sewn into the collar of a shirt, embedded to a table leg, or attached to the cardboard packaging of a coffee mug. Anything that you want to track can be tracked.
They can report location and state awareness (temperature, humidity, tilt, etc). The data can be accessed from anywhere in the world in real time – alerting anyone who needs to know about delays, detours, unexpected stops and accidents.
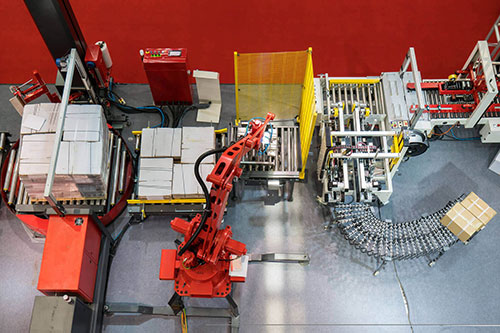
Why does the IoT matter for supply chain?
For the supply and logistics industry, knowing where the goods are and what state they are in is vital. Huge amounts of time and money are spent logging and tracking consignments, with the reputation of the shipper on the line every time a delivery does wrong. Because supply chains typically involve multiple providers and subcontractors, trust is essential.
IoT devices allow complete visibility. A shipping company will be able to keep track of every stage of the process. There will be no opportunity for products to go astray, be tampered with, or even be replaced by counterfeit goods. Shippers can guarantee quality and security, and keep all stakeholders informed about the progress of the delivery at all times.
Opportunities…
The potential benefits of IoT are enormous.
Data from IoT devices can be encrypted and shared using blockchain, so that customers and suppliers have a real-time record of a transaction as it progresses. This will facilitate instant payments and reduce the need for lines of credit.
Inventory management will be transformed. There is no need for time-consuming and costly stocktakes when there is a guaranteed accurate and reliable record of every item entering and leaving a warehouse.
The data provided by millions of objects travelling all over the world can be analyzed to identify optimal routes. Delays and bottlenecks can be predicted. And different options can then be tailored to each customer depending on priorities: cost, speed, security, and carbon footprint.
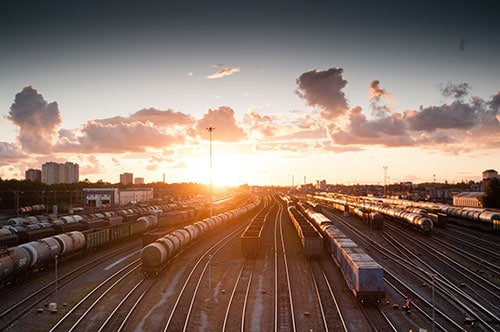
…and challenges
There are two major considerations that will affect IoT in the supply chain: disposability and privacy.
For the former, the question is simple – what do you do with the IoT devices and chips when the item has been delivered?
Currently, most of the IoT devices being used for pilots and trials in the supply chain need to be returned to providers, which is expensive and time consuming. However, the cost of the individual devices and chips is falling rapidly. Discarding chips would create vast amounts of electronic waste and is not sustainable in the long run. Recycling schemes, whether run by transport companies themselves or third parties are likely to be an essential part of the business before long.
There are also privacy concerns about whether an item could continue to be tracked once it has been passed to the consumer. How do you know the chip in your TV or even shirt is no longer active? The industry will need to collaborate to establish safeguards and protocols that can win the trust of the public.
Where is the IoT now?
IoT technology is already being used to track deliveries.
Agility has operated successful pilots with several partners, that have proved the value and efficacy of the technology. We have overcome practical issues such as ensuring IoT devices can be used on commercial cargo aircraft.
There are also a number of companies that offer IoT tracking devices for individual deliveries, such as Roambee.
As 5G is rolled out worldwide, there will be no technical barriers to the widespread adoption of IoT as a standard. High value items, and those that need close temperature monitoring such as pharmaceuticals and fresh or frozen food, are naturally the most likely early adopters. But within a few years, anything that customers or suppliers decide they want to track, will be tracked.
What we are learning
The big lessons in trials with customers are, first, that IoT without a corresponding data strategy is only half the story. IoT expands the data points available to shippers, but without a contextual data science strategy, the data is of little use.
Another lesson is that there is a larger-than-anticipated degree of compliance – whether with governments and regulatory authorities or with transport providers such as airlines – that has to be factored in.
For shippers, the next step is demonstrating where they can extract value from the data. That means using it to generate predictive analysis that strengthens their supply chain.
When a shirt is shipped from China to a shop in Europe, it passes through a complicated and sometimes slow supply chain, involving many different parties, manual data entry and a stack of paper documents.
What’s more, the retailer needs to trust that the shirt is on its way, and usually needs to make payment before it arrives.
Now imagine that the shirt is embedded with an intelligent chip and can be tracked using distributive ledger technology.
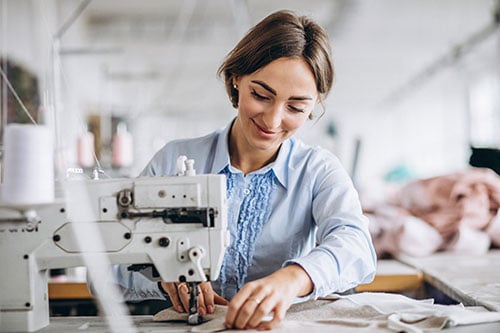
As it leaves the factory, it sends a digital signal that it’s on its way. Since this data is recorded in the blockchain, it is secure, immutable and can be trusted by all parties – no one needs to double check or verify that the shirt is on its way.
The retailer can pay for the shirt with assurance that it’s in transit, and the sender can instantly verify that the right person is collecting or receiving the goods.
In short, it’s faster, cheaper and more efficient way to send an item around the world.
This is how blockchain could change the face of logistics: by fostering trust between all parties and eliminating the need to manually track shipments, sign documentation and verify payments.
What is Blockchain?
Blockchain was made famous as a platform to trade cryptocurrencies like Bitcoin. But it has many uses beyond digital money. It is a secure record of transactions, a ledger, in which all data can be publicly verified and shared.
Offering a new way to send, store and verify information, the technology has trust at its core. Its secure, scalable and decentralized nature means its applications are potentially limitless. It could change the way we process and store health records as well as revolutionizing the way we shop, save and invest.
All that means the global blockchain market will be worth $23 billion by 2023, up from around $1 billion in 2018, according to MarketsandMarkets research.
Why does blockchain matter?
Blockchain technology has the potential to make shipping and logistics cheaper, safer and more reliable. It can be used to verify and store information all along the supply chain, as well as connecting different parties, giving them access to data and real-time tracking of goods as they move around the globe.
By embracing it, the industry could lower costs and ease friction. Documentation and administration are estimated to be one-fifth of the $1.8 trillion spent annually to move goods across borders.
What opportunities do Blockchain bring?
The key benefits of blockchain are speed, transparency and security. This generates a high level of trust in a transaction, unleashing a powerful tool for the logistics industry, where transactions involving many different parties and milestones are common.
For example, a very simple supply chain involves the shipper, banks, an assembly manufacturer, parts suppliers, modal carriers, port authorities, freight consolidators, customs officials and many others. It’s easy to see the potential for blockchain in this scenario, enabling the shipper to unlock access to specific information for specific parties, while retaining complete visibility of the whole process.
By enshrining trust in a transaction, there’s no need to verify documents and timestamps, to certify authenticity, or to deliver certificates, streamlining every step in the pathway.
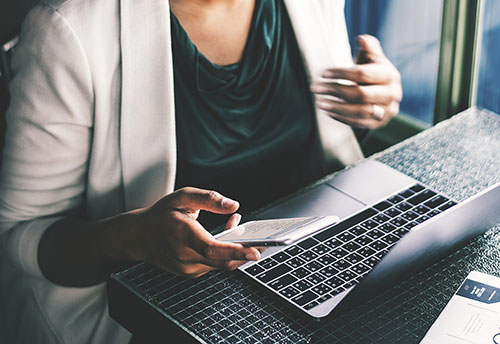
What are the challenges with Blockchain?
Even so, blockchain requires a collaborative approach, and one the industry might not yet be ready to embrace. To unleash its full potential, it needs the buy in and understanding of everyone along the supply chain, as well as agreement on a common approach and standards.
And without a critical mass, the risk is that too many providers try to create their own platform, meaning the results are disjointed.
Another challenge is the potential for a skills shortage. Finding and employing the right people with the necessary skills is essential to bridge the gap between those companies that have the knowledge and the technology in place, and those that don’t.
Fostering experimentation and collaboration will be key to success.
How does blockchain related technology apply to our current needs?
As discussed, distributive ledger technology is ready to go and has the potential to revolutionize our industry. Once a common approach is agreed, adopted, and achieved, its game-changing nature is likely to be unstoppable.
Agility is leading the conversation on how best to harness the potential of blockchain – helping our customers conduct pilots and working together to figure out the best ways forward.
We’ve already teamed up with Maersk-IBM to manage and track container shipments using blockchain, by identifying events associated with individual shipments and sharing information about them via the distributed ledger technology.
In this way, costs can be reduced, trade can be made more efficient, and standards can be set for an industry-wide adoption. Our aim is to help our customers understand how to use blockchain to improve shipment visibility, eliminate paperwork, reduce errors, and shorten transit times.
Blockchain could also help improve safety. Agility is part of a consortium of industry leaders exploring blockchain’s role in mitigating accidents and serious incidents onboard container ships.
Wrongly classified or inaccurately identified dangerous cargo leads to fires and other accidents that result in millions of dollars in losses, ship damage and delays in supply chains. Nearly a quarter of all serious incidents on containerships were attributable to mis-declared cargo, according to the Cargo Incident Notification System. It’s easy to see how blockchain could play a role in continuously tracking and monitoring what’s inside containers and reduce these risks.
Even as these examples show how blockchain is set to change the world, our industry is lagging behind. By recognizing the full potential of the technology and collaborating to foster experimentation, Agility is ready for the disruption that’s in train, and will be prepared when the pace of change accelerates.
What are we learning about Blockchain?
Use of blockchain for shipping remains largely in the pilot and concept stage for the moment. That’s likely to remain the case until there is wider industry participation that creates a tipping point.
Companies developing blockchain solutions are trying to figure out how to monetize a technology that requires so many participants to create an ecosystem. They need to incentive early adopters who can create more use cases and scale the number of transactions taking place with blockchain.