How Better Warehouses Increase Trade in Africa
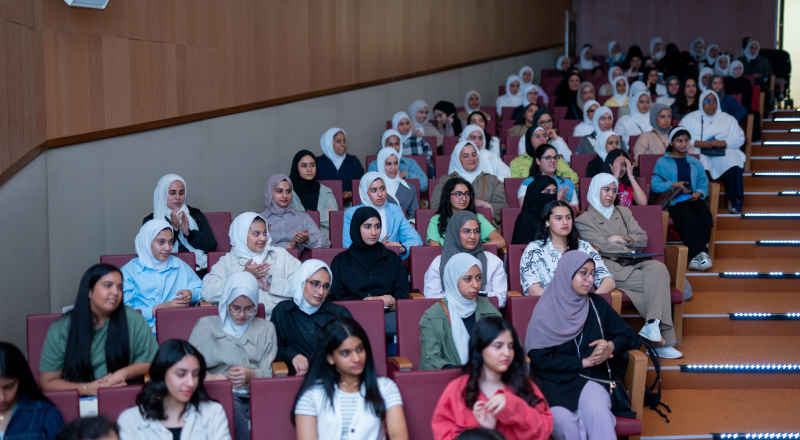
Kuwait-based Agility Logistics Parks customers can log-on to view contracts and make payments.
UK MOD personnel can log-in to the GRMS portal to schedule household relocation shipments.
Kuwait-based Agility Logistics Parks customers can log-on to view contracts and make payments.
UK MOD personnel can log-in to the GRMS portal to schedule household relocation shipments.
Warehousing is in the midst of a tech-driven revolution as companies race to identify and adopt emerging technologies that cut costs, optimize operations and improve overall supply chain efficiency. In some of the largest economies and companies, warehouse drones and robots already have been employed.
It’s not just logistics giants who are adopting innovative tech-based solutions. With the cost of automation falling, increasing numbers of SMEs and startups are investing in these efficient technologies. The top nine technologies shaking up the traditional warehousing scene:
Small maneuverable drones are appearing in warehouses as companies around the world seek to automate inventory and asset management. With stock stored up to ceilings as high as 12 meters in many warehouses, hard-to-reach barcodes have traditionally meant hours of labor using equipment such as forklifts and ladders. Scanner-carrying drones increase speed and accuracy by navigating warehouse shelves and taking automatic registry of stock. RFID tags can be read and located through cameras from a distance of 10m. Still needed are advancements that allow numerous drones to navigate tight spaces without colliding.
Robots are a game changer. They are programmed to guide themselves and to pick and pack orders into waiting carts or trucks. Some warehouses have already made the shift to full automation through use of robots. The distribution warehouse at online British supermarket Ocado uses thousands of robots to pack groceries into individual boxes. The robots run on complex algorithms that teach them where to pick up inventory and guide them to the exact grocery bag to drop it into, all while making sure that they don’t collide as they roam around filling orders.
Batteries might not seem directly linked to warehousing, but they can power the machines that facilitate warehouse operations. So how can the latest innovations in battery technology advance warehousing?
Advancements in lithium-ion power cells have created impressive battery lives that can last up to ten years before needing to be replaced. Tesla’s latest batteries focus on alternative and affordable energy sources, drawing on solar power and energy from nearby power grids. Just think how powerful, efficient and cost effective robots, electric forklifts and other warehouse machines could be if they utilized these battery technologies. Heating and cooling warehouse space can consume large amounts of energy, so using improved batteries to power these systems could also mean significant savings on this front.
3D printing could shake-up the entire global supply chain by bringing manufacturing closer to consumers and other end users. Take the example of auto parts now made in Asia for vehicles assembled in Mexico and sold in the United States. Production of some parts is likely to move closer to the market to cut down on shipment times and costs. 3D printing could reduce costs associated with complex trade and customs red tape for vast amounts of goods, because they could just be printed on demand near their final destination.
Automated Guided Vehicles (AGVs) differ to robots because instead of operating more autonomously they follow guided routes around warehouses. A huge advantage of AGVs is that they replace forklift trucks, so it’s not necessary to change the basic configuration of a warehouse. AGVs are also designed to come to a safe stop if they run into anything. This increases efficiency as AGVs can run continuously without breaks. AGVs are expected to become practical in even the smallest distribution centers, such as those of SMEs, as their cost continues to decrease.
As with other industries, cloud storage is revolutionizing the productivity of warehousing as the instantaneous and self-updating systems cut down maintenance, infrastructure and the labor costs associated with the upkeep of management systems. Cloud technologies are also user-friendly and can be used by all employees, leaving companies less vulnerable if highly-skilled tech workers move on.
The “uberization” of warehousing – on-demand warehousing – is an emerging way of buying warehousing services and space on a pay-per-use basis. This method of warehousing gives customers more choice and flexibility over location, cost and supplier, either as a complete substitute to owning warehouses, or as partial replacements when new warehousing locations become necessary. The biggest disadvantage logistics companies face when adopting on-demand warehousing is that they’re exposed to fluctuating market rates for space, which is often overpriced in locations near ports, airports, rail spurs, major roads and urban centers.
Internet of Things (IoT) technologies are not new on the logistics scene, and devices such as wearables, sensors and radio-frequency identification tags (RFID) are already used in many warehouses. By communicating relevant information to other IoT devices, the technologies reduce human error and the need for manual labor. Warehouse managers also get real-time visibility of order fulfillment, allowing them to process goods more efficiently.
Security concerns have blocked some of these advancements from reaching their potential, but a number of emerging technologies are being developed to enhance the safety of applying IoT sensor technology to large logistics operations. Microchips that allow more efficient encryption are one of the innovations that will ease security concerns about adopting the IoT in warehousing, and drastically increase efficiency in the future.
9. Composite Panel Technology
Clever developments in the construction and maintenance of warehouses are set to optimize insulation, air-tightness and durability through the use of new materials in composite panels. The latest panel technology can improve warehouse energy efficiency by around 20%. The cost and emission savings will be especially important in cold-storage facilities such as chilled and frozen food warehouses, where maintaining the correct temperature requires significant resource.
Composite panel technology is set to have global impact on the logistics supply chain: not only does it increase sustainability, it can also decrease warehouse build time and costs by one fifth.